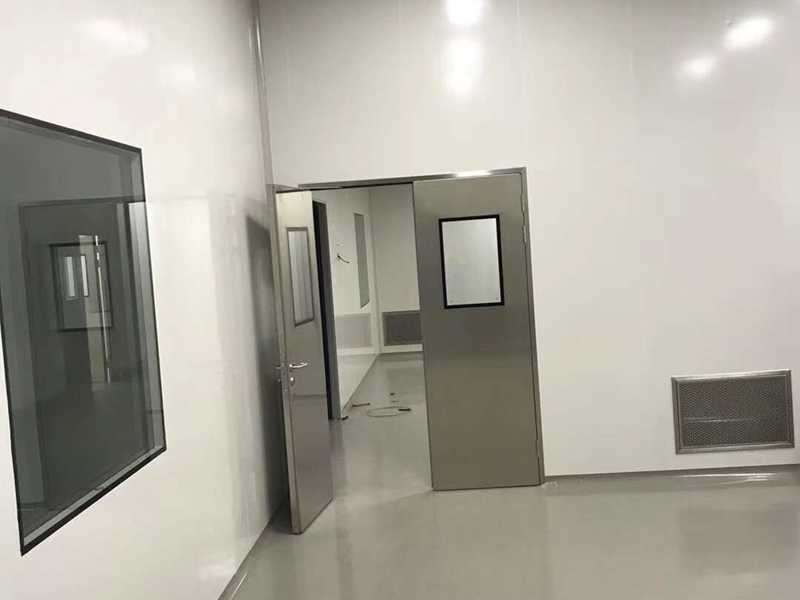
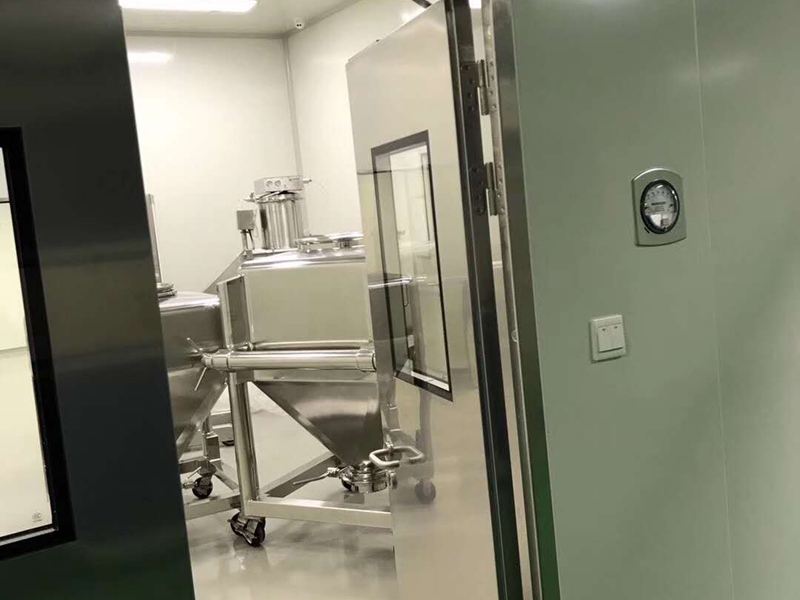
With the rapid development of modern industry, clean room workshops have been widely used in all walks of life, but many people do not have a comprehensive understanding of clean room workshops, especially some related practitioners, which will directly cause the wrong use of clean room workshops, resulting in the destruction of the workshop environment and the increase of product defective rate. So what is a clean room workshop? What kind of evaluation criteria is it divided by? How to correctly use and maintain the environment of the clean room workshop?
Clean room workshop is also called dust free room. It refers to a specially designed room that removes pollutants such as microparticles, harmful air, and bacteria in the air within a certain space range, and controls the indoor temperature, cleanliness, indoor pressure, airflow speed and airflow distribution, noise vibration, lighting, and static electricity within a certain range of requirements.
Simply put, clean room workshop is designed for standardized production space that requires hygiene levels for certain production environments. It has broad application prospects in microelectronics, opto-magnetic technology, bioengineering, electronic equipment, precision instruments, aerospace, food industry, cosmetics industry, scientific research and teaching, and other fields.
There are three main standards for clean room classification that are most commonly used at present.
1. ISO standard of the International Organization for Standardization: clean room rating based on the dust content per cubic meter of air.
2. FS 209D standard of the United States: based on the particle content per cubic foot of air as the rating basis.
3. GMP (Good Manufacturing Practice) rating standard: mainly in the pharmaceutical industry. The smaller the value, the higher the cleanliness level.
Many users of cleanrooms know to find a professional team to build but ignore the post-construction management, resulting in some cleanrooms being qualified when they are delivered for use. After a period of operation, the particle concentration is overrun, so the defective rate of goods increases, and some are even abandoned.
Cleanroom maintenance work is very critical. It is not only related to product quality, but also affects the service life of cleanrooms. When analyzing the proportion of cleanroom pollution sources, the pollution caused by human factors accounts for 80%. It is mainly fine particulate matter and microbial pollution.
(1) Personnel must wear dust-free clothing before entering the clean room.
The anti-static protective clothing series includes anti-static clothing, anti-static shoes, anti-static caps and other products. They can reach the cleanliness level of class 1,000 and 10,000 through repeated washing. The anti-static material can reduce the adsorption of dust, hair and other fine pollutants, and at the same time can isolate the sweat, dandruff, bacteria and other substances produced by human metabolism. Reduce the pollution caused by human factors.
(2) Use qualified wiping products according to the clean room level.
Using unqualified wiping products is easy to pilling and dandruff, breeding bacteria, not only polluting the workshop environment, but also causing product contamination.
Made of polyester long fiber or ultra-fine long fiber, it feels soft and delicate, has good flexibility, and has good wrinkle resistance and wear resistance.
Weaving processing, not easy to pilling, not easy to dandruff. Packaging is completed in the dust-free workshop, and it is not easy to breed bacteria after ultra-clean cleaning.
Use special edge sealing processes such as ultrasonic and laser to ensure that the edges are not easy to fall apart.
It can be used in production operations in clean rooms from class 10 to class 1000 to remove dust from the surface of products, such as LCD/microelectronics/semiconductor products. It can also be used to clean polishing machines, tools, magnetic media surfaces, glass, and the inside of polished stainless steel pipes.
Post time: Mar-19-2025