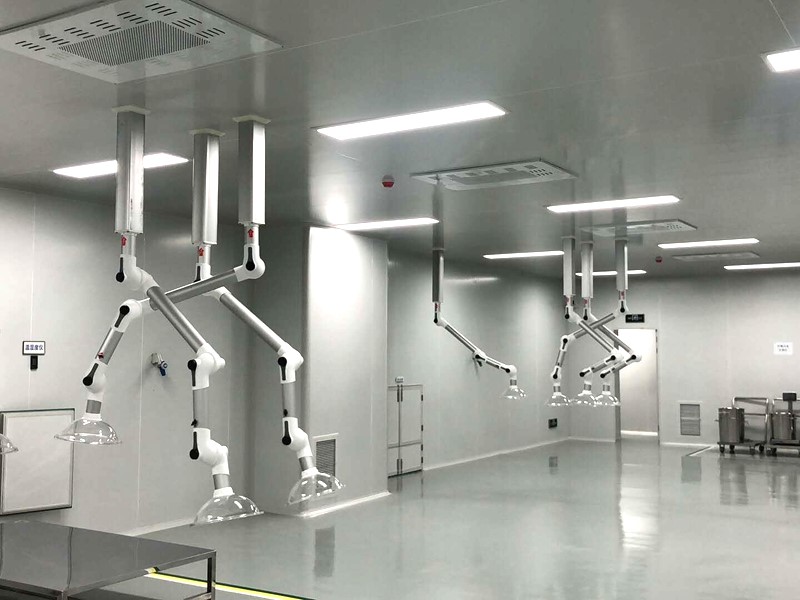
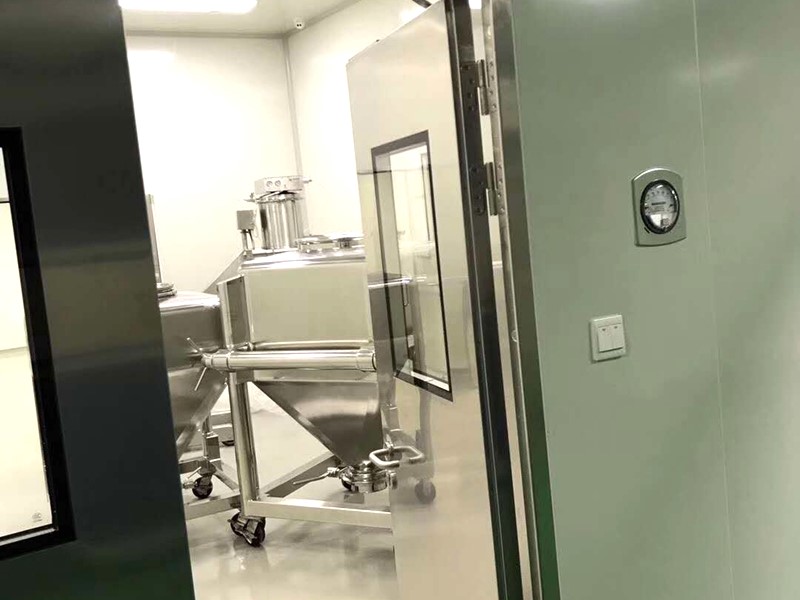
Clean room project has clear requirements for clean workshop. In order to meet the needs and ensure product quality, the environment, personnel, equipment and production processes of the workshop must be controlled. Workshop management includes management of workshop staff, materials, equipment, and pipelines. Production of work clothes for workshop staff and cleaning of the workshop. Selection, cleaning and sterilization of indoor equipment and decoration materials to prevent the generation of dust particles and microorganisms in clean room. Maintenance and management of equipment and facilities, formulating corresponding operating specifications to ensure that equipment operates as required, including purification air conditioning systems, water, gas and electricity systems, etc., ensuring production process requirements and air cleanliness levels. Clean and sterilize facilities in clean room to prevent the retention and reproduction of microorganisms in clean room. In order to better carry out clean room project, it is necessary to start from clean workshop.
The main workflow of clean room project:
1. Planning: Understand customer needs and determine reasonable plans;
2. Primary design: Design clean room project according to customer's situation;
3. Plan communication: communicate with customers on primary design plans and make adjustments;
4. Business negotiation: Negotiate clean room project cost and sign contract according to determined plan;
5. Construction drawing design: Determine primary design plan as construction drawing design;
6. Engineering: Construction will be carried out in accordance with construction drawings;
7. Commmissioning and testing: Conduct commissioning and testing according to acceptance specifications and contract requirements;
8. Completion acceptance: Carry out completion acceptance and deliver it to customer for use;
9. Maintenance services: Take responsibility and provide services after warranty period.
Post time: Jan-26-2024