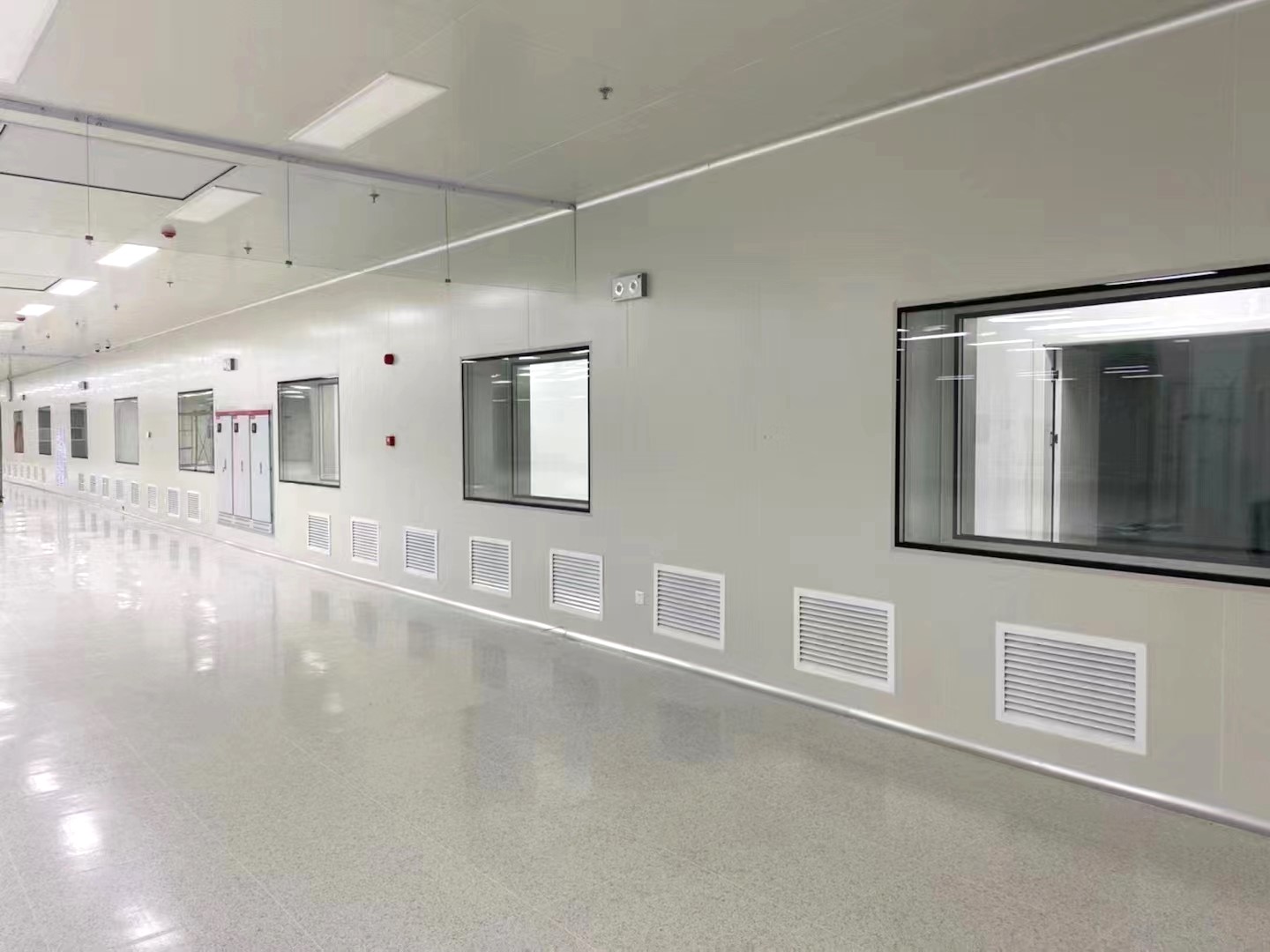
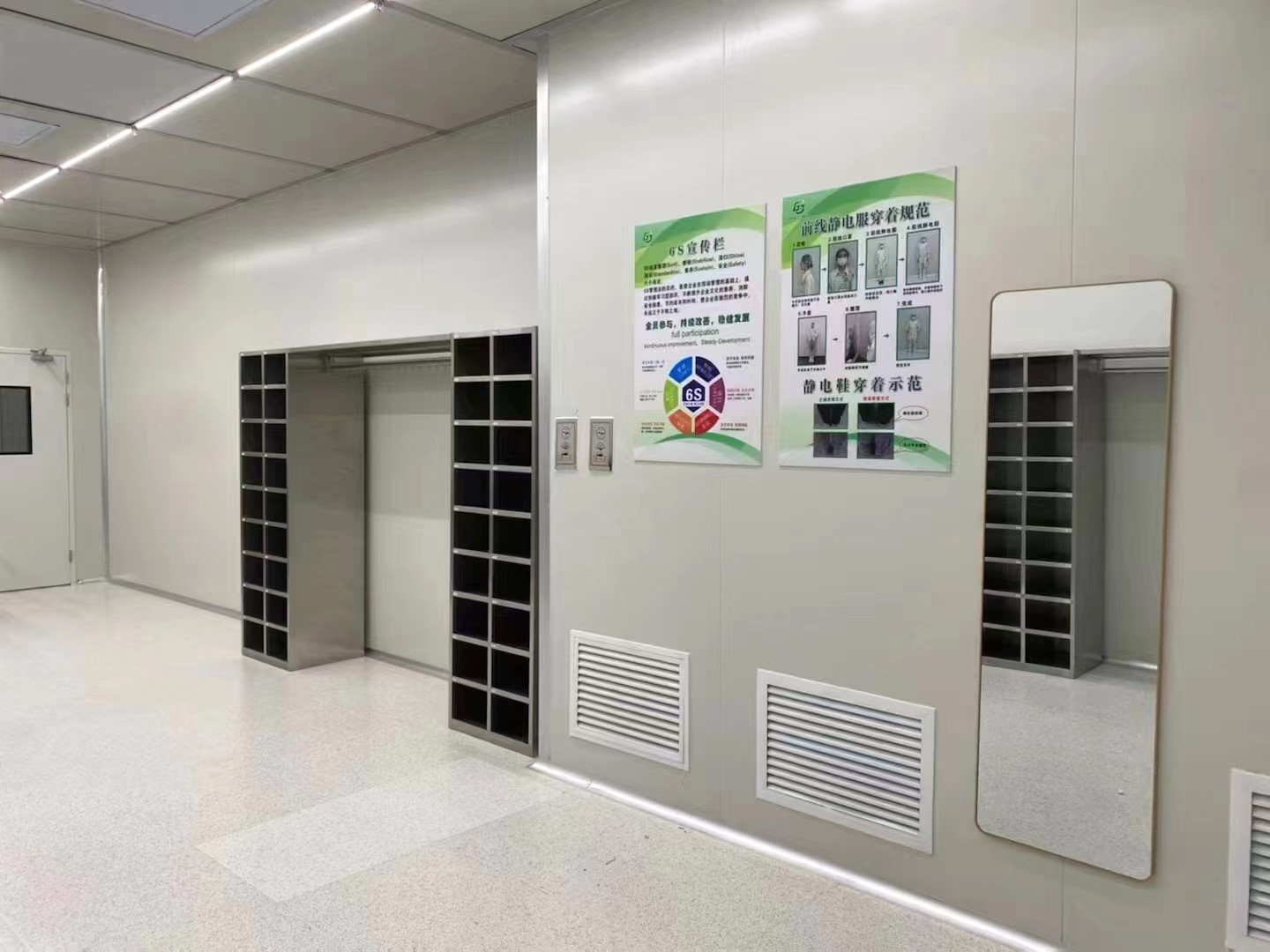
Electronic manufacturing industry:
With the development of computers, microelectronics and information technology, the electronic manufacturing industry has developed rapidly, and the clean room technology has also been driven. At the same time, higher requirements have been put forward for the design of clean room. The design of clean room in electronic manufacturing industry is a comprehensive technology. Only by fully understanding the design characteristics of clean room in electronic manufacturing industry and making reasonable designs can the defective rate of products in electronic manufacturing industry be reduced and production efficiency be improved.
