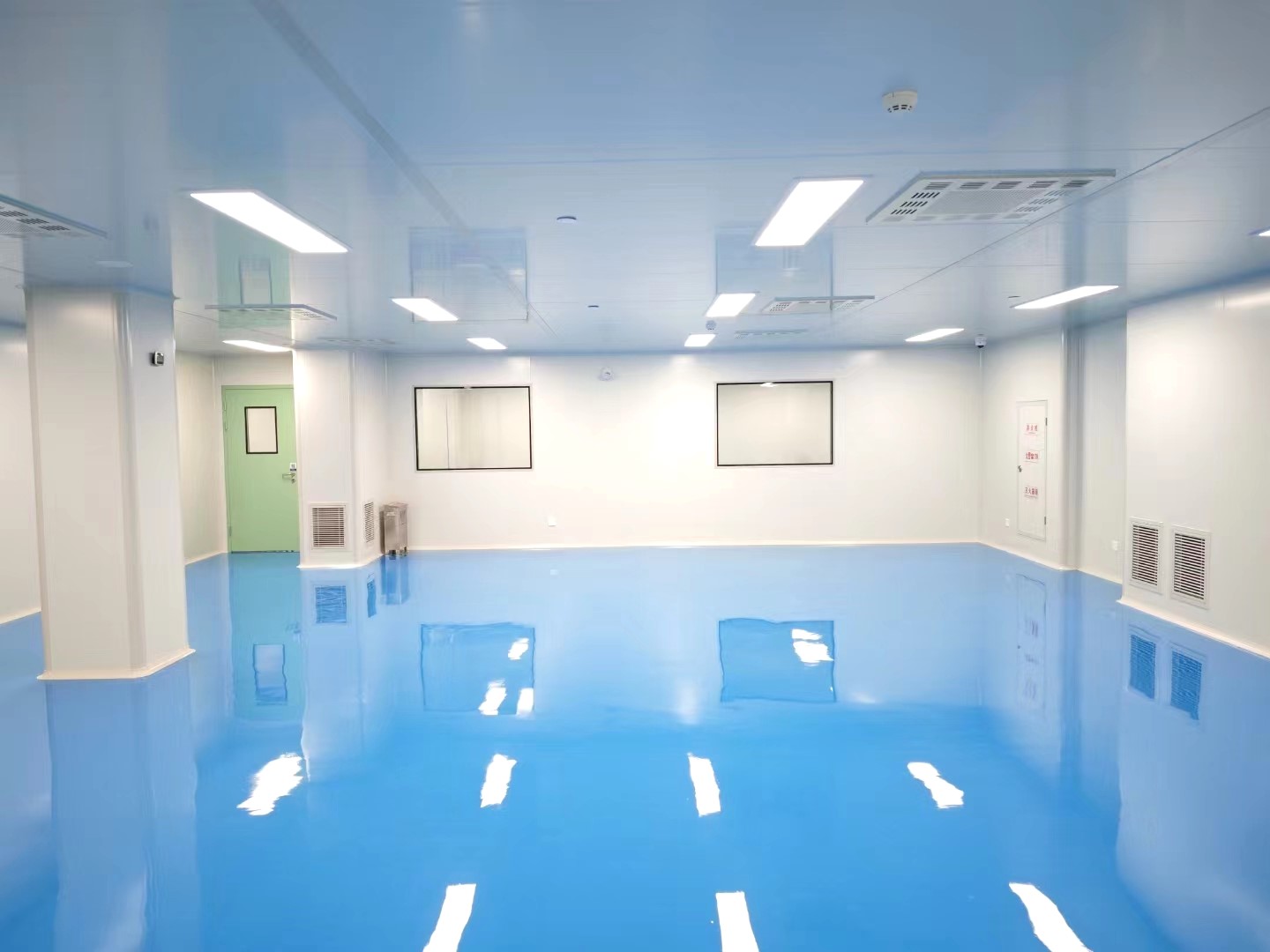
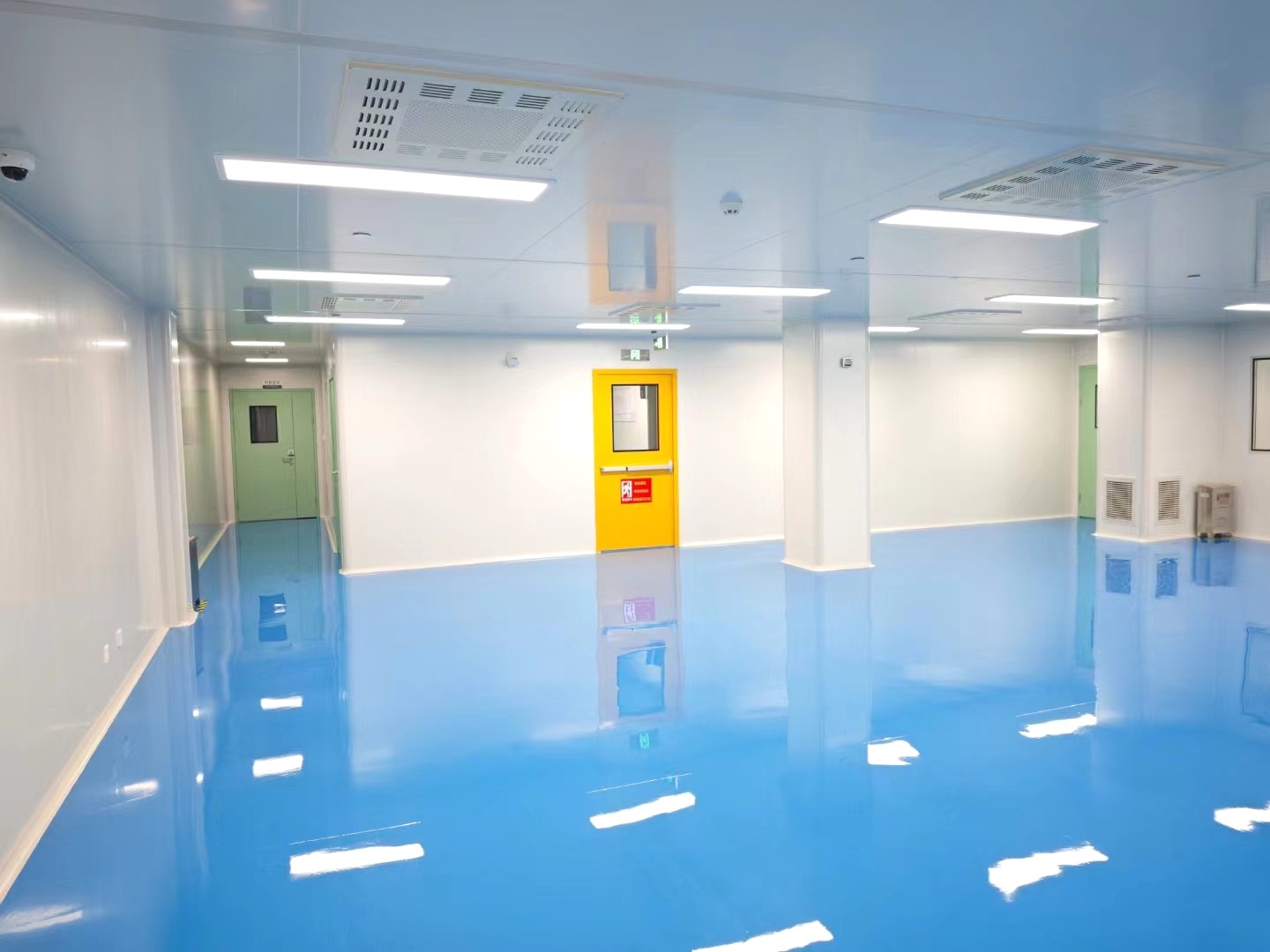
ISO 8 cleanroom refers to the use of a series of technologies and control measures to make the workshop space with a cleanliness level of class 100,000 for the production of products that require a high clean environment. This article will introduce in detail the relevant knowledge of ISO 8 cleanroom.
The concept of ISO 8 cleanroom
A dust-free cleanroom refers to a workshop that designs and controls the cleanliness, temperature, humidity, airflow, etc. of the workshop environment to meet specific requirements to ensure the cleanliness and quality of production equipment, personnel and manufactured products. ISO 8 clean room means that the number of dust particles in every cubic meter of air is less than 100,000, which meets the standard of air cleanliness level of class 100,000.
Key design elements of the ISO 8 cleanroom
1. Ground treatment
Select anti-static, anti-slip, wear-resistant and easy-to-clean floor materials.
2. Door and window design
Good airtightness, select door and window materials with good airtightness and little impact on the cleanliness of the workshop.
3. Air purification treatment system
The air treatment system is the most important link. The system should include primary filters, medium filters and hepa filters to ensure that all air used in the manufacturing process is close to clean air.
4. Clean area
The clean area and non-clean area should be isolated to ensure that the air within a certain range can be controlled.
Implementation process of ISO 8 cleanroom
1. Calculate the cleanliness of the space
First, use the air detection instrument to calculate the cleanliness of the original environment, as well as the content of dust, mold, etc.
2. Formulate design standards
According to the needs of product production, make full use of production conditions and formulate design standards that meet production requirements.
