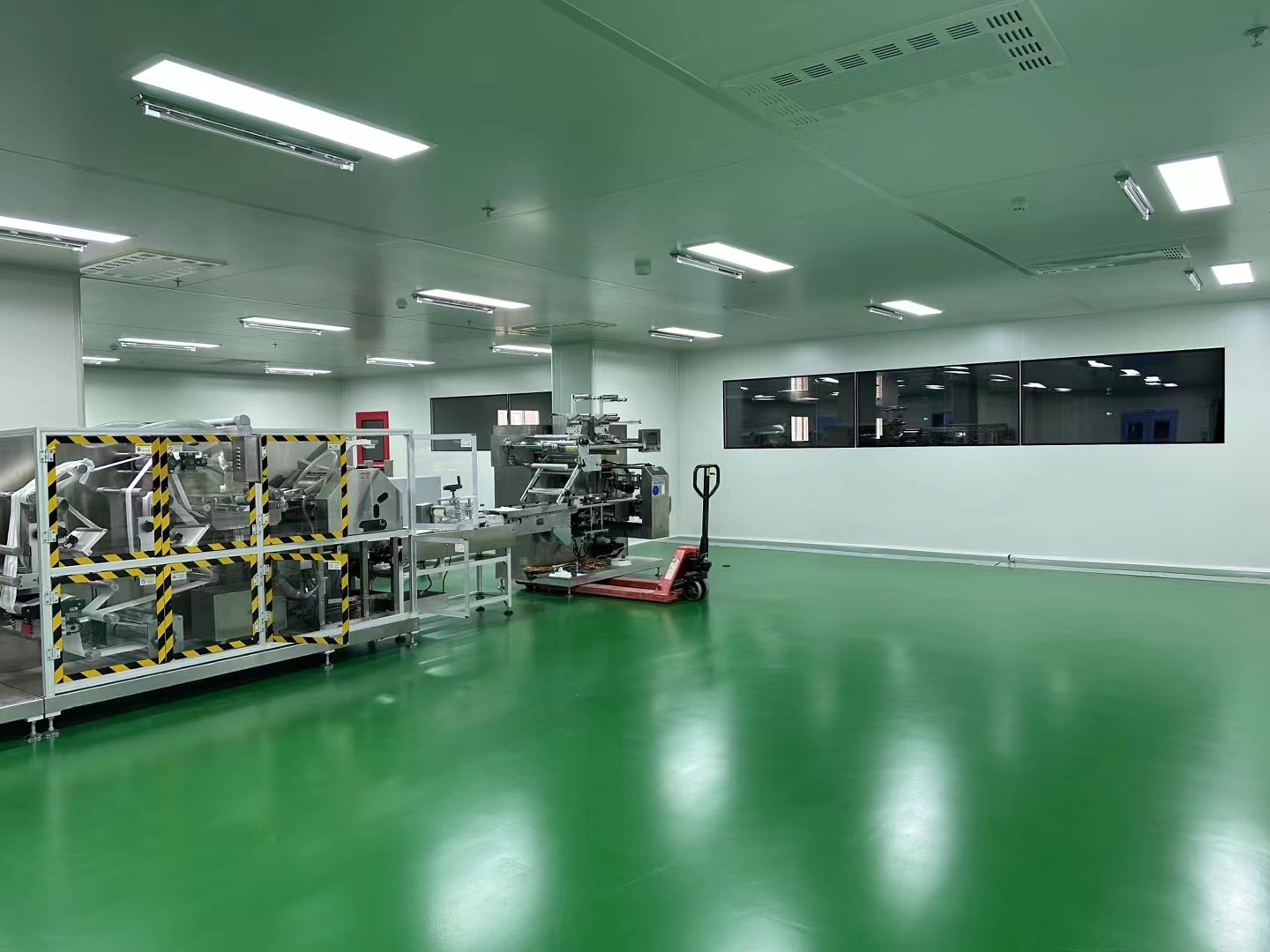
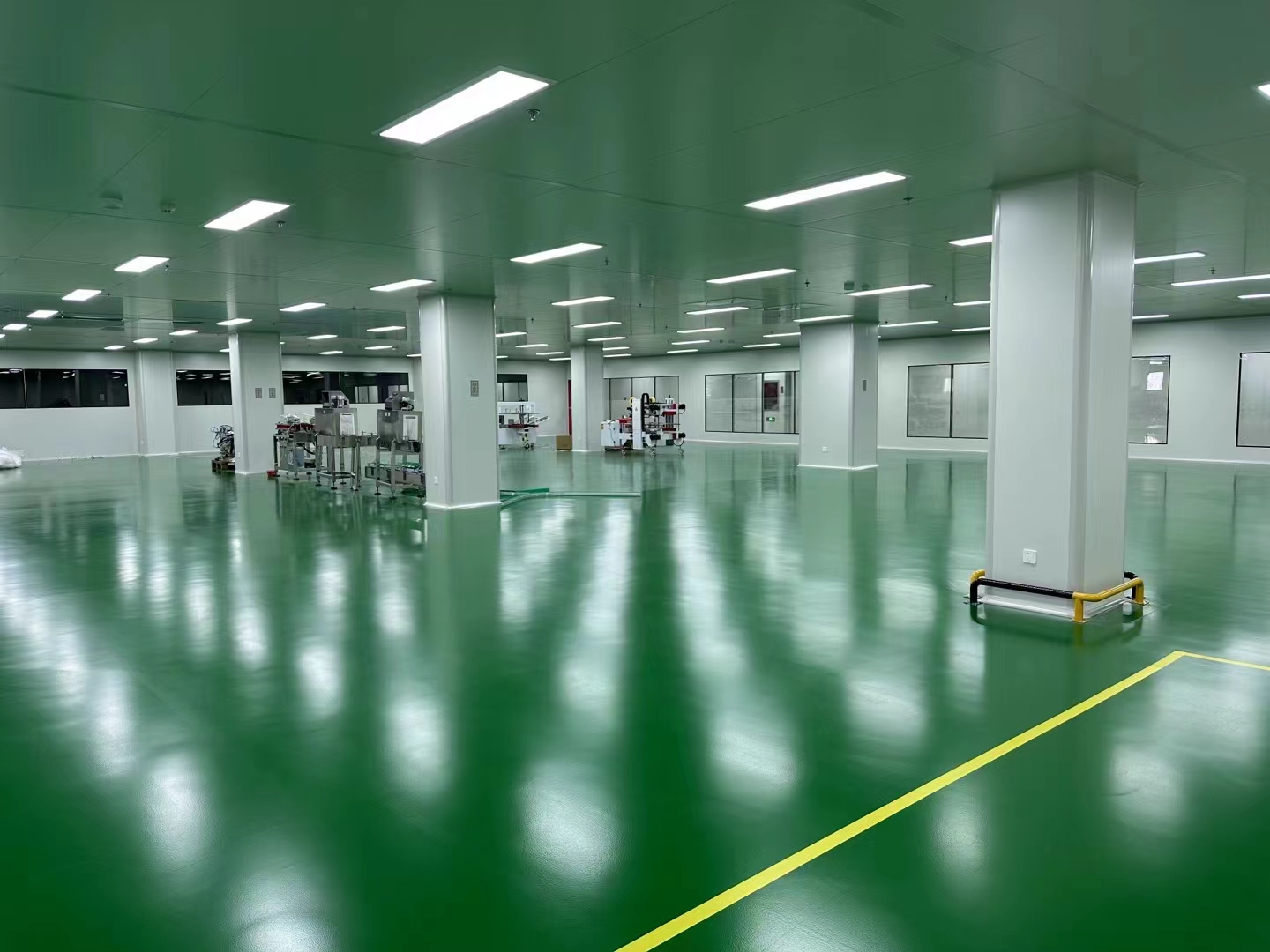
As a special type of building, the cleanroom's internal environment cleanliness, temperature and humidity control, etc. have a vital impact on the stability of the production process and product quality.
In order to ensure the efficient operation and long-term stability of the cleanroom, effective operation management and timely maintenance are particularly important. This article will conduct an in-depth discussion on the operation management, maintenance and other aspects of the cleanroom, in order to provide useful reference for related companies.
Cleanroom operation management
Environmental monitoring: Monitoring the internal environment of the cleanroom is one of the core tasks of operation management. This includes regular testing of key parameters such as cleanliness, temperature and humidity, and pressure difference to ensure that they are within the set range. At the same time, attention should also be paid to the content of pollutants such as particles and microorganisms in the air, as well as the air flow, to ensure that the airflow organization meets the design requirements.
