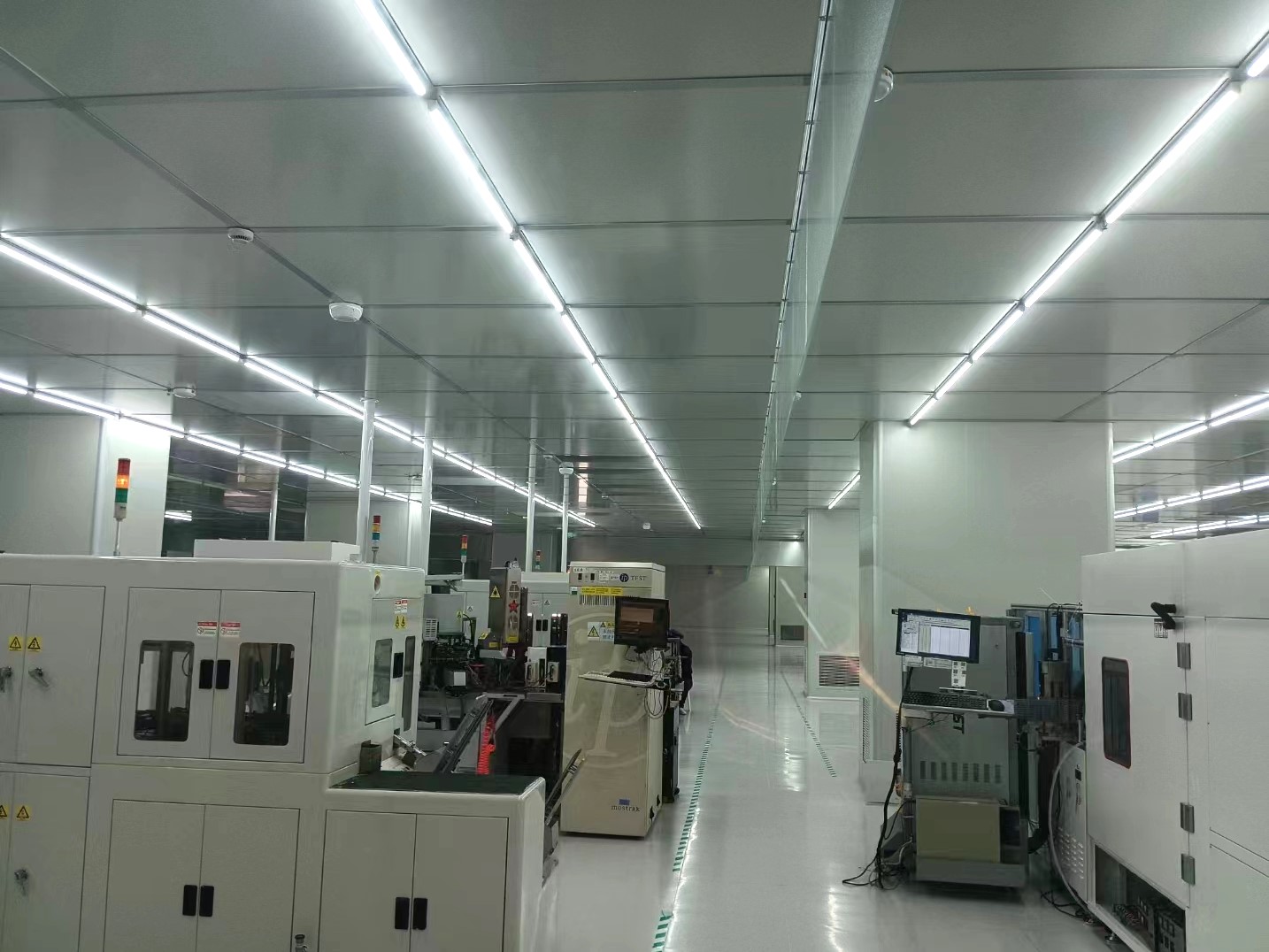
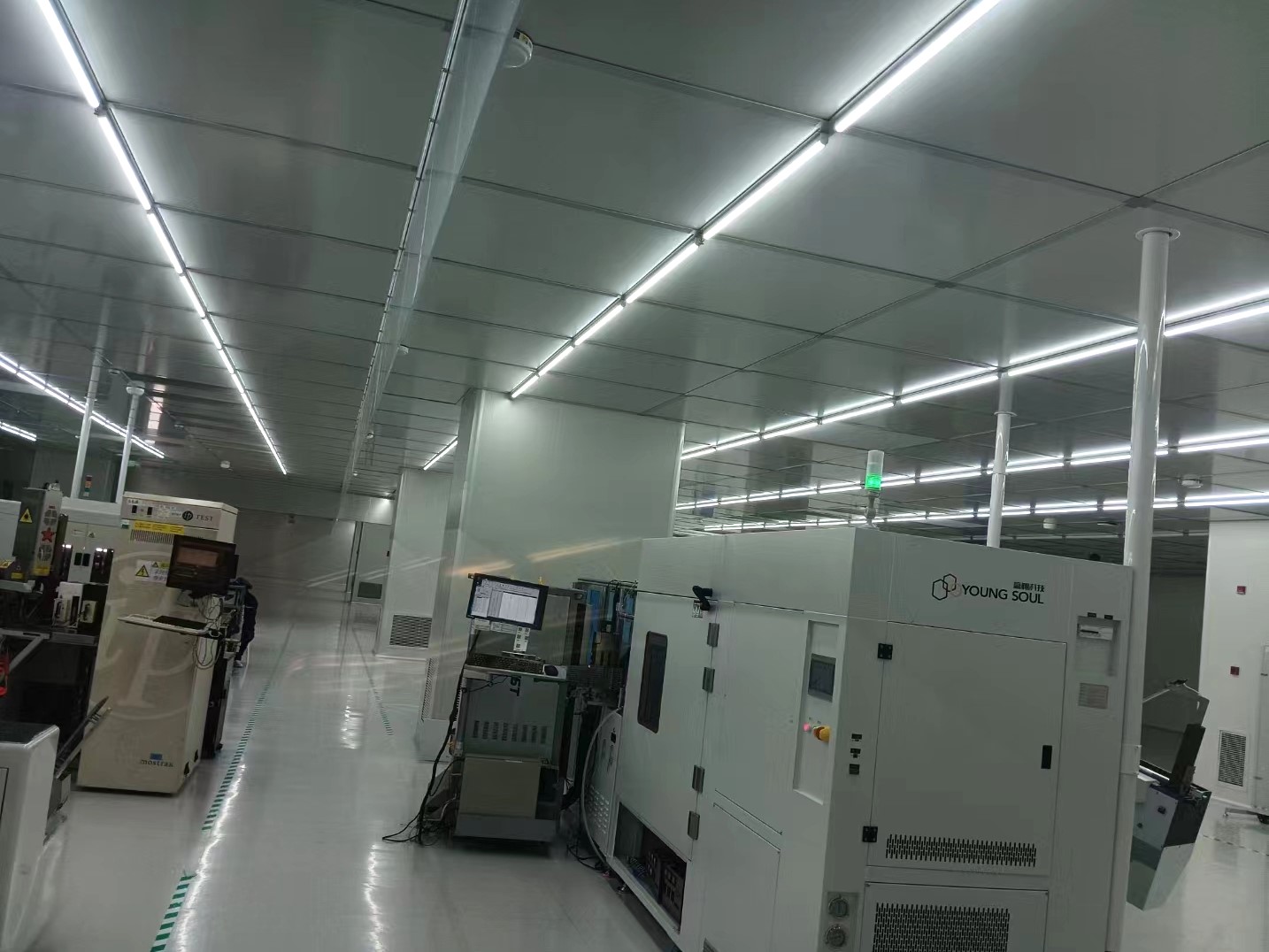
As a highly controlled environment, clean rooms are widely used in many high-tech fields. By providing a highly clean environment, the quality and performance of products are ensured, pollution and defects are reduced, and production efficiency and reliability are improved. The design and management of clean rooms in different fields need to be carried out according to specific needs and standards to meet specific cleanliness requirements. The following are the five major application areas of clean rooms:
Electronic clean room
Semiconductor manufacturing is one of the most important application scenarios of clean rooms. The chip manufacturing process, such as photolithography, etching, thin film deposition and other processes, has extremely high requirements for environmental cleanliness. Tiny dust particles may cause short circuits or other performance problems in chips. For example, in the production of chips with a process of 28 nanometers and below, it is necessary to carry out in ISO 3-ISO 4 clean rooms to ensure chip quality. The production of liquid crystal displays (LCDs) and organic light-emitting diode displays (OLEDs) is also inseparable from clean rooms. In the manufacturing process of these displays, such as liquid crystal perfusion, organic material coating and other links, a clean environment helps prevent defects such as dead pixels and bright spots on the screen.
