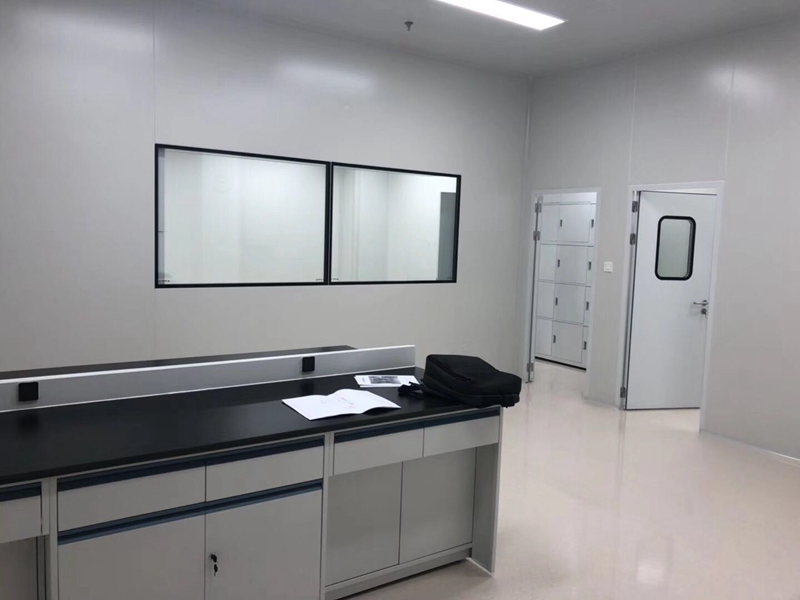
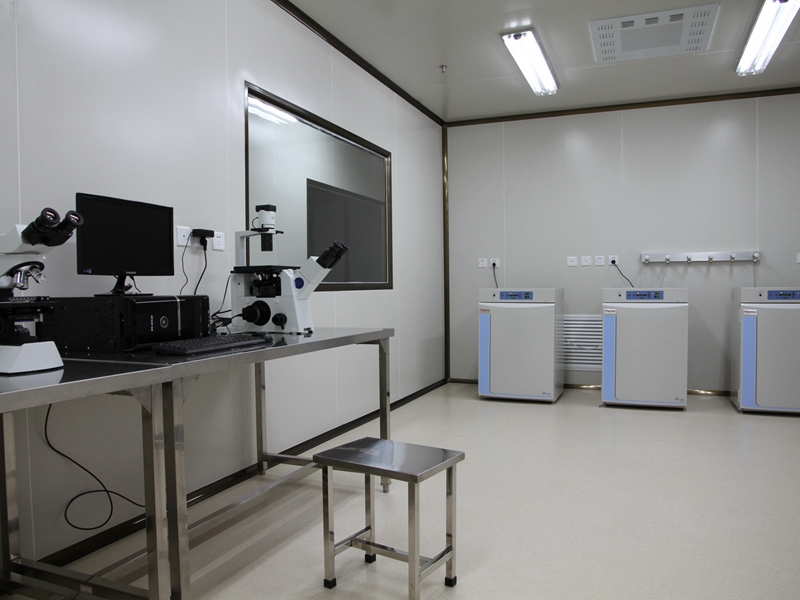
Cleanroom project refers to the discharge of pollutants such as microparticles, harmful air, bacteria, etc. in the air within a certain air range, and the control of indoor temperature, cleanliness, indoor pressure, airflow speed and distribution, noise vibration, lighting, static electricity, etc. within a certain required range. We call such an environmental process as cleanroom project. A complete cleanroom project involves more aspects, including eight parts: decoration and maintenance structure system, HVAC system, ventilation and exhaust system, fire protection system, electrical system, process pipeline system, automatic control system and water supply and drainage system. These components together constitute the complete system of cleanroom project to ensure its performance and effect.
1. Clenroom system
(1). Decoration and maintenance structure system
The decoration and decoration link of cleanroom project usually involves specific decoration of the system of enclosure structure such as ground, ceiling and partition. In short, these parts cover the six surfaces of the three-dimensional enclosed space, namely the top, wall and ground. In addition, it also includes doors, windows and other decorative parts. Different from general home decoration and industrial decoration, cleanroom project pays more attention to specific decoration standards and details to ensure that the space meets specific cleanliness and hygiene standards.
