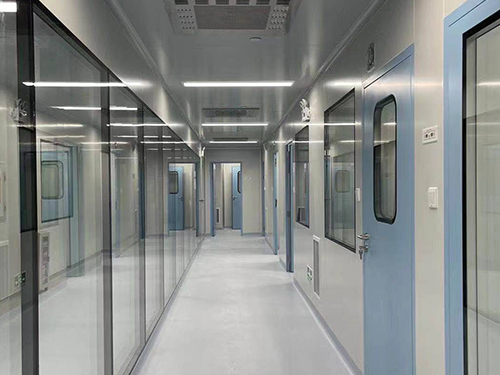
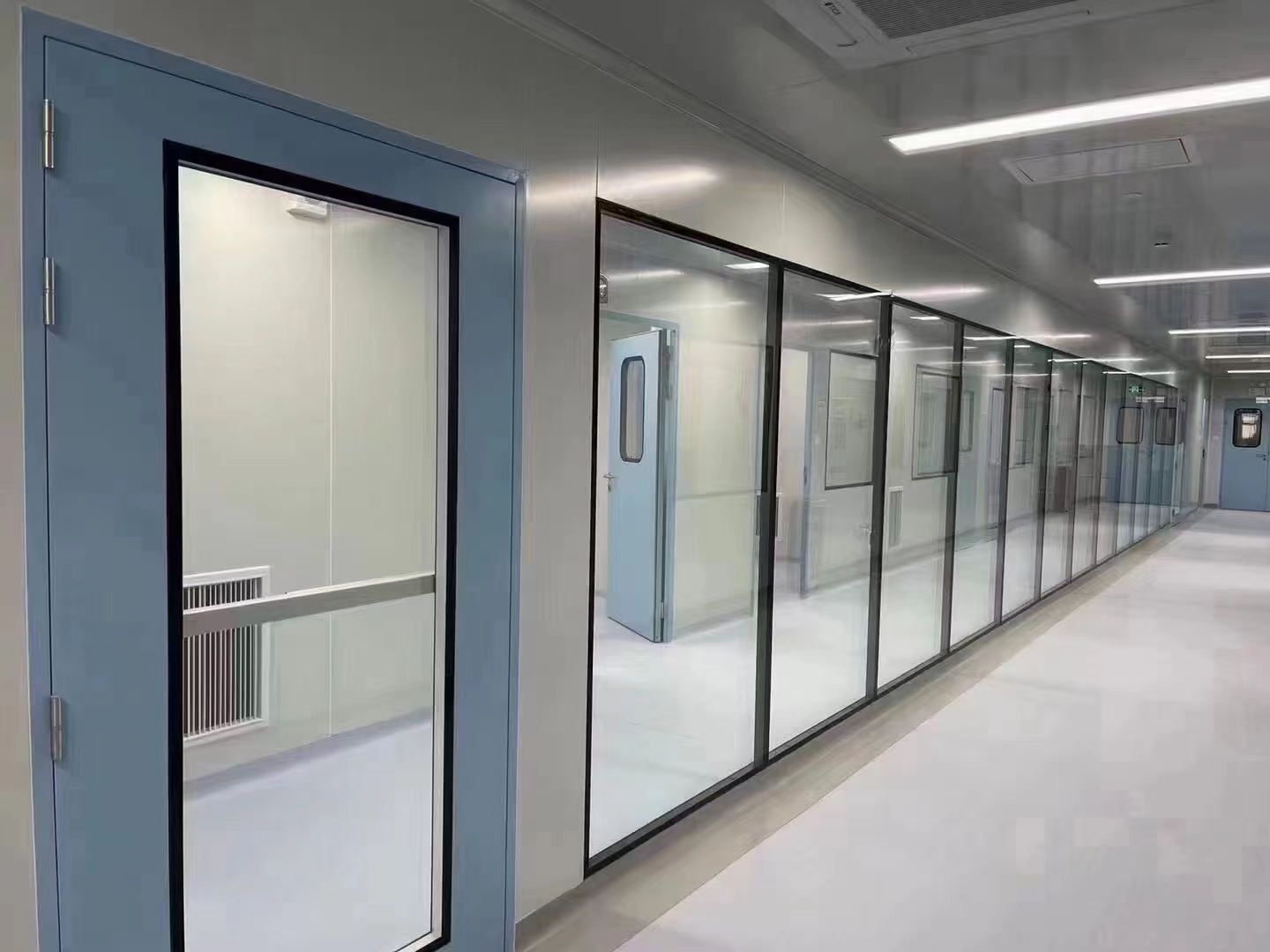
Clean rooms are also called dust free rooms. They are used to discharge pollutants such as dust particles, harmful air, and bacteria in the air within a certain space, and to control the indoor temperature, cleanliness, indoor pressure, airflow velocity and airflow distribution, noise vibration, lighting, and static electricity within a certain range. The following mainly describes the four necessary conditions for achieving cleanliness requirements in clean room purification measures.