Characteristics of clean room in electronic manufacturing industry:
The cleanliness level requirements are high, and the air volume, temperature, humidity, pressure difference, and equipment exhaust are controlled as needed. The illumination and air velocity of the clean room section are controlled according to the design or specification. In addition, this type of clean room has extremely strict requirements on static electricity. The requirements for humidity are particularly severe. Because static electricity is easily generated in an overly dry factory, it causes damage to CMOS integration. Generally speaking, the temperature of an electronic factory should be controlled at around 22°C, and the relative humidity should be controlled between 50-60% (there are relevant temperature and humidity regulations for special clean room). At this time, static electricity can be effectively eliminated and people can also feel comfortable. Chip production workshops, integrated circuit clean room and disk manufacturing workshops are important components of clean room in electronics manufacturing industry. Since electronic products have extremely strict requirements on indoor air environment and quality during manufacturing and production, they mainly focus on controlling particles and floating dust, and also have strict regulations on the temperature, humidity, fresh air volume, noise, etc. of the environment.
1. Noise level (empty state) in the class 10,000 clean room of an electronics manufacturing plant: should not be greater than 65dB (A).
2. The full coverage ratio of the vertical flow clean room in electronics manufacturing plant should not be less than 60%, and the horizontal unidirectional flow clean room should not be less than 40%, otherwise it will be a partial unidirectional flow.
3. The static pressure difference between the clean room and the outdoors of the electronics manufacturing plant should not be less than 10Pa, and the static pressure difference between the clean area and the non-clean area with different air cleanliness should not be less than 5Pa.
4. The amount of fresh air in class 10,000 clean room of the electronics manufacturing industry should take the maximum of the following two items:
① Compensate for the sum of the indoor exhaust volume and the amount of fresh air required to maintain the indoor positive pressure value.
② Ensure that the amount of fresh air supplied to the clean room per person per hour is not less than 40m3.
③ The heater of the clean room purification air conditioning system in the electronic manufacturing industry should be equipped with fresh air and over-temperature power-off protection. If point humidification is used, waterless protection should be set. In cold areas, the fresh air system should be equipped with anti-freeze protection measures. The air supply volume of the clean room should take the maximum value of the following three items: the air supply volume to ensure the air cleanliness level of the clean room of the electronic manufacturing plant; the air supply volume of the clean room of the electronic factory is determined according to the heat and humidity load calculation; the amount of fresh air supplied to the clean room of the electronic manufacturing plant.
Biomanufacturing industry:
Characteristics of biopharmaceutical factories:
1. Biopharmaceutical cleanroom not only have high equipment costs, complex production processes, high requirements for cleanliness levels and sterility, but also have strict requirements on the quality of production personnel.
2. Potential biological hazards will appear in the production process, mainly infection risks, dead bacteria or dead cells and components or metabolism to the human body and other organisms toxicity, sensitization and other biological reactions, product toxicity, sensitization and other biological reactions, environmental effects.
Clean area: A room (area) where dust particles and microbial contamination in the environment need to be controlled. Its building structure, equipment and its use have the function of preventing the introduction, generation and retention of pollutants in the area.
Airlock: An isolated space with two or more doors between two or more rooms (such as rooms with different cleanliness levels). The purpose of setting up an airlock is to control the airflow when people or materials enter and exit the airlock. Airlocks are divided into personnel airlocks and material airlocks.
The basic characteristics of the clean room of biopharmaceuticals: dust particles and microorganisms must be the objects of environmental control. The cleanliness of the pharmaceutical production workshop is divided into four levels: local class 100, class 1000, class 10000 and class 30000 under the background of class 100 or class 10000.
The temperature of the clean room: without special requirements, at 18~26 degrees, and the relative humidity is controlled at 45%~65%. Pollution control of biopharmaceutical clean workshops: pollution source control, diffusion process control, and cross-contamination control. The key technology of clean room medicine is mainly to control dust and microorganisms. As a pollutant, microorganisms are the top priority of clean room environmental control. The pollutants accumulated in the equipment and pipelines in the clean area of the pharmaceutical plant can directly contaminate the drugs, but it does not affect the cleanliness test. The cleanliness level is not suitable for characterizing the physical, chemical, radioactive and vital properties of suspended particles. Unfamiliar with the drug production process, the causes of pollution and the places where pollutants accumulate, and the methods and evaluation standards for removing pollutants.
The following situations are common in the GMP technology transformation of pharmaceutical plants:
Due to the misunderstanding of subjective cognition, the application of clean technology in the pollution control process is unfavorable, and finally some pharmaceutical plants have invested heavily in transformation, but the quality of drugs has not been significantly improved.
