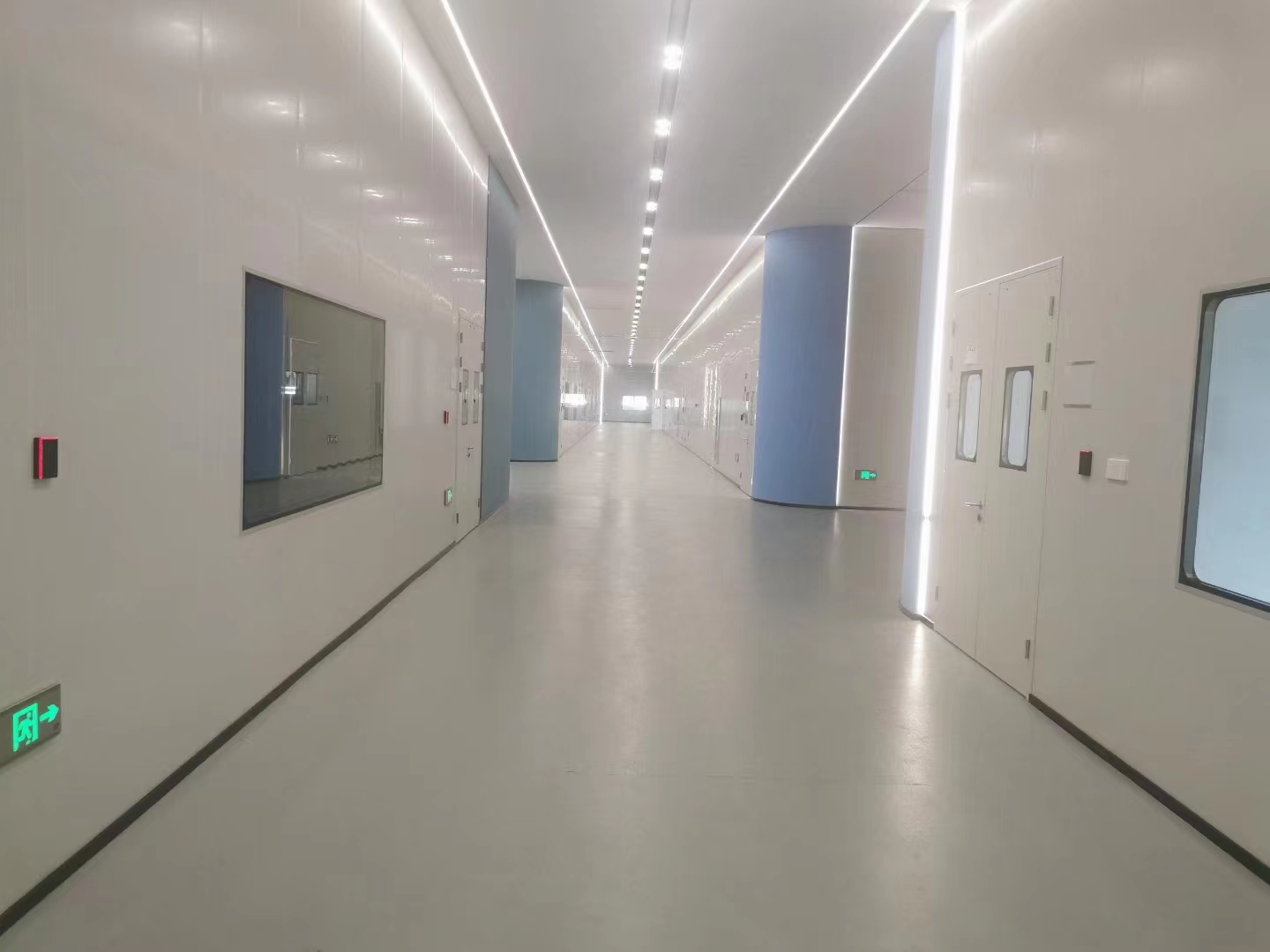

1. Analysis of the characteristics of tall clean rooms
(1). Tall clean rooms have their inherent characteristics. In general, tall clean room is mainly used in the post-production process, and are generally used for the assembly of large equipment. They do not require high cleanliness, and the control accuracy of temperature and humidity is not high. The equipment does not generate much heat during the process production, and there are relatively few people.
(2). Tall clean rooms usually have large frame structures, and often use light materials. The top plate is generally not easy to bear a large load.