(2). HVAC system
It covers the chiller (hot water) unit (including water pump, cooling tower, etc.) and air-cooled pipe machine level and other equipment, air conditioning pipeline, combined purification air conditioning box (including mixed flow section, primary effect section, heating section, refrigeration section, dehumidification section, pressurization section, medium effect section, static pressure section, etc.) are also taken into account.
(3). Ventilation and exhaust system
The ventilation system is a complete set of devices consisting of air inlet, exhaust outlet, air supply duct, fan, cooling and heating equipment, filter, control system and other auxiliary equipment. The exhaust system is a whole system consisting of exhaust hood or air inlet, cleanroom equipment and fan.
(4). Fire protection system
Emergency passage, emergency lights, sprinkler, fire extinguisher, fire hose, automatic alarm facilities, fireproof roller shutter, etc.
(5). Electrical system
It includes three components: lighting, power and weak current, specifically covering purification lamps, sockets, electrical cabinets, lines, monitoring and telephone and other strong and weak current systems.
(6). Process piping system
In cleanroom project, it mainly includes: gas pipelines, material pipelines, purified water pipelines, injection water pipelines, steam, pure steam pipelines, primary water pipelines, circulating water pipelines, emptying and draining water pipelines, condensate, cooling water pipelines, etc.
(7). Automatic control system
Including temperature control, temperature control, air volume and pressure control, opening sequence and time control, etc.
(8). Water supply and drainage system
System layout, pipeline selection, pipeline laying, drainage accessories and small drainage structure, cleanroom circulation system, these dimensions, drainage system layout and installation, etc.
Food industry, quality inspection station, electronics industry, hospital, medical care industry, aerospace, scientific research institutions, pharmaceutical factories, microelectronics, biological clean room and other industries provide various types and class 100000 cleanliness levels of clean workshops and cleanroom air conditioning system design, installation and construction, commissioning, after-sales service and other overall solutions. The biosafety laboratory designed by our company guarantees the construction quality and meets the requirements of general standard building technical specifications.
2. Cleanroom service requirements
(1). Cleanroom services
① Design and renovate air-conditioned cleanrooms and clean, dust-free and sterile laboratories of various purification levels, process requirements and floor plans.
② Renovate cleanrooms with special requirements such as relative negative pressure, high temperature, fire and explosion prevention, sound insulation and silencing, high-efficiency sterilization, detoxification and deodorization, and anti-static.
③ Construct lighting, electrical facilities, power, electrical control systems and air conditioning automatic control systems that match the cleanroom.
3. Cleanroom applications
(1). Hospital biological cleanrooms
Hospital biological cleanrooms mainly include clean operating rooms and clean wards. The clean wards of hospitals are mainly places where fungi are strictly controlled to prevent patients from being infected or causing serious consequences.
(2). P-level series laboratories
① P3 laboratories are biosafety level 3 laboratories. Biosafety laboratories are divided into four levels according to the degree of harm of microorganisms and their toxins, with level 1 being low and level 4 being high. They are divided into two categories: cell level and animal level, and the animal level is further divided into small animal level and large animal level. The first P3 laboratory in my country was built in 1987 and was mainly used for AIDS research.
②P4 laboratory refers to the biosafety level 4 laboratory, which is specially used for the research of highly infectious diseases. It is the highest level of biosafety laboratory in the world. There is no such laboratory in China at present. According to relevant experts, the safety measures of P4 laboratories are stricter than those of P3 laboratories. Researchers must not only wear fully enclosed protective clothing but also carry oxygen cylinders when entering.
(3). Cleanroom engineering of factories and workshops
The construction methods can be divided into civil engineering and prefabricated types.
The prefabricated clean workshop system is mainly composed of air conditioning supply system, return air system, return air, exhaust unit, enclosure structure, human and material clean units, primary, middle and high level air filtration, gas and water system, power and lighting, working environment parameter monitoring and alarm, fire protection, communication and anti-static floor treatment.