The design and construction of pharmaceutical clean production plants, the manufacture and installation of equipment and facilities in the plants, the quality of raw and auxiliary materials and packaging materials used in production, and the unfavorable implementation of the control procedures for clean people and clean facilities will affect product quality. The reasons that affect product quality in construction are that there are problems in the process control link, and there are hidden dangers during the installation and construction process, which are as follows:
① The inner wall of the air duct of the purification air conditioning system is not clean, the connection is not tight, and the air leakage rate is too large;
② The color steel plate enclosure structure is not tight, the sealing measures between the clean room and the technical mezzanine (ceiling) are improper, and the closed door is not airtight;
③ The decorative profiles and process pipelines form dead corners and dust accumulation in the clean room;
④ Some locations are not constructed according to the design requirements and cannot meet the relevant requirements and regulations;
⑤ The quality of the sealant used is not up to standard, easy to fall off, and deteriorate;
⑥ The return and exhaust color steel plate aisles are connected, and dust enters the return air duct from the exhaust;
⑦ The inner wall weld is not formed when welding stainless steel sanitary pipes such as process purified water and injection water;
⑧ The air duct check valve fails to work, and air backflow causes pollution;
⑨ The installation quality of the drainage system is not up to standard, and the pipe rack and accessories are easy to accumulate dust;
⑩ The pressure difference setting of the clean room is unqualified and fails to meet the production process requirements.
Printing and packaging industry:
With the development of society, the products of the printing industry and packaging industry have also improved. Large-scale printing equipment has entered the cleanroom, which can greatly improve the quality of printed products and significantly increase the qualified rate of products. This is also the best integration of the purification industry and the printing industry. Printing mainly reflects the temperature and humidity of the product in the coating space environment, the number of dust particles, and directly plays an important role in product quality and qualified rate. The packaging industry is mainly reflected in the temperature and humidity of the space environment, the number of dust particles in the air, and the quality of water in food packaging and pharmaceutical packaging. Of course, the standardized operating procedures of production personnel are also very important.
Dust-free spraying is an independent closed production workshop composed of steel sandwich panels, which can effectively filter the pollution of bad air environment to products and reduce dust in the spraying area and product defective rate. The application of dust-free technology further improves the appearance quality of products, such as TV/computer, mobile phone shell, DVD/VCD, game console, video recorder, PDA handheld computer, camera shell, audio, hair dryer, MD, makeup, toys and other workpieces. Process: loading area → manual dust removal → electrostatic dust removal → manual/automatic spraying → drying area → UV paint curing area → cooling area → screen printing area → quality inspection area → receiving area.
To prove that the food packaging dust-free workshop works satisfactorily, it must be proved that it meets the requirements of the following criteria:
① The air supply volume of the food packaging dust-free workshop is sufficient to dilute or eliminate the pollution generated indoors.
② The air in the food packaging dust-free workshop flows from the clean area to the area with poor cleanliness, the flow of contaminated air is minimized, and the air flow direction at the door and in the indoor building is correct.
③ The air supply of the food packaging dust-free workshop will not significantly increase the indoor pollution.
④ The movement state of the indoor air in the food packaging dust-free workshop can ensure that there is no high-concentration gathering area in the closed room. If the clean room meets the requirements of the above criteria, its particle concentration or microbial concentration (if necessary) can be measured to determine that it meets the specified clean room standards.
Food packaging industry:
1. Air supply and exhaust volume: If it is a turbulent clean room, then its air supply and exhaust volume must be measured. If it is a unidirectional clean room, its wind speed should be measured.
2. Airflow control between zones: To prove that the direction of airflow between zones is correct, that is, it flows from the clean area to the area with poor cleanliness, it is necessary to test:
① The pressure difference between each zone is correct;
② The direction of airflow at the door or openings on the wall, floor, etc. is correct, that is, it flows from the clean area to the area with poor cleanliness.
3. Filter leak detection: The high-efficiency filter and its outer frame should be inspected to ensure that suspended pollutants will not pass through:
① Damaged filter;
② The gap between the filter and its outer frame;
③ Other parts of the filter device and invade the room.
4. Isolation leak detection: This test is to prove that suspended pollutants do not penetrate the building materials and invade the clean room.
