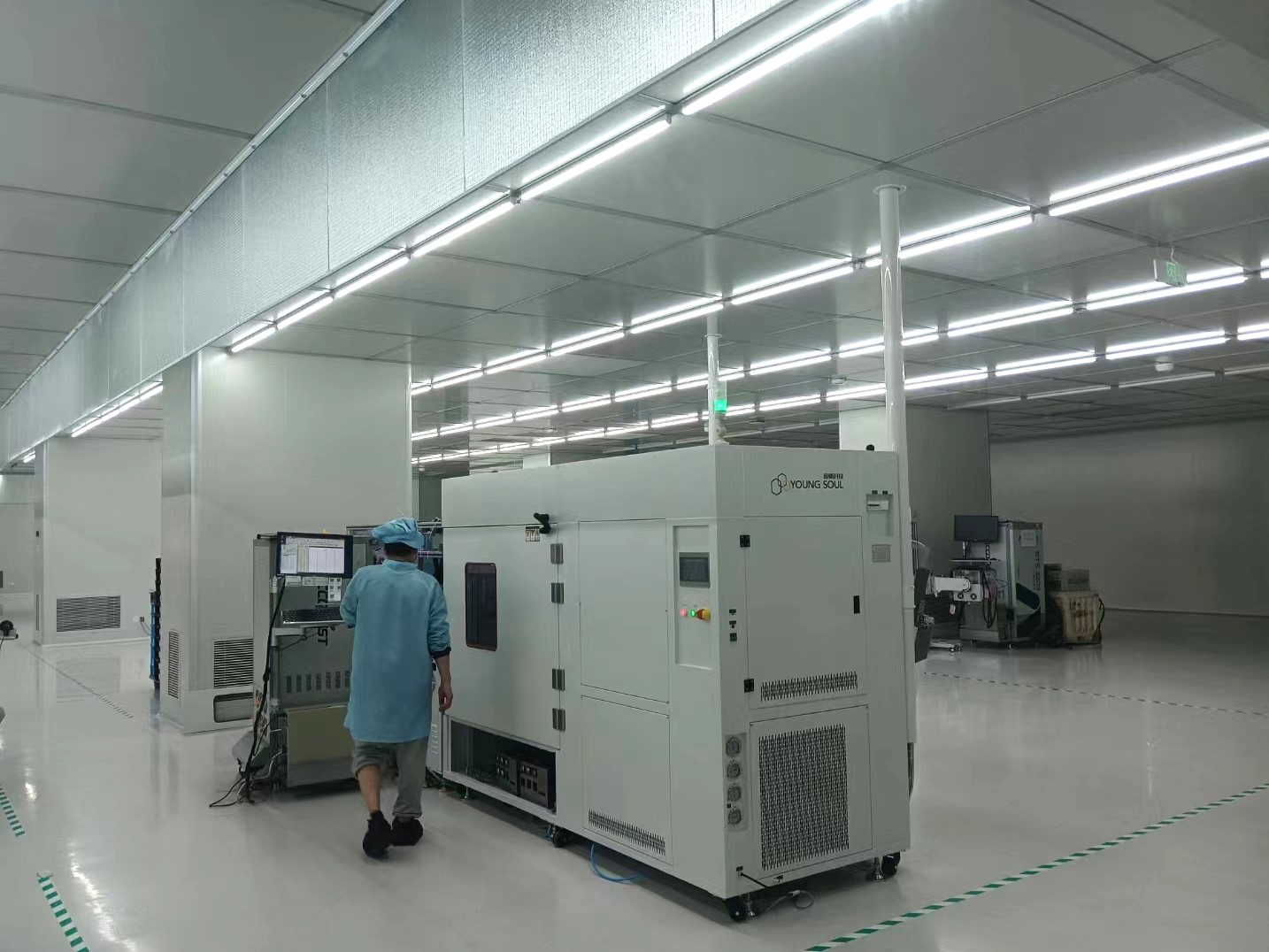
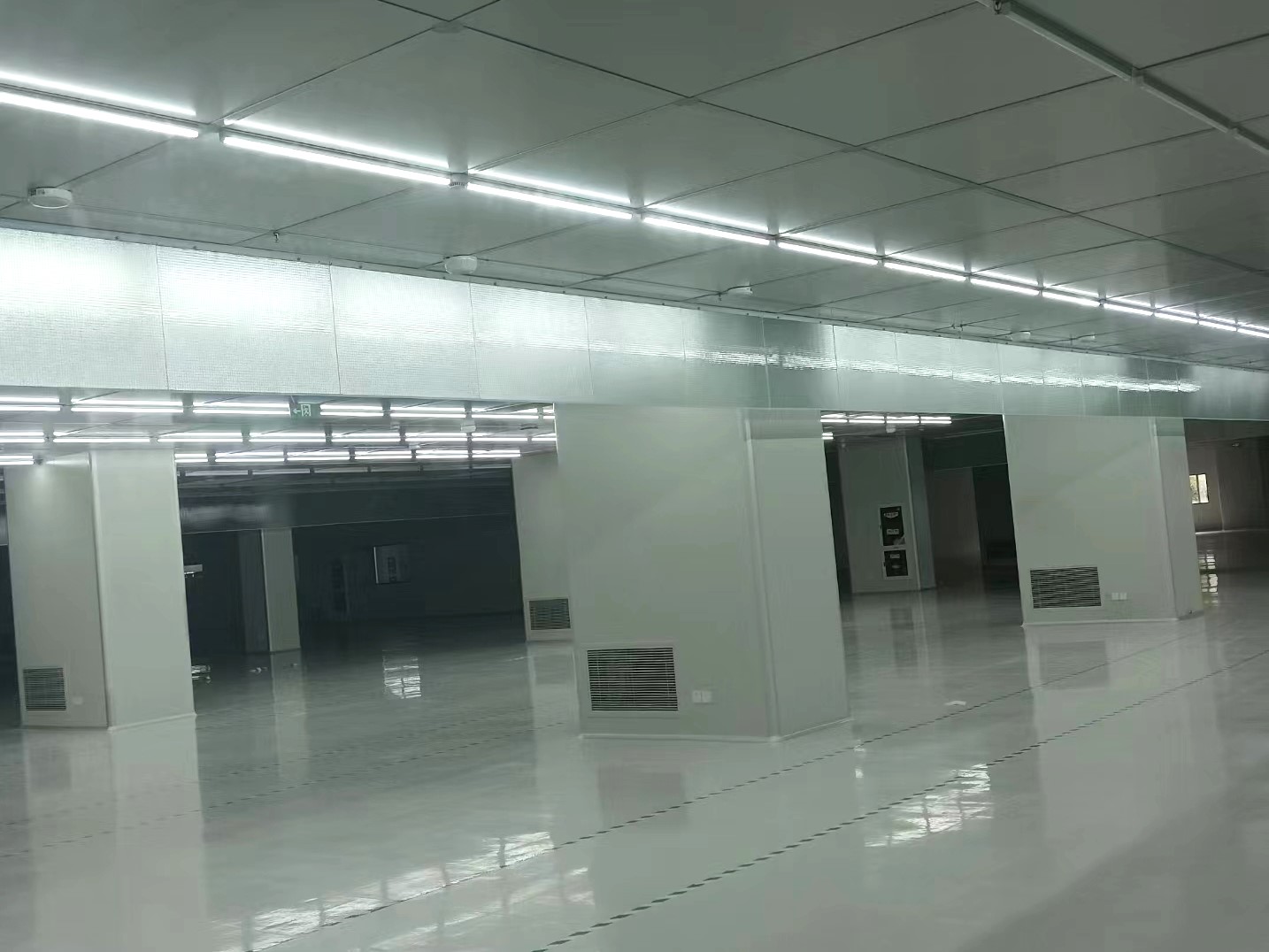
Injection molding in clean room allows medical plastics to be produced in a controlled clean environment, ensuring a high-quality product without the worry of contamination. Whether you are an expert or new to the clean room world, this can be a complex process, so this article answers the most common questions about the injection molding process for medical plastics.