(3). The generation and distribution of dust particles For tall clean rooms, the main pollution source is different from that of general clean rooms. In addition to dust generated by people and sports equipment, surface dust accounts for a large proportion. According to the data provided by the literature, the dust generation when a person is stationary is 105 particles/(min·person), and the dust generation when a person is moving is calculated as 5 times that when the person is stationary. For clean rooms of ordinary height, the surface dust generation is calculated as the surface dust generation of 8m2 of the ground is equivalent to the dust generation of a person at rest. For tall clean rooms, the purification load is larger in the lower personnel activity area and smaller in the upper area. At the same time, due to the characteristics of the project, it is necessary to take an appropriate safety factor for safety and considering unforeseen dust pollution. The surface dust generation of this project is based on the surface dust generation of 6m2 of the ground, which is equivalent to the dust generation of a person at rest. This project is calculated based on 20 people working per shift, and the dust generation of personnel only accounts for 20% of the total dust generation, while the dust generation of personnel in a general clean room accounts for about 90% of the total dust generation.
2. Clean room decoration of tall workshops
Clean room decoration generally includes clean room floors, wall panels, ceilings, and supporting air conditioning, lighting, fire protection, water supply and drainage and other contents related to clean rooms. According to the requirements, the building envelope and interior decoration of the clean room should use materials with good air tightness and small deformation when the temperature and humidity change. The decoration of walls and ceilings in clean rooms should meet the following requirements:
(1). The surfaces of walls and ceilings in clean rooms should be flat, smooth, dust-free, glare-free, easy to remove dust, and have fewer uneven surfaces.
(2). Clean rooms should not use masonry walls and plastered walls. When it is necessary to use them, dry work should be done and high-grade plastering standards should be used. After plastering the walls, the paint surface should be painted, and paint that is flame-retardant, crack-free, washable, smooth, and not easy to absorb water, deteriorate, and mold should be selected. In general, clean room decoration mainly chooses better powder-coated metal wall panels as interior decoration materials. However, for large space factories, due to the high floor height, the installation of metal wall panel partitions is more difficult, with poor strength, high cost, and inability to bear weight. This project analyzed the dust generation characteristics of clean rooms in large factories and the requirements for room cleanliness. Conventional metal wall panel interior decoration methods were not adopted. Epoxy coating was applied on the original civil engineering walls. No ceiling was set in the entire space to increase the usable space.
3. Airflow organization of tall clean rooms
According to the literature, for tall clean rooms, the use of clean room air conditioning system can greatly reduce the total air supply volume of the system. With the reduction of air volume, it is particularly important to adopt reasonable airflow organization to obtain better clean air conditioning effect. It is necessary to ensure the uniformity of the air supply and return air system, reduce the vortex and airflow swirl in the clean working area, and enhance the diffusion characteristics of the air supply airflow to give full play to the dilution effect of the air supply airflow. In tall clean workshops with class 10,000 or 100,000 cleanliness requirements, the design concept of tall and large spaces for comfort air conditioning can be cited, such as the use of nozzles in large spaces such as airports and exhibition halls. Using nozzles and side air supply, the airflow can be diffused over a long distance. Nozzle air supply is a way to achieve air supply by relying on high-speed jets blown out of the nozzles. It is mainly used in air conditioning places in tall clean rooms or public building spaces with high floor heights. The nozzle adopts side air supply, and the nozzle and the return air outlet are arranged on the same side. The air is concentratedly ejected from several nozzles set in the space at a higher speed and a larger air volume. The jet flows back after a certain distance, so that the entire air-conditioned area is in the reflow area, and then the return air outlet set at the bottom extracts it back to the air-conditioning unit. Its characteristics are high air supply speed and long range. The jet drives the indoor air to mix strongly, the speed gradually decays, and a large swirling airflow is formed indoors, so that the air-conditioned area obtains a more uniform temperature field and velocity field.
4. Engineering design example
A tall clean workshop (40 m long, 30 m wide, 12 m high) requires a clean working area below 5 m, with a purification level of static 10,000 and dynamic 100,000, temperature tn= 22℃±3℃, and relative humidity fn= 30%~60%.
(1). Determination of airflow organization and ventilation frequency
In view of the use characteristics of this tall clean room, which is more than 30m wide and has no ceiling, the conventional clean workshop air supply method is difficult to meet the use requirements. The nozzle layered air supply method is adopted to ensure the temperature, humidity and cleanliness of the clean working area (below 5 m). The nozzle air supply device for blowing is evenly arranged on the side wall, and the return air outlet device with a damping layer is evenly arranged at a height of 0.25 m from the ground at the lower part of the side wall of the workshop, forming an airflow organization form in which the work area returns from the nozzle and returns from the concentrated side. At the same time, in order to prevent the air in the non-clean working area above 5 m from forming a dead zone in terms of cleanliness, temperature and humidity, reduce the impact of cold and heat radiation from the ceiling outdoor on the working area, and timely discharge the dust particles generated by the upper crane during operation, and make full use of the clean air diffused to more than 5 m, a row of small strip return air outlets are arranged in the non-clean air-conditioning area, forming a small circulating return air system, which can greatly reduce the pollution of the upper non-clean area to the lower clean working area.