1. Air supply cleanliness
To ensure that the air supply cleanliness meets the requirements, the key is the performance and installation of the final filter of the purification system. The final filter of the clean room system generally uses a hepa filter or a sub-hepa filter. According to national standards, the efficiency of hepa filters is divided into four grades: Class A is ≥99.9%, Class B is ≥99.99%, Class C is ≥99.999%, Class D is (for particles ≥0.1μm) ≥99.999% (also known as ultra-hepa filters); sub-hepa filters are (for particles ≥0.5μm) 95~99.9%.
2. Airflow organization
The airflow organization of a clean room is different from that of a general air-conditioned room. It requires that the cleanest air be delivered to the operating area first. Its function is to limit and reduce the contamination of the processed objects. Different airflow organizations have their own characteristics and scopes: Vertical unidirectional flow: Both can obtain uniform downward airflow, facilitate the layout of process equipment, have strong self-purification ability, and can simplify common facilities such as personal clean room facilities. The four air supply methods also have their own advantages and disadvantages: fully covered hepa filters have the advantages of low resistance and long filter replacement cycle, but the ceiling structure is complex and the cost is high; the advantages and disadvantages of side-covered hepa filter top delivery and full-hole plate top delivery are opposite to those of fully covered hepa filter top delivery. Among them, the full-hole plate top delivery is prone to dust accumulation on the inner surface of the orifice plate when the system is non-continuously running, and poor maintenance will have some impact on the cleanliness; dense diffuser top delivery requires a mixing layer, so it is only suitable for tall clean rooms over 4m, and its characteristics are similar to those of full-hole plate top delivery; the return air method for the plates with grilles on both sides and the return air outlets evenly arranged at the bottom of the walls on both sides is only suitable for clean rooms with a net spacing of less than 6m on both sides; the return air outlets at the bottom of the single-side wall are only suitable for clean rooms with a small spacing between walls (such as ≤2~3m). Horizontal unidirectional flow: only the first working area reaches the 100-level cleanliness. When the air flows to the other side, the dust concentration gradually increases. Therefore, it is only suitable for clean rooms with different cleanliness requirements for the same process. The local distribution of hepa filters on the air supply wall can reduce the use of hepa filters and save initial investment, but there are eddies in local areas. Turbulent airflow: The characteristics of top delivery of orifice plates and top delivery of dense diffusers are the same as those mentioned above. The advantages of side delivery are easy pipeline layout, no technical interlayer, low cost, and conducive to the renovation of old factories. The disadvantages are that the wind speed in the working area is large, and the dust concentration on the downwind side is higher than that on the upwind side. The top delivery of hepa filter outlets has the advantages of simple system, no pipelines behind the hepa filter, and clean airflow directly delivered to the working area, but the clean airflow diffuses slowly and the airflow in the working area is more uniform. However, when multiple air outlets are evenly arranged or hepa filter outlets with diffusers are used, the airflow in the working area can also be made more uniform. However, when the system is not running continuously, the diffuser is prone to dust accumulation.