Why do you need a clean room for injection molding?
When the product being manufactured requires an element of contamination control, injection molding requires a clean room where cleanliness, precision, and compliance are strictly regulated. Manufacturing products for the medical industry means that the output of these processes often comes into direct contact with the human body, so contamination control is a top priority.
Most clean room used to manufacture medical devices must meet ISO Class 5 to Class 8 standards, but all active implantable medical devices and their accessories fall into the highest risk category (Class III), which means that GMP clean room may be required.
By manufacturing in clean room environment, you can ensure that the process is free of contaminants that could affect the quality, safety, and functionality of the final product.
What are the key features that an injection molding clean room needs to have?
The specific functionality of any clean room will depend on variables such as available space, height restrictions, accessibility requirements, transportability needs, and the overall processes being conducted in the clean room itself. Here are some of the key features to consider when choosing the right clean room for injection molding.
Transportability: Does your clean room need to cover specific parts of a machine as part of the injection molding process? Does the machine produce both non-medical and medical components? If this is the case, then consider softwall clean room on casters for easy movement and transportation, enabling you to create a controlled environment when necessary.
Tool Changing: Flexibility is key in injection molding manufacturing, as one machine may be used to produce a range of different products. Therefore, accessibility is required to change the tooling used to produce a part. A mobile clean room can simply be moved to access the tooling area, however, more permanent structures require more innovative solutions such as a HEPA-lite canopy with sliding filtration to allow crane access from above.
Materials: Softwall clean room panels are commonly used in injection molding to achieve an ISO Class environment and benefit from being lightweight, transportable, and easy to build. Hardwall clean room panels allow for a more rigid structure with the option of additional features such as shelving units and transfer hatches. Monoblock panels offer further capacity for tighter environmental control, however, are more costly and offer less flexibility in accessibility than softwall or hardwall panels.
Air Filtration and Ventilation: Clean rooms for injection molding machines typically require fan filter units (FFUs) to be located directly above the platens and molding tools to ensure optimal filtration where it is needed most. This will impact the design and layout of your facility and will dictate the layout of the machines within the clean room.
Efficient Workflow: Anyone entering the clean room to operate a machine will need to first enter a gowning area to ensure contamination from the outside environment is minimized. Injection molding machines typically have conveyors or shot ports to facilitate the movement of finished products, so your clean room processes and workflows need to account for this to ensure equipment and personnel flow follows a logical, contamination-reducing path.
How do you ensure your clean room is compliant throughout the injection molding process?
Ensuring compliance requires a combination of careful planning, regular monitoring, and adherence to strict protocols throughout the life of the clean room.
The first stage of clean room compliance is before construction begins. The development of a User Requirement Specification (URS) is critical for a GMP clean room and must take into account regulatory and process requirements – what GMP classifications do you need to work under, and are there any process requirements such as temperature or humidity control?
Regular validation and requalification is a requirement for all cleanrooms to ensure you remain compliant – the frequency of requalification will depend on the regulatory standards the clean room adheres to.
If you are using one injection molding machine to produce multiple products, you may not need a clean environment for each product. If your clean room is used intermittently, it is highly recommended that you obtain a particle counter as you will need to be able to measure particle levels within the clean room before production begins to ensure compliance during use.
Ensuring that the personnel operating the clean room environment are properly trained is a key part of compliance. Not only are they responsible for following strict clean room protocols such as protective clothing, daily manufacturing procedures, entry and exit procedures, and ongoing cleaning, they are also responsible for maintaining appropriate documentation.
In summary, the answers to the above questions go some way towards providing a clear understanding of why clean rooms are critical in the injection molding process and the important factors to consider when designing such an environment.
Post time: Feb-10-2025