5. Indoor airflow control: The type of airflow control test depends on the airflow pattern of the clean room - whether it is turbulent or unidirectional. If the clean room airflow is turbulent, it must be verified that there is no area in the room where the airflow is insufficient. If it is a unidirectional clean room, it must be verified that the wind speed and wind direction of the entire room meet the design requirements.
6. Suspended particle concentration and microbial concentration: If the above tests meet the requirements, the particle concentration and microbial concentration (when necessary) are finally measured to verify that they meet the technical requirements of the clean room design.
7. Other tests: In addition to the above pollution control tests, one or more of the following tests must sometimes be performed: temperature; relative humidity; indoor heating and cooling capacity; noise value; illuminance; vibration value.
Pharmaceutical packaging industry:
1. Environmental control requirements:
① Provide the air purification level required for production. The number of air dust particles and live microorganisms in the packaging workshop purification project should be regularly tested and recorded. The static pressure difference between packaging workshops of different levels should be kept within the specified value.
② The temperature and relative humidity of the packaging workshop purification project should be consistent with its production process requirements.
③ The production area of penicillins, highly allergenic and anti-tumor drugs should be equipped with an independent air-conditioning system, and the exhaust gas should be purified.
④ For rooms that generate dust, effective dust collection devices should be installed to prevent cross-contamination of dust.
⑤ For auxiliary production rooms such as storage, the ventilation facilities and temperature and humidity should be consistent with the requirements of pharmaceutical production and packaging.
2. Cleanliness zoning and ventilation frequency: The clean room should strictly control the air cleanliness, as well as the parameters such as environmental temperature, humidity, fresh air volume and pressure difference.
① The purification level and ventilation frequency of the pharmaceutical production and packaging workshop The air cleanliness of the purification project of the pharmaceutical production and packaging workshop is divided into four levels: class 100, class 10,000, class 100,000 and class 300,000. To determine the ventilation frequency of the clean room, it is necessary to compare the air volume of each item and take the maximum value. In practice, the ventilation frequency of the class 100 is 300-400 times/h, class 10,000 is 25-35 times/h, and the class 100,000 is 15-20 times/h.
② Cleanliness zoning of the cleanroom project of the pharmaceutical packaging workshop. The specific zoning of the cleanliness of the pharmaceutical production and packaging environment is based on the national standard purification standard.
③ Determination of other environmental parameters of the cleanroom project of the packaging workshop.
④ Temperature and humidity of the cleanroom project of the packaging workshop. The temperature and relative humidity of the clean room should comply with the pharmaceutical production process. Temperature: 20~23℃ (summer) for class 100 and class 10,000 cleanliness, 24~26℃ for class 100,000 and class 300,000 cleanliness, 26~27℃ for general areas. Class 100 and 10,000 cleanliness are sterile rooms. Relative humidity: 45-50% (summer) for hygroscopic drugs, 50%~55% for solid preparations such as tablets, 55%~65% for water injections and oral liquids.
⑤ Clean room pressure to maintain indoor cleanliness, positive pressure must be maintained indoors. For clean rooms that produce dust, harmful substances, and produce penicillin-type highly allergenic drugs, external pollution must be prevented or relative negative pressure must be maintained between areas. Static pressure of rooms with different cleanliness levels. The indoor pressure must be maintained positive, with a difference of more than 5Pa from the adjacent room, and the static pressure difference between the clean room and the outdoor atmosphere must be greater than 10Pa.
Food industry:
Food is the first necessity of the people, and diseases come from the mouth, so the safety and sanitation of the food industry play an important role in our daily life. The safety and sanitation of food mainly need to be controlled in three aspects: first, the standardized operation of production personnel; second, the control of external environmental pollution (a relatively clean operating space should be established. Third, the source of procurement should be free of problematic product raw materials.