3. Air supply volume or air velocity
Sufficient ventilation volume is to dilute and remove indoor polluted air. According to different cleanliness requirements, when the net height of the clean room is high, the ventilation frequency should be appropriately increased. Among them, the ventilation volume of the 1 million clean room is considered according to the high-efficiency clean room system, and the rest are considered according to the high-efficiency clean room system; when the hepa filters of the class 100,000 clean room are concentrated in the machine room or the sub-hepa filters are used at the end of the system, the ventilation frequency can be appropriately increased by 10% to 20%.
4. Static pressure difference
Maintaining a certain positive pressure in the clean room is one of the essential conditions to ensure that the clean room is not or less polluted to maintain the designed cleanliness level. Even for a negative pressure clean room, it must have an adjacent room or suite with a cleanliness level not lower than its level to maintain a certain positive pressure, so that the cleanliness of the negative pressure clean room can be maintained. The positive pressure value of the clean room refers to the value when the indoor static pressure is greater than the outdoor static pressure when all doors and windows are closed. It is achieved by the method that the air supply volume of the purification system is greater than the return air volume and exhaust air volume. In order to ensure the positive pressure value of the clean room, it is best to interlock the air supply, return air and exhaust fans. When the system is turned on, the supply fan is started first, and then the return fan and exhaust fan are started; when the system is turned off, the exhaust fan is turned off first, and then the return fan and supply fan are turned off to prevent the clean room from being contaminated when the system is turned on and off. The air volume required to maintain the positive pressure of the clean room is mainly determined by the tightness of the maintenance structure. In the early stage of the construction of clean rooms in China, due to the poor tightness of the enclosure structure, it took 2~6 times/h of air supply to maintain a positive pressure of ≥5Pa; at present, the tightness of the maintenance structure has been greatly improved, and it only takes 1~2 times/h of air supply to maintain the same positive pressure; it only takes 2~3 times/h of air supply to maintain ≥10Pa. National design specifications stipulate that the static pressure difference between clean rooms of different levels and between clean areas and non-clean areas should not be less than 0.5mmH2O (~5Pa), and the static pressure difference between the clean area and the outdoors should not be less than 1.0mmH2O (~10Pa).
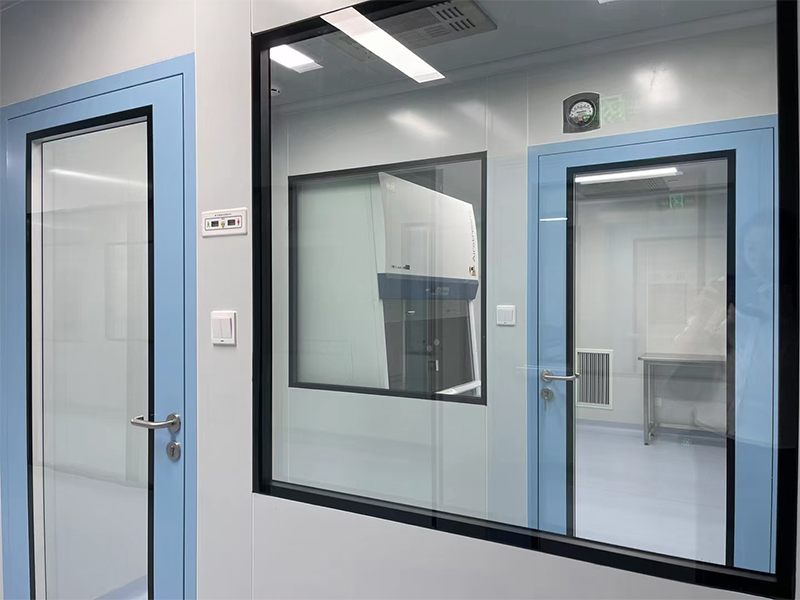
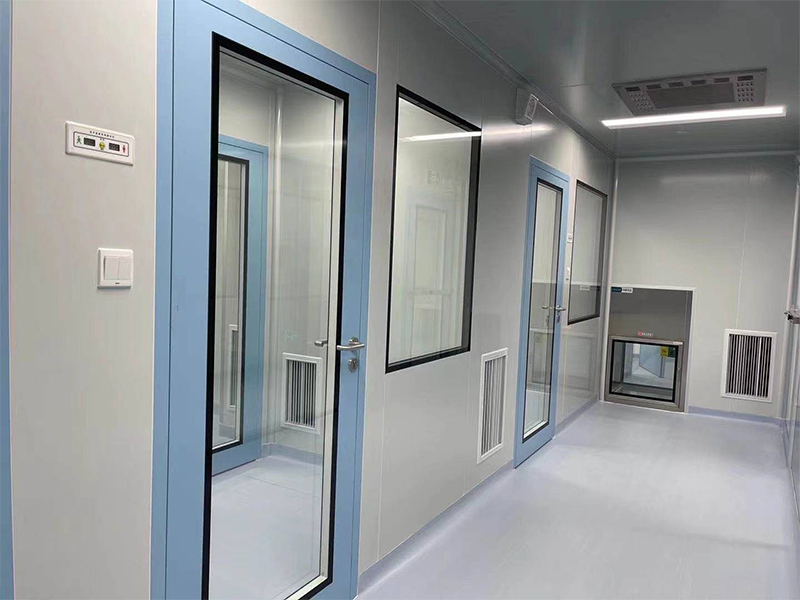
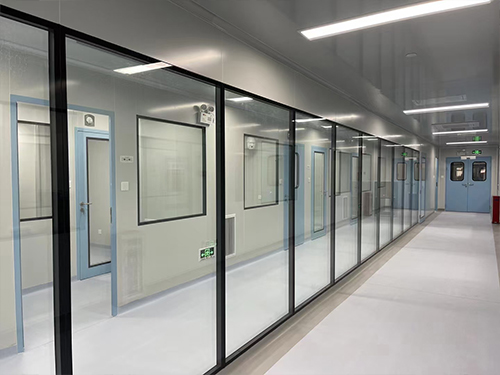
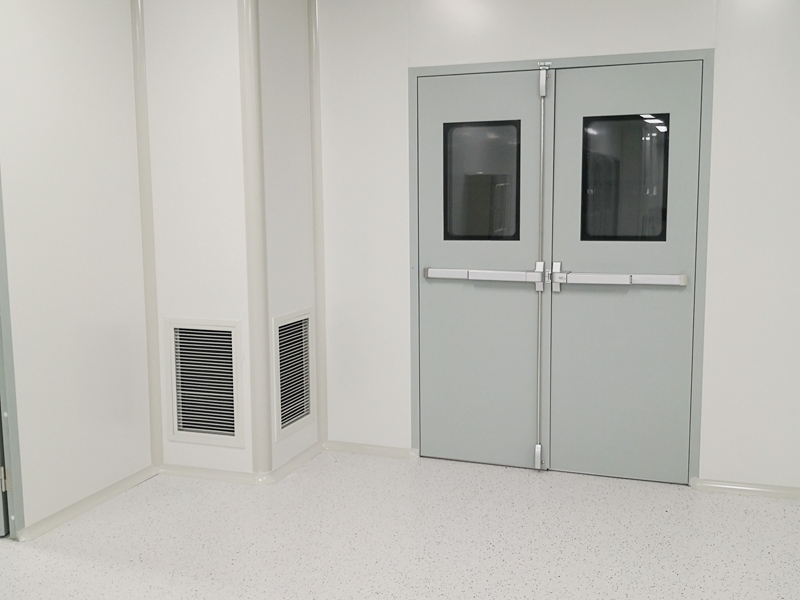
Post time: Mar-03-2025