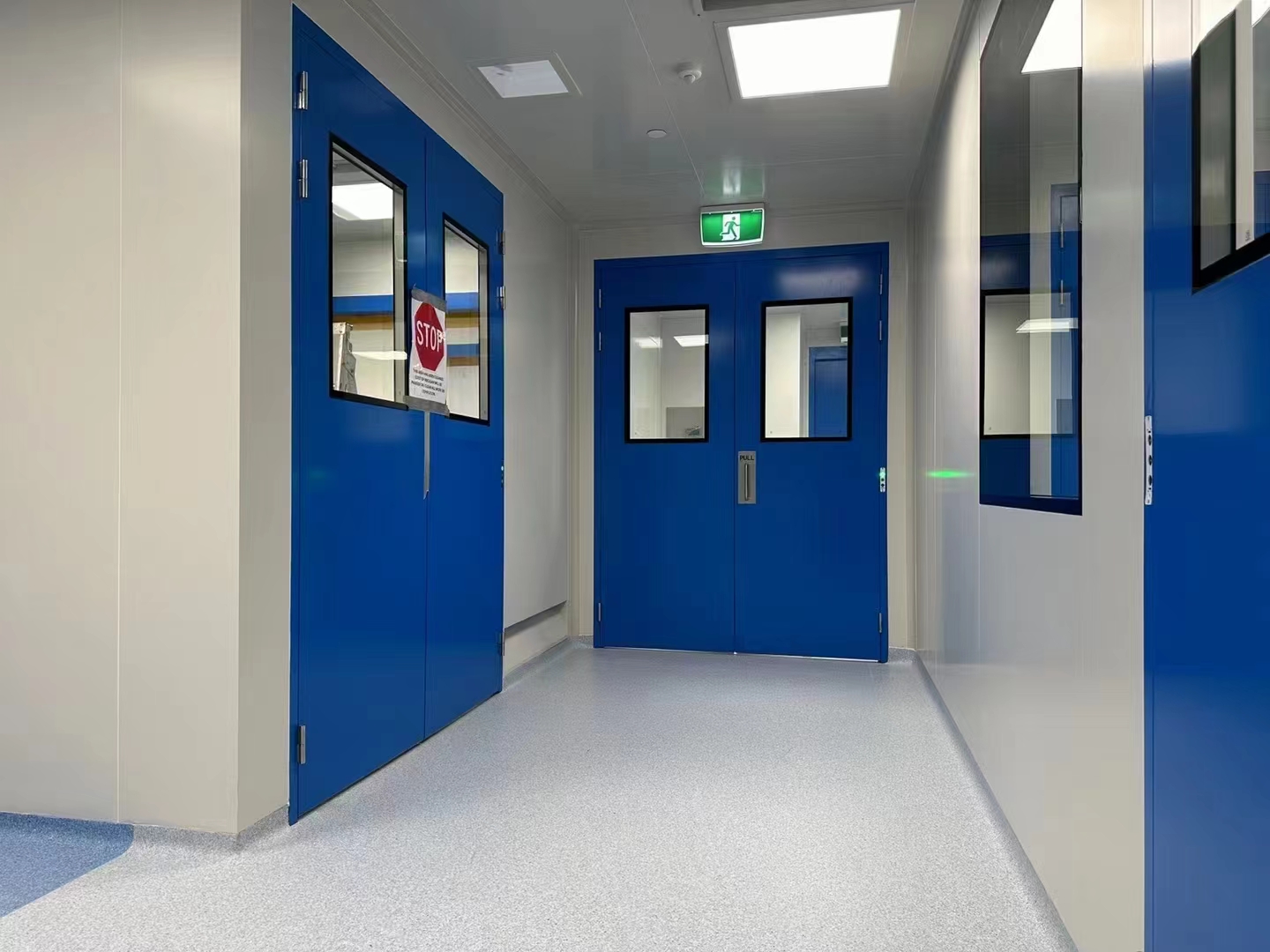
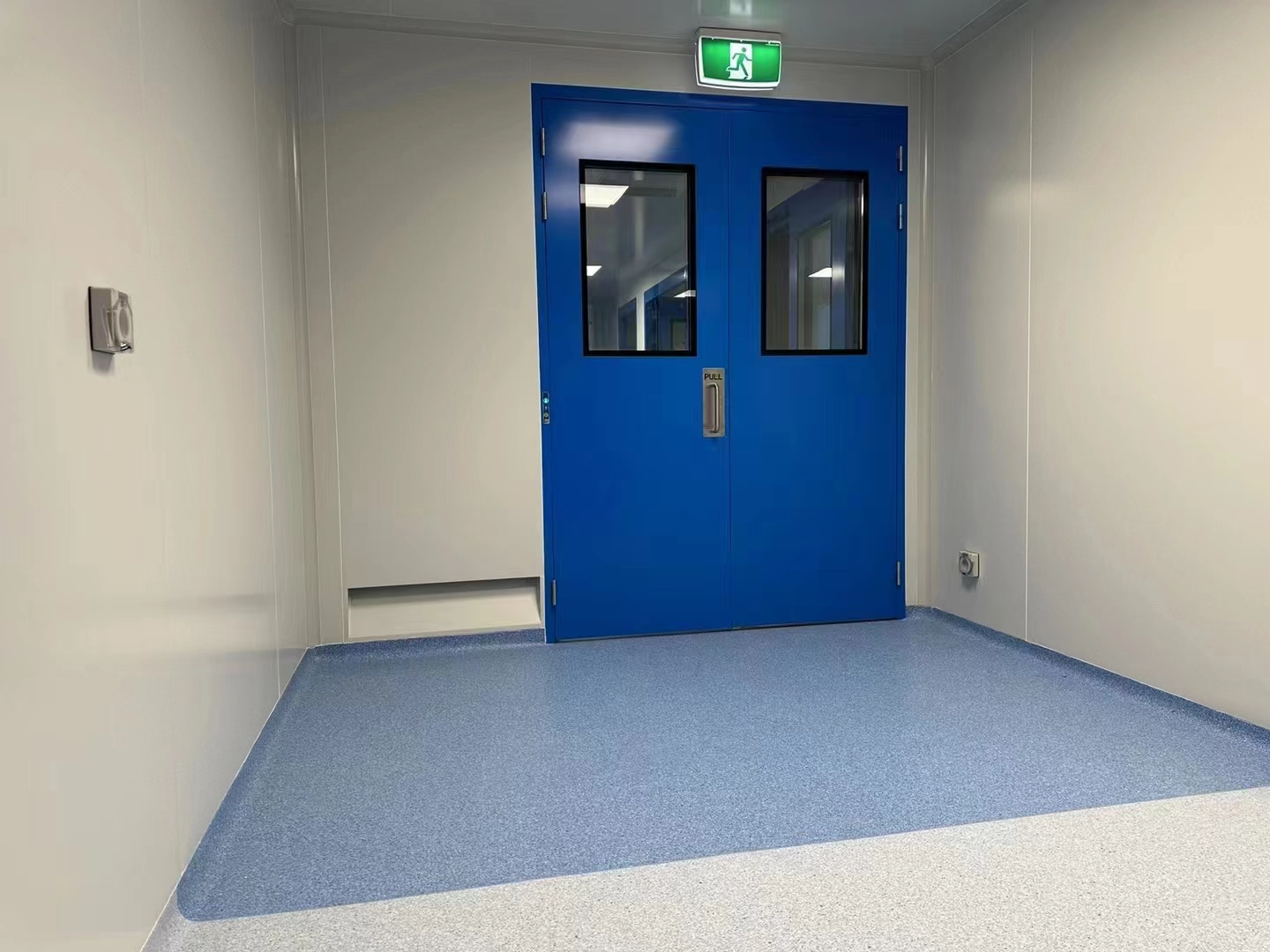
A clean room is a specially controlled environment in which factors such as the number of particles in air, humidity, temperature and static electricity can be controlled to achieve specific cleaning standards. Clean rooms are widely used in high-tech industries such as semiconductors, electronics, pharmaceuticals, aviation, aerospace and biomedicine.
In the pharmaceutical production management specifications, clean room is divided into 4 levels: A, B, C and D.
Class A: High-risk operating areas, such as filling areas, areas where rubber stopper barrels and open packaging containers are in direct contact with sterile preparations, and areas where aseptic assembly or connection operations are performed, should be equipped with unidirectional flow operating table to maintain the environmental status of the area. The unidirectional flow system must supply air evenly in its working area with air velocity of 0.36-0.54m/s. There should be data to prove the status of the unidirectional flow and be verified. In a closed, isolated operator or glove box, lower air velocity can be used.
Class B: refers to the background area where class A clean area is located for high-risk operations such as aseptic preparation and filling.
Class C and D: refer to clean areas with less important steps in the production of sterile pharmaceutical products.
According to GMP regulations, my country's pharmaceutical industry divides clean areas into 4 levels of ABCD as above based on indicators such as air cleanliness, air pressure, air volume, temperature and humidity, noise and microbial content.
The levels of clean areas are divided according to the concentration of suspended particles in air. Generally speaking, the smaller the value, the higher the cleanliness level.
1. Air cleanliness refers to the size and number of particles (including microorganisms) contained in air per unit volume of space, which is the standard for distinguishing the cleanliness level of a space.