According to the cleanliness level and pollutant emission, this project adopts a ventilation frequency of 16 h-1 for the clean air-conditioned area below 6 m, and adopts appropriate exhaust for the upper non-clean area, with a ventilation frequency of less than 4 h-1. In fact, the average ventilation frequency of the entire plant is 10 h-1. In this way, compared with the clean air conditioning of the whole room, the clean layered nozzle air supply method not only better guarantees the ventilation frequency of the clean air-conditioned area and meets the air flow organization of the large-span plant, but also greatly saves the system's air volume, cooling capacity and fan power.
(2). Calculation of side nozzle air supply
Supply air temperature difference
The ventilation frequency required for clean room air conditioning is much greater than that of general air conditioning. Therefore, making full use of the large air volume of clean room air conditioning and reducing the supply air temperature difference of the supply air flow can not only save equipment capacity and operating costs, but also make it more conducive to ensuring the air conditioning accuracy of the clean room air-conditioned area. The supply air temperature difference calculated in this project is ts= 6℃.
The clean room has a relatively large span, with a width of 30 m. It is necessary to ensure the overlap requirements in the middle area and ensure that the process work area is in return air area. At the same time, the noise requirements must be considered. The air supply speed of this project is 5 m/s, the nozzle installation height is 6 m, and the air flow is sent out from the nozzle in the horizontal direction. This project calculated the nozzle air supply airflow. The nozzle diameter is 0.36m. According to the literature, the Archimedes number is calculated to be 0.0035. The nozzle air supply speed is 4.8m/s, the axial speed at the end is 0.8m/s, the average speed is 0.4m/s, and the average speed of the return flow is less than 0.4m/s, which meets the process use requirements.
Since the air volume of the supply air flow is large and the supply air temperature difference is small, it is almost the same as the isothermal jet, so the jet length is easy to guarantee. According to the Archimedean number, the relative range x/ds = 37m can be calculated, which can meet the requirement of 15m overlap of the opposite side supply air flow.
(3). Air conditioning condition treatment
In view of the characteristics of large supply air volume and small supply air temperature difference in clean room design, full use is made of return air, and the primary return air is eliminated in the summer air conditioning treatment method. The maximum proportion of secondary return air is adopted, and the fresh air is only treated once and then mixed with a large amount of secondary return air, thereby eliminating reheating and reducing the capacity and operating energy consumption of the equipment.
(4). Engineering measurement results
After the completion of this project, a comprehensive engineering test was carried out. A total of 20 horizontal and vertical measurement points were set up in the entire plant. The velocity field, temperature field, cleanliness, noise, etc. of the clean plant were tested under static conditions, and the actual measurement results were relatively good. The measured results under the design working conditions are as follows:
The average velocity of the airflow at the air outlet is 3.0~4.3m/s, and the velocity at the joint of the two opposite airflows is 0.3~0.45m/s. The ventilation frequency of the clean working area is guaranteed to be 15 times/h, and its cleanliness is measured to be within class 10,000, which meets the design requirements well.
The indoor A-level noise is 56 dB at the return air outlet, and other working areas are all below 54dB.
5. Conclusion
(1). For tall clean rooms with not very high requirements, simplified decoration can be adopted to achieve both the use requirements and the cleanliness requirements.
(2). For tall clean rooms that only require the cleanliness level of the area below a certain height to be class 10,000 or 100,000, the air supply method of clean layered air conditioning nozzles is a relatively economical, practical and effective method.
(3). For this type of tall clean rooms, a row of strip return air outlets is set in the upper non-clean work area to remove dust generated near the crane rails and reduce the impact of cold and heat radiation from the ceiling on the work area, which can better ensure the cleanliness and temperature and humidity of the work area.
(4). The height of a tall clean room is more than 4 times that of a general clean room. Under normal dust production conditions, it should be said that the unit space purification load is much lower than that of a general low clean room. Therefore, from this perspective, the ventilation frequency can be determined to be lower than the ventilation frequency of the clean room recommended by the national standard GB 73-84. Research and analysis show that for tall clean rooms, the ventilation frequency varies due to the different heights of the clean area. Generally, 30%~80% of the ventilation frequency recommended by the national standard can meet the purification requirements.
Post time: Feb-18-2025