Pharmaceutical clean room
The pharmaceutical industry is a major application of clean rooms. Whether it is the production of chemical drugs or biological drugs, all links from raw material processing to drug packaging need to be carried out in a clean environment. In particular, the production of sterile drugs, such as injections and ophthalmic preparations, requires extremely strict control of microorganisms and particles. Medical device production, such as implantable medical devices and surgical instruments, can be produced in a clean room to ensure the sterility and particle-free contamination of the devices, thereby ensuring the safety of patients. Hospital operating rooms, intensive care units (ICUs), sterile wards, etc. also belong to the category of clean rooms, which are used to prevent patient infection.
Aerospace clean room
The precision processing and assembly of aerospace parts requires a clean room environment. For example, in the processing of aircraft engine blades, tiny particle impurities may cause defects on the surface of the blades, which in turn affects the performance and safety of the engine. The assembly of electronic components and optical instruments in aerospace equipment also needs to be carried out in a clean environment to ensure that the equipment can work normally in the extreme environment of space.
Food clean room
For some high-value-added, perishable foods, such as infant formula and freeze-dried foods, clean room technology helps to extend the shelf life of products and ensure food safety. Using a clean room in the packaging of food can prevent microbial contamination and maintain the original quality of the food.
Precision manufacturing clean room
In precision machinery processing, such as the production of high-end watch movements and high-precision bearings, clean rooms can reduce the impact of dust on precision parts and improve product accuracy and service life. The manufacturing and assembly process of optical instruments, such as photolithography lenses and astronomical telescope lenses, can avoid scratches, pitting and other defects on the lens surface in a clean environment to ensure optical performance.
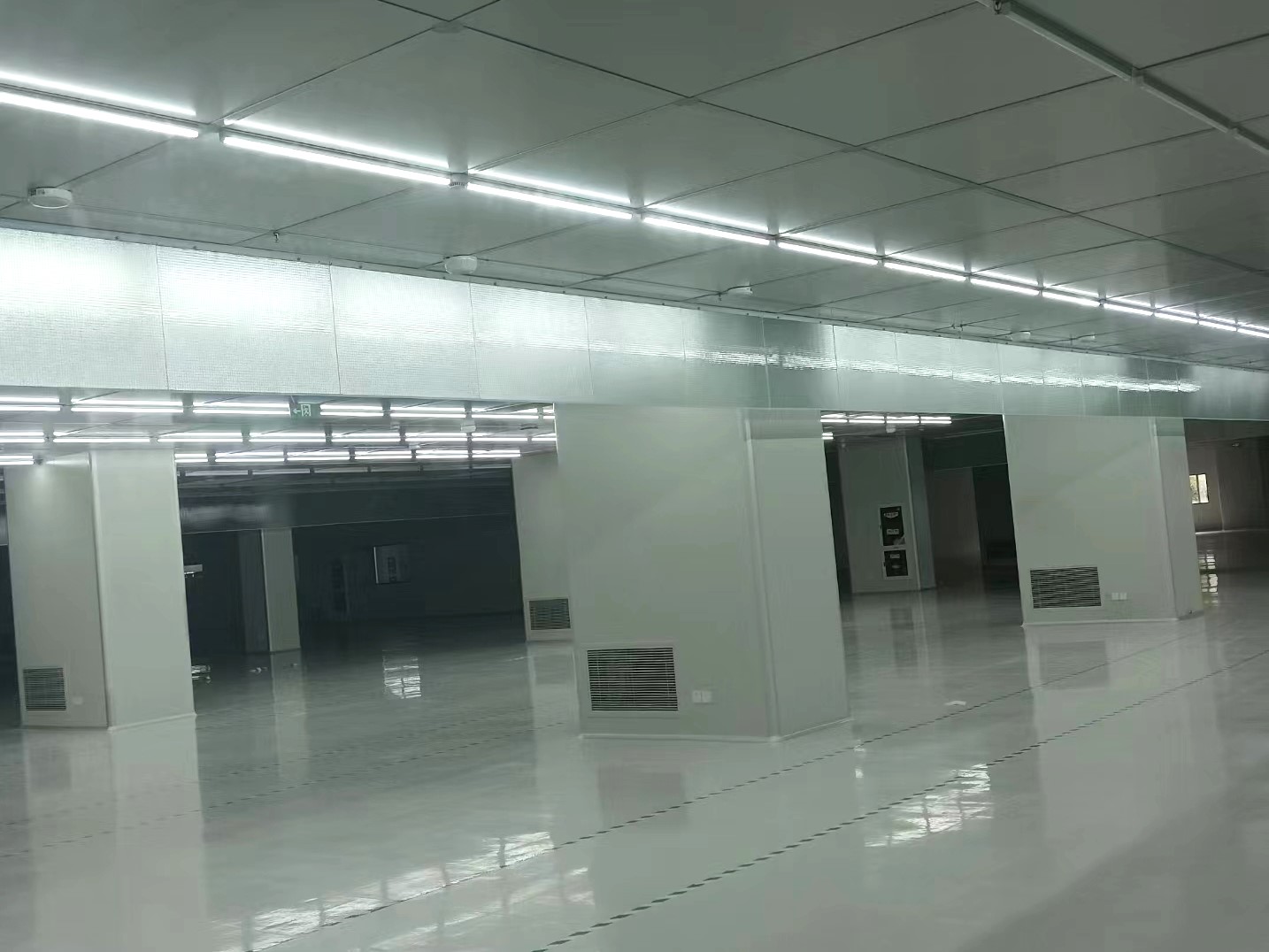
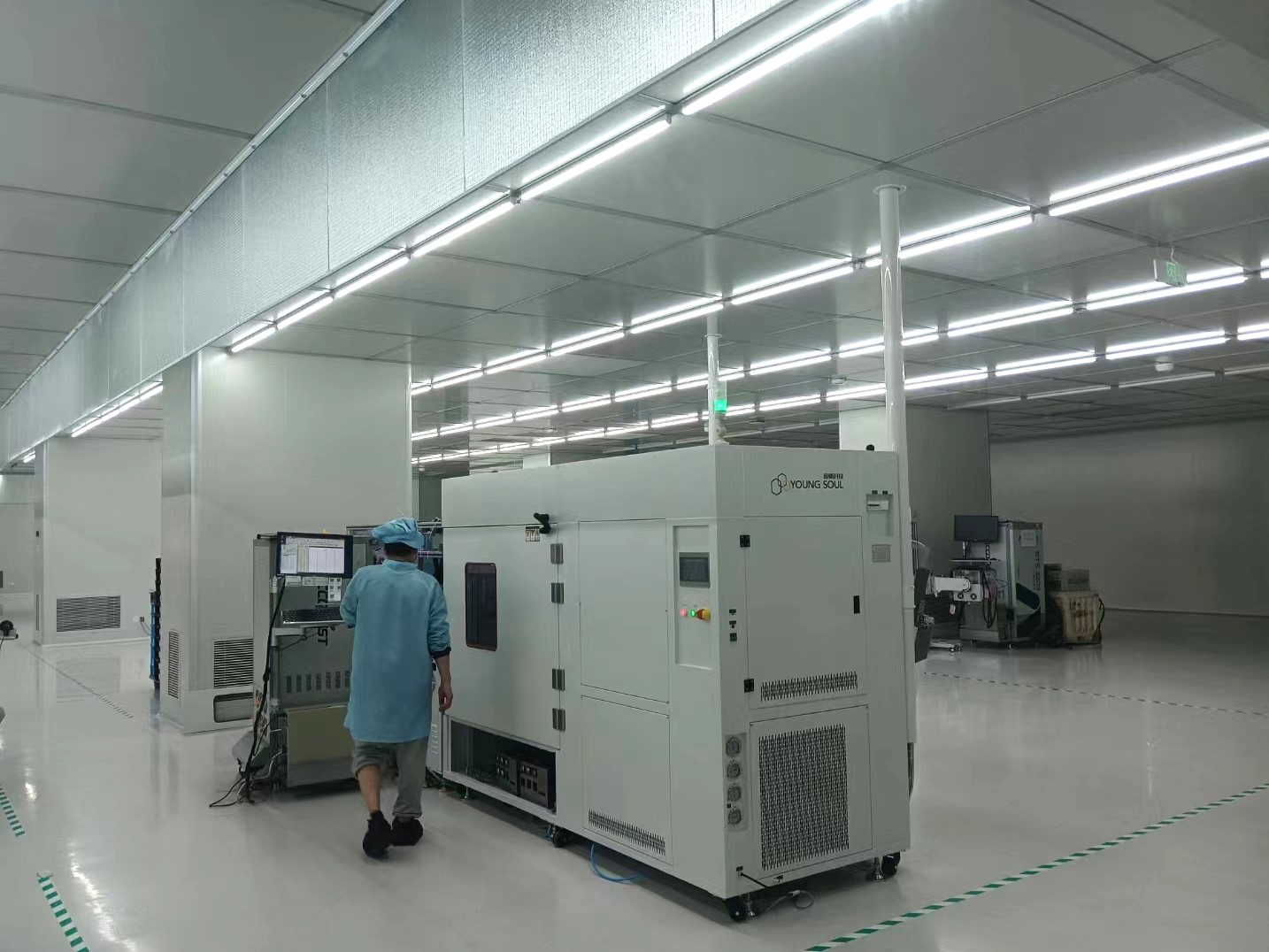
Post time: Feb-11-2025