①GMP clean workshop purification parameters:
Air change times: class 100000 ≥15 times; class 10000 ≥20 times; class 1000 ≥30 times.
Pressure difference: main workshop to adjacent room ≥5Pa;
Average air velocity: class 100 clean workshop 03-0.5m/s;
Temperature: >16℃ in winter; <26℃ in summer; fluctuation ±2℃. Humidity 45-65%; humidity in GMP clean workshop is preferably around 50%; humidity in electronic workshop is slightly higher to avoid static electricity. Noise ≤65dB(A); fresh air supplement is 10%-30% of the total air supply; illumination: 300LX.
②GMP workshop structural materials:
The wall and ceiling panels of the clean workshop are generally made of 50mm thick sandwich color steel plates, which are beautiful and rigid. Arc corner doors, window frames, etc. are generally made of special anodized aluminum profiles;
The floor can be made of epoxy self-leveling floor or high-grade wear-resistant plastic floor. If there is an anti-static requirement, the anti-static type can be selected;
The air supply and return ducts are made of hot-dip galvanized sheet, and the flame-retardant PF foam plastic sheet with good purification and heat preservation effect is pasted;
The hepa box uses a stainless steel frame, which is beautiful and clean, and the perforated mesh plate uses a painted aluminum plate, which is rust-proof and dust-proof and easy to clean.
(4). Electronic and physical cleanroom engineering
Generally applicable to electronic instruments, computer rooms, semiconductor factories, automobile industry, aerospace industry, photolithography, microcomputer manufacturing and other industries. In addition to air cleanliness, it is also necessary to ensure that the requirements of anti-static are met.
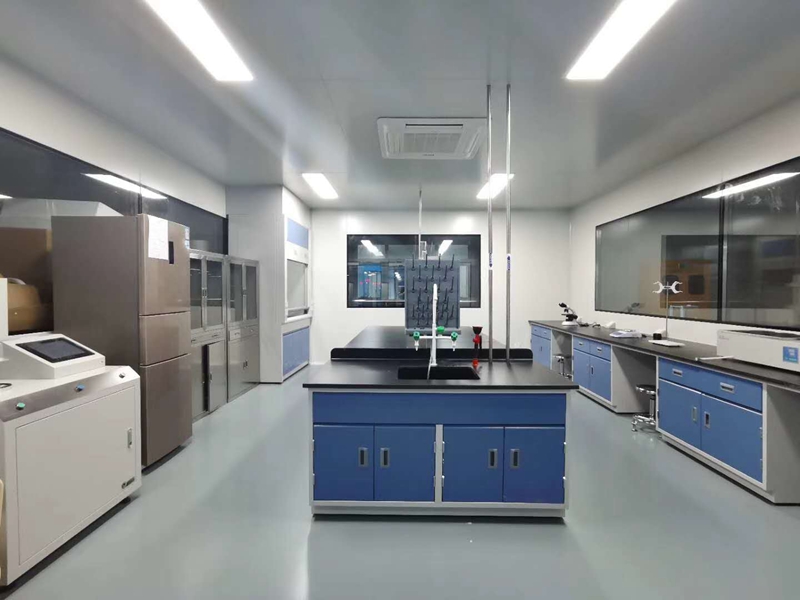
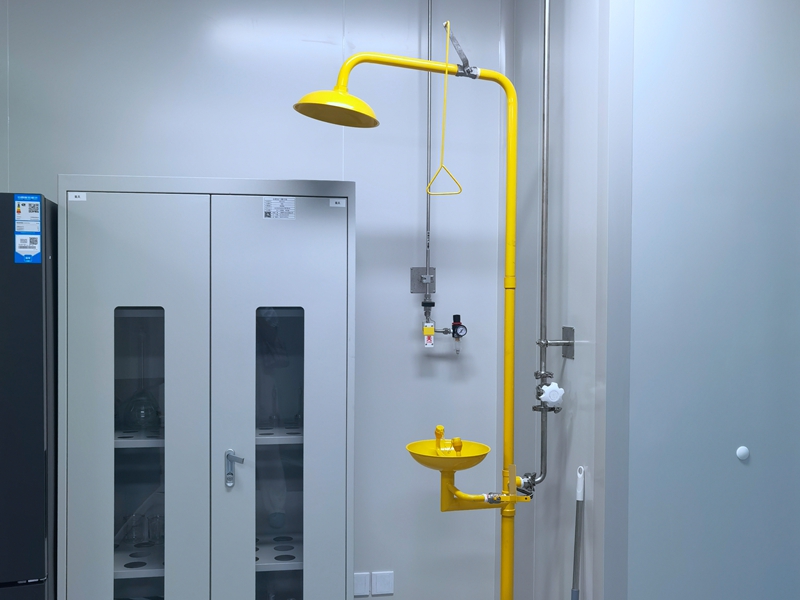
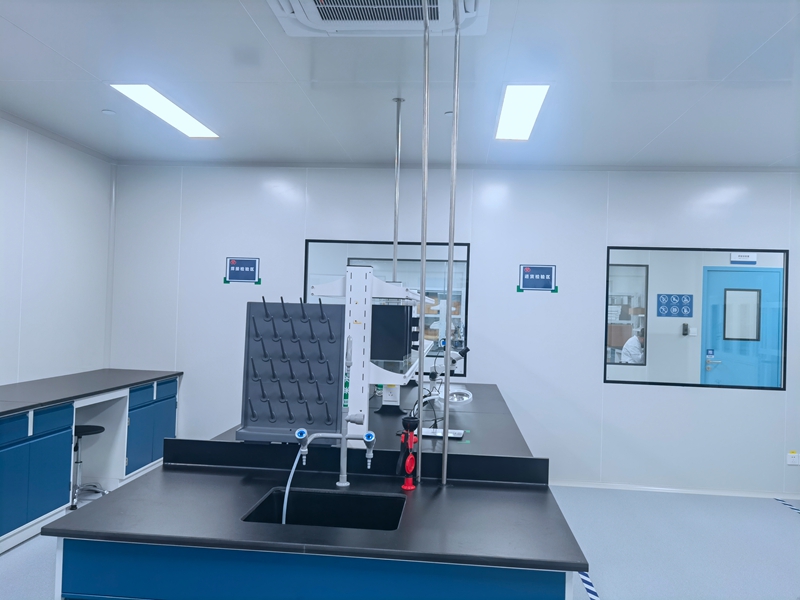
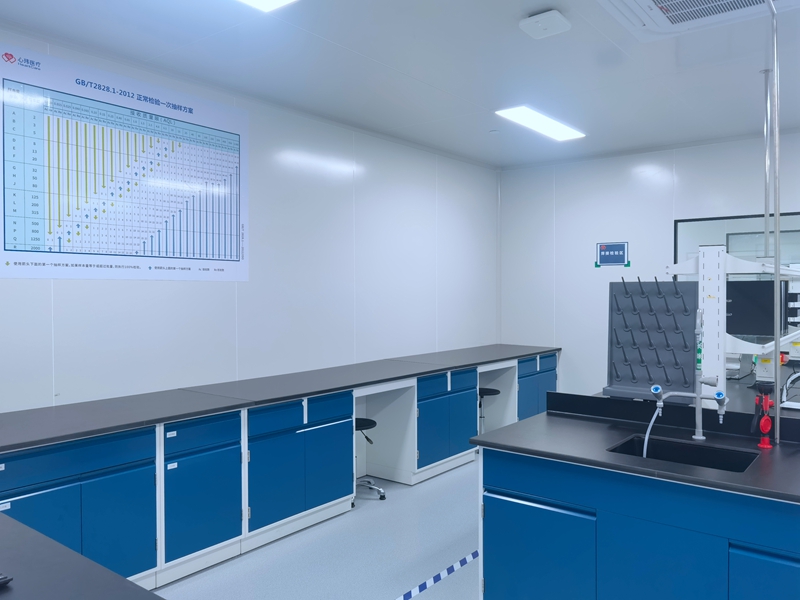
Post time: Feb-28-2025