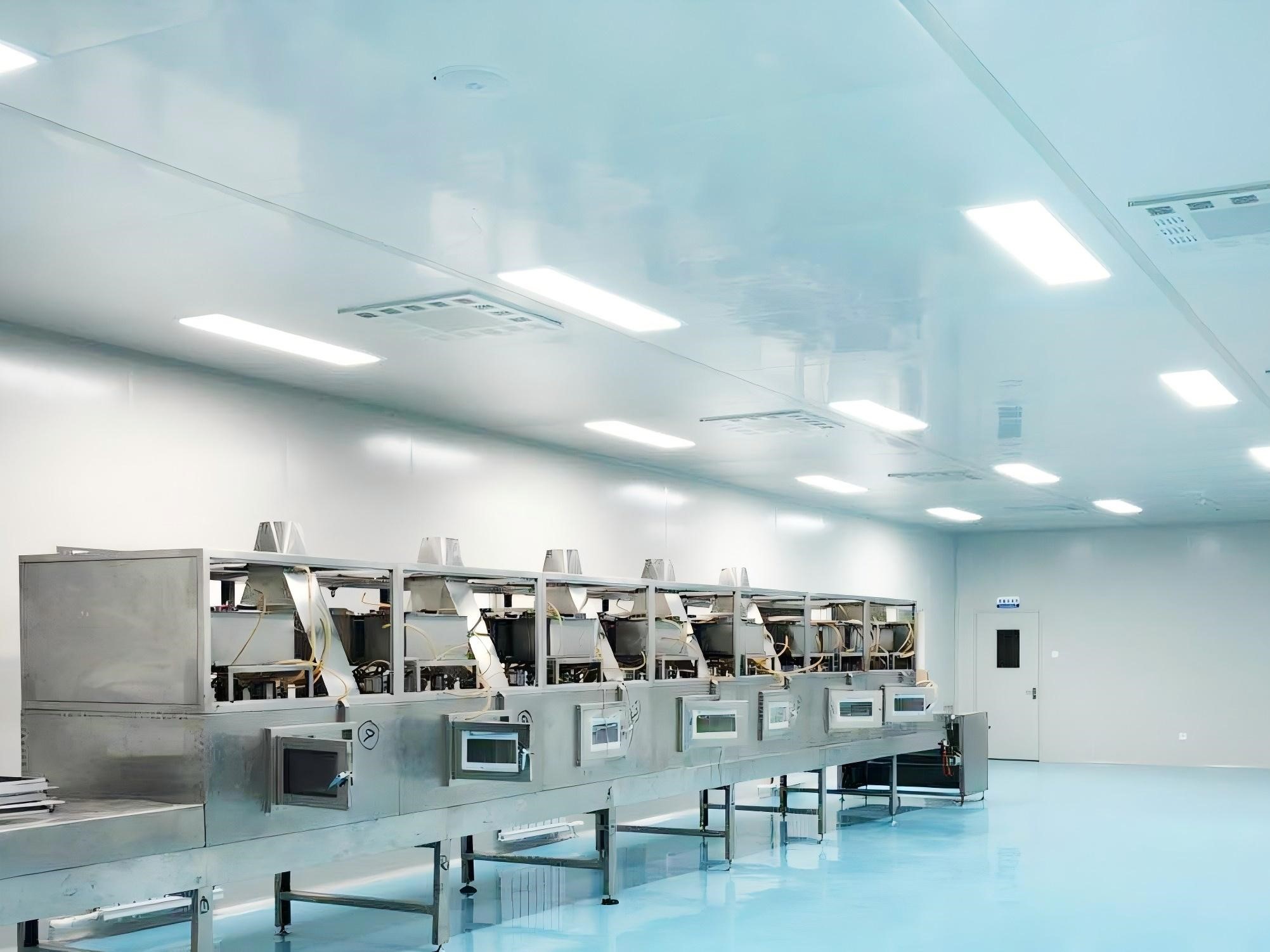
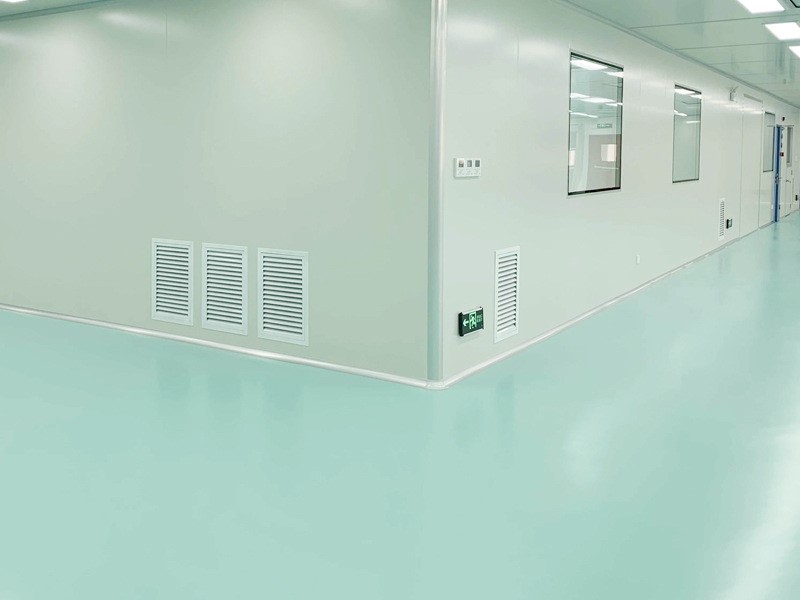
Pharmaceutical clean room design: The pharmaceutical factory is divided into main production area and auxiliary production area. The main production area is divided into clean production area and general production area. Although it is general, there are hygiene requirements and no cleanliness level requirements such as API synthesis, antibiotic fermentation and refining.