Static refers to the state after clean room air conditioning system has been installed and fully functional, and clean room staff have evacuated the site and self-purified for 20 minutes.
Dynamic means that clean room is in normal working condition, the equipment is operating normally, and designated personnel are operating according to specifications.
2. The ABCD grading standard comes from the GMP promulgated by the World Health Organization (WHO), which is a common pharmaceutical production quality management specification in the pharmaceutical industry. It is currently used in most regions around the world, including the European Union and China.
Chinese old version of GMP followed the American grading standards (class 100, class 10,000, class 100,000) until the implementation of the new version of GMP standards in 2011. Chinese pharmaceutical industry has begun to use the WHO's classification standards and use ABCD to distinguish the levels of clean areas.
Other clean room classification standards
Clean room have different grading standards in different regions and industries. The GMP standards have been introduced previously, and here we mainly introduce the American standards and ISO standards.
(1). American Standard
The concept of grading clean room was first proposed by the United States. In 1963, the first federal standard for the military part of clean room was launched: FS-209. The familiar class 100, class 10000 and class 100000 standards are all derived from this standard. In 2001, the United States stopped using FS-209E standard and began to use ISO standard.
(2). ISO standards
ISO standards are proposed by International Organization for Standardization ISO and cover multiple industries, not just the pharmaceutical industry. There are nine levels from class1 to class 9. Among them, class 5 is equivalent to class B, class 7 is equivalent to class C, and class 8 is equivalent to class D.
(3). To confirm the level of Class A clean area, the sampling volume of each sampling point shall not be less than 1 cubic meter. The level of airborne particles in class A clean areas is ISO 5, with suspended particles ≥5.0μm as the limit standard. The level of airborne particles in class B clean area (static) is ISO 5, and includes suspended particles of two sizes in table. For class C clean areas (static and dynamic), the levels of airborne particles are ISO 7 and ISO 8 respectively. For class D clean areas (static) the level of airborne particles is ISO 8.
(4). When confirming the level, a portable dust particle counter with a shorter sampling tube should be used to prevent ≥5.0μm suspended particles from settling in the long sampling tube of the remote sampling system. In unidirectional flow systems, isokinetic sampling heads should be used.
(5) Dynamic testing can be carried out during routine operations and culture medium simulated filling processes to prove that dynamic cleanliness level is achieved, but the culture medium simulated filling test requires dynamic testing under the "worst condition".
Class A clean room
Class A clean room, also known as class 100 clean room or ultra-clean room, is one of the cleanest rooms with the highest cleanliness. It can control the number of particles per cubic foot in air to less than 35.5, that is to say, the number of particles greater than or equal to 0.5um in each cubic meter of air cannot exceed 3,520 (static and dynamic). Class A clean room have very strict requirements and require the use of hepa filters, differential pressure control, air circulation systems and constant temperature and humidity control systems to achieve their high cleanliness requirements. Class A clean rooms are mainly used in microelectronics processing, biopharmaceuticals, precision instrument manufacturing, aerospace and other fields.
Class B clean room
Class B clean rooms are also called class 1000 clean rooms. Their cleanliness level is relatively low, allowing the number of particles greater than or equal to 0.5um per cubic meter of air to reach 3520 (static) and 352000 (dynamic). Class B clean rooms usually use high-efficiency filters and exhaust systems to control the humidity, temperature and pressure difference of the indoor environment. Class B clean rooms are mainly used in biomedicine, pharmaceutical manufacturing, precision machinery and instrument manufacturing and other fields.
Class C clean room
Class C clean rooms are also called class 10,000 clean rooms. Their cleanliness level is relatively low, allowing the number of particles greater than or equal to 0.5um per cubic meter of air to reach 352,000 (static) and 352,0000 (dynamic). Class C clean rooms usually use hepa filters, positive pressure control, air circulation, temperature and humidity control and other technologies to achieve their specific cleanliness standards. Class C clean rooms are mainly used in pharmaceuticals, medical device manufacturing, precision machinery and electronic component manufacturing and other fields.
Class D clean room
Class D clean rooms are also called class 100,000 clean rooms. Their cleanliness level is relatively low, allowing the number of particles greater than or equal to 0.5um per cubic meter of air to reach 3,520,000 (static). Class D clean rooms usually use ordinary hepa filters and basic positive pressure control and air circulation systems to control indoor environment. Class D clean rooms are mainly used in general industrial production, food processing and packaging, printing, warehousing and other fields.
Different levels of clean rooms have their own scope of application, which should be selected according to actual needs. In practical applications, environmental control of clean rooms is a very important task, involving the comprehensive consideration of multiple factors. Only scientific and reasonable design and operation can ensure the quality and stability of the clean room environment.
Post time: Mar-07-2024