The area of the food production workshop is adapted to the production, with a reasonable layout and smooth drainage; the workshop floor is built with non-slip, strong, impermeable and corrosion-resistant materials, and is flat, free of water accumulation, and kept clean; the workshop exit and the drainage and ventilation areas connected to the outside world are equipped with anti-rat, anti-fly and anti-insect facilities. The walls, ceilings, doors and windows in the workshop should be constructed with non-toxic, light-colored, waterproof, mildew-proof, non-shedding and easy-to-clean materials. The corners of the walls, the ground corners and the top corners should have an arc (the radius of curvature should not be less than 3cm). The operating tables, conveyor belts, transport vehicles and tools in the workshop should be made of non-toxic, corrosion-resistant, rust-free, easy-to-clean and disinfect, and solid materials. A sufficient number of hand-washing, disinfection and hand-drying equipment or supplies should be set up in appropriate locations, and the faucets should be non-manual switches. According to the needs of product processing, there should be disinfection facilities for shoes, boots and wheels at the entrance of the workshop. There should be a dressing room connected to the workshop. According to the needs of product processing, toilets and shower rooms connected to the workshop should also be set up.
Optoelectronics:
The cleanroom for optoelectronic products is generally suitable for electronic instruments, computers, semiconductor factories, automobile industry, aerospace industry, photolithography, microcomputer manufacturing and other industries. In addition to air cleanliness, it is also necessary to ensure that the requirements of static electricity removal are met. The following is an introduction to the dust-free purification workshop in the optoelectronics industry, taking the modern LED industry as an example.
LED cleanroom workshop project installation and construction case analysis: In this design, it refers to the installation of some purification dust-free workshops for terminal processes, and its purification cleanliness is generally class 1,000, class 10,000 or class 100,000 cleanroom workshops. The installation of backlight screen cleanroom workshops is mainly for stamping workshops, assembly and other cleanroom workshops for such products, and its cleanliness is generally class 10,000 or class 100,000 cleanroom workshops. Indoor air parameter requirements for LED cleanroom workshop installation:
1. Temperature and humidity requirements: The temperature is generally 24±2℃, and the relative humidity is 55±5%.
2. Fresh air volume: Since there are many people in this type of clean dust-free workshop, the following maximum values should be taken according to the following values: 10-30% of the total air supply volume of the non-unidirectional cleanroom workshop; the amount of fresh air required to compensate for indoor exhaust and maintain the indoor positive pressure value; ensure that the indoor fresh air volume per person per hour is ≥40m3/h.
3. Large air supply volume. In order to meet the cleanliness and heat and humidity balance in cleanroom workshop, a large air supply volume is required. For a workshop of 300 square meters with a ceiling height of 2.5 meters, if it is a class 10,000 cleanroom workshop, the air supply volume needs to be 300*2.5*30=22500m3/h (air change frequency is ≥25 times/h); if it is a class 100,000 cleanroom workshop, the air supply volume needs to be 300*2.5*20=15000m3/h (air change frequency is ≥15 times/h).
Medical and health:
Clean technology is also called clean room technology. In addition to meeting the conventional requirements of temperature and humidity in air-conditioned rooms, various engineering and technical facilities and strict management are used to control the indoor particle content, airflow, pressure, etc. within a certain range. This kind of room is called a clean room. A clean room is built and used in a hospital. With the development of medical and health care and high technology, clean technology is more widely used in medical environments, and the technical requirements for itself are also higher. Clean rooms used in medical treatment are mainly divided into three categories: clean operating rooms, clean nursing wards and clean laboratories.
Modular operation room:
Modular operation room take indoor microorganisms as the control target, operating parameters and classification indicators, and air cleanliness is a necessary guarantee condition. Modular operation room can be divided into the following levels according to the degree of cleanliness:
1. Special modular operation room: The cleanliness of the operating area is class 100, and the surrounding area is class 1,000. It is suitable for aseptic operations such as burns, joint conversion, organ transplantation, brain surgery, ophthalmology, plastic surgery and cardiac surgery.
2. Modular operation room: The cleanliness of the operation area is class 1000, and the surrounding area is class 10,000. It is suitable for aseptic operations such as thoracic surgery, plastic surgery, urology, hepatobiliary and pancreatic surgery, orthopedic surgery and egg retrieval.
3. General modular operation room: The cleanliness of the operating area is class 10,000, and the surrounding area is class 100,000. It is suitable for general surgery, dermatology and abdominal surgery.
4. Quasi-clean modular operation room: The air cleanliness is class 100,000, suitable for obstetrics, anorectal surgery and other operations. In addition to the cleanliness level and bacterial concentration of the clean operating room, the relevant technical parameters should also comply with relevant regulations. See the main technical parameters table of rooms at all levels in the clean operating department. The plane layout of the modular operation room should be divided into two parts: clean area and non-clean area according to general requirements. The operation room and the functional rooms that directly serve the operation room should be located in clean area. When people and objects pass through different cleanliness areas in modular operation room, airlocks, buffer rooms or pass box should be installed. The operation room is generally located in the core part. The internal plane and channel form should comply with the principles of functional flow and clear separation of clean and dirty.