Plant area division: The factory production area includes clean production area and general production area. The production area in the factory should be separated from administrative area and living area, reasonably laid out, with appropriate spacing, and should not interfere with each other. The layout of the production area should consider the separate entry of personnel and materials, the coordination of personnel and logistics, the coordination of process flow, and the coordination of cleanliness level. The clean production area should be located in a clean environment in the factory, and irrelevant personnel and logistics do not pass through or pass through less. The general production area includes water preparation, bottle cutting, dark rough washing, sterilization, light inspection, packaging and other workshops and visiting corridors for API synthesis, antibiotic fermentation, Chinese medicine fluid extract, powder, premix, disinfectant, and packaged injection. The API production area of A pharmaceutical clean room that also has API synthesis, as well as areas with severe pollution such as waste treatment and boiler room, should be placed on the leeward side of the area with the most wind direction throughout the year.
Principles for the setting of clean rooms(areas) with the same air cleanliness level should be relatively concentrated. Clean rooms (areas) with different air cleanliness levels should be arranged with high inside and low outside according to the level of air cleanliness, and should have a device indicating pressure difference or a monitoring alarm system.
Clean rooms (areas): Clean rooms (areas) with high air cleanliness levels should be arranged as far as possible in areas with the least external interference and the least irrelevant personnel, and should be as close to the air conditioning room as possible. When rooms (areas) with different cleanliness levels are interconnected (people and materials entering and exiting), they should be handled according to the measures of people purification and cargo purification.
Clean goods storage area: The storage area for raw and auxiliary materials, semi-finished products and finished products in clean room (area) should be as close as possible to the production area related to it to reduce mixing and contamination during the transfer process.
Highly allergenic drugs: The production of highly allergenic drugs such as penicillin and β-lactam structures must be equipped with independent clean workshops, facilities and independent air purification systems. Biological products: Biological products should be equipped with their own production areas (rooms), storage areas or storage equipment according to the type, nature and production process of microorganisms. Chinese herbal medicines: The pretreatment, extraction, concentration of Chinese herbal medicines, as well as the washing or treatment of animal organs and tissues must be strictly separated from their preparations. Preparation room and sample weighing room: Clean rooms (areas) must have separate preparation rooms and sample weighing rooms, and their cleanliness levels are the same as those of clean rooms (areas) where the materials are used for the first time. For materials that need to be sampled in a clean environment, a sampling room should be set up in the storage area, and the air cleanliness level of the environment should be the same as that of the clean area (room) where the materials are used for the first time. Veterinary drug manufacturers without such conditions can take samples in the weighing room, but they must meet the above requirements. Clean rooms (areas) should have separate equipment and container cleaning rooms.
The equipment and container cleaning rooms of clean rooms (areas) below class 10,000 can be set up in this area, and the air cleanliness level is the same as that of the area. Equipment and containers in class 100 and class 10,000 clean rooms (areas) should be cleaned outside cleanroom, and the air cleanliness level of the cleaning room should not be lower than class 10,000. If it must be set up in a cleanroom (area), the air cleanliness level should be the same as that of the area. It should be dried after washing. Containers entering the sterile cleanroom should be disinfected or sterilized. In addition, a storage room for equipment and containers should be set up, which should be the same as the cleaning room, or a storage cabinet should be set up in the cleaning room. Its air cleanliness should not be lower than class 100,000.
Cleaning tools: The washing and storage room should be set up outside the clean area. If it is necessary to set up in cleanroom (area), its air cleanliness level should be the same as that of the area, and measures should be taken to prevent pollution.
Clean work clothes: The washing, drying and sterilization rooms for clean work clothes in areas of class 100,000 and above should be set up in cleanroom (area), and their cleanliness level should not be lower than class 300,000. The sorting room and sterilization room for sterile work clothes should have the same cleanliness level as the cleanroom (area) where these sterile work clothes are used. Work clothes in areas with different cleanliness levels should not be mixed.
Personnel cleanrooms: Personnel cleanrooms include shoe changing rooms, dressing rooms, washrooms, airlocks, etc. Toilets, shower rooms, and rest rooms should be set up according to process requirements and should not have adverse effects on the clean area.
Post time: Mar-07-2025