3. Environmental simulation
Simulate the workshop use environment, test the air purification equipment, test the purification effect of the system and the reduction of target objects such as particles, bacteria and odors.
4. Equipment installation and debugging
Install the air purification equipment and debug it to ensure the stable operation of the system.
5. Environmental testing
Use air detection instruments to test the workshop cleanliness, particles, bacteria and other indicators to confirm that the workshop air quality meets the requirements.
6. Clean area division
According to the design requirements, the workshop is divided into clean areas and non-clean areas to ensure the cleanliness of the entire workshop space.
Advantages of clean room technology
1. Improve production efficiency
In the environment of a dust-free cleanroom, the production process of the product is easier for producers to focus on production than in a general production workshop. Due to the better air quality, the physical, emotional and mental levels of employees can be guaranteed, thereby improving production efficiency.
2. Increase product quality stability
The quality of products produced in a dust-free clean room environment will be more stable, because products produced in a clean environment often have better stability and consistency.
3. Reduce production costs
Although the cost of dust-free workshop construction is high, it can reduce errors in the production process and reduce the break-even point, thereby reducing the overall production cost.
In short, the construction of ISO 8 cleanroom is an important part of modern highly-clean production technology. It has the advantages of ensuring product quality, improving production efficiency and increasing economic benefits, and will have a positive role in promoting the standardization of production in related industries and industrial upgrading.
Post time: Aug-07-2024