Several types of clean nursing wards in hospital:
Clean nursing wards are divided into isolation wards and intensive care units. Isolation wards are divided into four levels according to biological risk: P1, P2, P3, and P4. P1 wards are basically the same as ordinary wards, and there is no special prohibition on outsiders entering and exiting; P2 wards are stricter than P1 wards, and outsiders are generally prohibited from entering and exiting; P3 wards are isolated from the outside by heavy doors or buffer rooms, and the internal pressure of the room is negative; P4 wards are separated from the outside by isolation areas, and the indoor negative pressure is constant at 30Pa. Medical staff wear protective clothing to prevent infection. Intensive care units include ICU (intensive care unit), CCU (cardiovascular patient care unit), NICU (premature infant care unit), leukemia room, etc. The room temperature of the leukemia room is 242, the wind speed is 0.15-0.3/m/s, the relative humidity is below 60%, and the cleanliness is class 100. At the same time, the cleanest air delivered should reach the patient's head first, so that the mouth and nose breathing area is on the air supply side, and horizontal flow is better. The bacterial concentration measurement in the burn ward shows that the use of vertical laminar flow has obvious advantages over open treatment, with a laminar injection speed of 0.2m/s, a temperature of 28-34, and a cleanliness level of class 1000. Respiratory organ wards are rare in China. This type of ward has strict requirements on indoor temperature and humidity. The temperature is controlled at 23-30℃, the relative humidity is 40-60%, and each ward can be adjusted according to the patient's own needs. The cleanliness level is controlled between class 10 and class 10000, and the noise is less than 45dB (A). Personnel entering the ward should undergo personal purification such as changing clothes and showering, and the ward should maintain positive pressure.
Laboratory:
Laboratories are divided into ordinary laboratories and biosafety laboratories. The experiments conducted in ordinary clean laboratories are not infectious, but the environment is required to have no adverse effects on the experiment itself. Therefore, there are no protective facilities in laboratory, and the cleanliness must meet the experimental requirements.
A biosafety laboratory is a biological experiment with primary protection facilities that can achieve secondary protection. All scientific experiments in the fields of microbiology, biomedicine, functional experiments, and gene recombination require biosafety laboratories. The core of biosafety laboratories is safety, which are divided into four levels: P1, P2, P3, and P4 according to the degree of biological hazard.
P1 laboratories are suitable for very familiar pathogens, which do not often cause diseases in healthy adults and pose little danger to experimental personnel and the environment. The door should be closed during the experiment and the operation should be carried out according to ordinary microbiological experiments; P2 laboratories are suitable for pathogens that are moderately potentially dangerous to humans and the environment. Access to the experimental area is restricted. Experiments that may cause aerosols should be carried out in Class II biosafety cabinets, and autoclaves should be available; P3 laboratories are used in clinical, diagnostic, teaching, or production facilities. Work related to endogenous and exogenous pathogens is carried out at this level. Exposure and inhalation of the pathogens will cause serious and potentially fatal diseases. The laboratory is equipped with double doors or airlocks and an external isolated experimental area. Non-staff members are prohibited from entering. The laboratory is fully negatively pressurized. Class II biosafety cabinets are used for experiments. Hepa filters are used to filter indoor air and exhaust it outdoors. P4 laboratories have stricter requirements than P3 laboratories. Some dangerous exogenous pathogens have a high individual risk of laboratory infection and life-threatening diseases caused by aerosol transmission. Relevant work should be carried out in P4 laboratories. The structure of an independent isolation area in a building and an external partition is adopted. Negative pressure is maintained indoors. Class III biosafety cabinets are used for experiments. Air partition devices and shower rooms are set up. Operators should wear protective clothing. Non-staff members are prohibited from entering. The core of the design of biosafety laboratories is dynamic isolation, and exhaust measures are the focus. On-site disinfection is emphasized, and attention is paid to the separation of clean and dirty water to prevent accidental spread. Moderate cleanliness is required.
Post time: Jul-26-2024