Equipment operation management: Ventilation, air conditioning, air purification and other equipment in the cleanroom are important equipment for maintaining environmental cleanliness. Operation management personnel should regularly inspect these equipment, check their operating status, energy consumption, maintenance records, etc., to ensure that the equipment is in good working condition. At the same time, necessary maintenance and replacement should be carried out according to the operation status and maintenance plan of the equipment.
Personnel management: Personnel management of clean workshops is equally important. Operation managers should formulate a strict personnel entry and exit management system to ensure that personnel entering the clean workshop meet the clean requirements, such as wearing clean clothes and clean gloves. At the same time, employees should be regularly trained in clean knowledge to improve their clean awareness and operating skills.
Record management: Operation managers should establish a complete record management system to record the operation status, environmental parameters, equipment operation status, etc. of the clean workshop in detail. These records can not only be used for daily operation management, but also provide important reference for troubleshooting, maintenance, etc.
Clean workshop maintenance
Preventive maintenance: Preventive maintenance is a key measure to ensure the long-term and stable operation of clean workshops. This includes regular cleaning, inspection, adjustment of ventilation and air conditioning, air purification and other equipment, as well as tightening and lubrication of pipes, valves and other accessories. Through preventive maintenance, potential problems can be discovered and solved in a timely manner to avoid the impact of equipment failure on the operation of clean workshops.
Troubleshooting and repair: When the equipment in the clean room fails, the maintenance personnel should quickly troubleshoot and repair it. During the troubleshooting process, the operation records, equipment maintenance records and other information should be fully utilized to analyze the cause of the failure and formulate a repair plan. During the repair process, the quality of the repair should be ensured to avoid secondary damage to the equipment. At the same time, the performance of the repaired equipment should be tested and verified to ensure that it resumes normal operation.
Spare parts management: Spare parts management is an important part of maintenance work. Enterprises should establish a complete spare parts management system and prepare necessary spare parts in advance according to the operation status and maintenance plan of the equipment. At the same time, spare parts should be regularly counted and updated to ensure the availability and reliability of spare parts.
Maintenance and maintenance record management: Maintenance and maintenance records are important data reflecting the operation status and maintenance quality of equipment. Enterprises should establish a complete maintenance and maintenance record management system to record the time, content, results, etc. of each maintenance and maintenance in detail. These records can not only be used for daily maintenance and repair work, but also provide important reference for equipment replacement and performance improvement.
Challenges and Countermeasures
In the process of operation management and maintenance of clean workshops, some challenges are often faced. For example, the continuous improvement of cleanliness requirements, the increase in equipment operation costs, and the insufficient skills of maintenance personnel. In order to meet these challenges, enterprises can take the following measures:
Introduce advanced technology: Improve the cleanliness and environmental stability of clean workshops by introducing advanced ventilation and air conditioning, air purification and other technologies. At the same time, it can also reduce the operation and maintenance costs of equipment.
Strengthen personnel training: Regularly conduct professional training for operation management personnel and maintenance personnel to improve their professional skills and knowledge level. Through training, the operation level and work efficiency of personnel can be improved to ensure the efficient operation and long-term stability of clean workshops.
Establish an incentive mechanism: By establishing an incentive mechanism, encourage operation management personnel and maintenance personnel to actively participate in work and improve work efficiency and quality. For example, a reward system and promotion mechanism can be established to stimulate employees' work enthusiasm and creativity.
Strengthen cooperation and communication: Strengthen cooperation and communication with other departments to jointly promote the operation management and maintenance of clean workshops. For example, a regular communication mechanism can be established with the production department, R&D department, etc. to jointly solve problems encountered in the operation management and maintenance process.
Conclusion
The operation management and maintenance of cleanrooms are important guarantees for ensuring the efficient operation and long-term stability of cleanrooms. By strengthening environmental monitoring, equipment management, personnel management, record management and other aspects, as well as taking measures to cope with challenges, the stable operation of cleanrooms and the steady improvement of product quality can be ensured.
At the same time, with the continuous advancement of science and technology and the continuous accumulation of experience, we should also continue to innovate and improve the operation management and maintenance methods to adapt to the new needs and challenges of cleanroom development.
Post time: Dec-10-2024