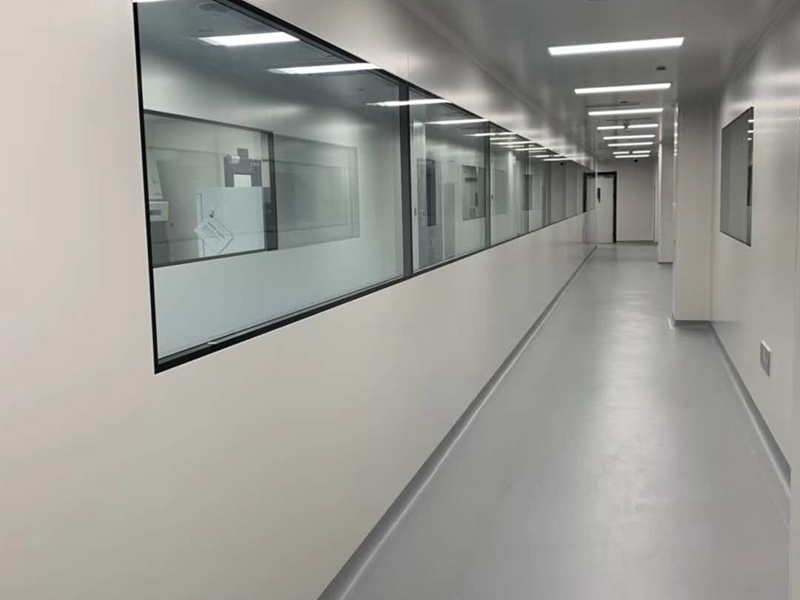
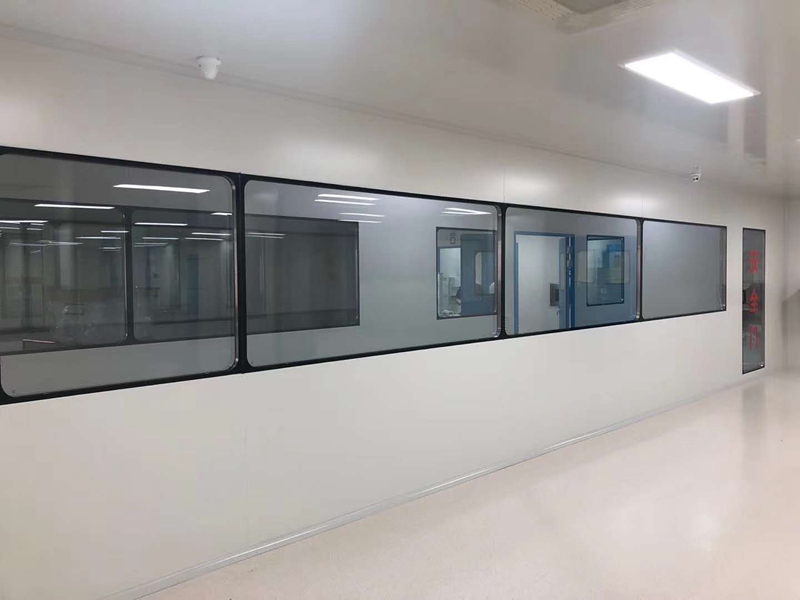
Cleanroom concept
Purification: refers to the process of removing pollutants in order to obtain the necessary cleanliness.
Air purification: the act of removing pollutants from the air to make the air clean.
Particles: solid and liquid substances with a general size of 0.001 to 1000μm.
Suspended particles: solid and liquid particles with a size range of 0.1 to 5μm in the air used for air cleanliness classification.
Static test: a test conducted when the cleanroom air conditioning system is in normal operation, the process equipment has been installed, and there are no production personnel in cleanroom.
Dynamic test: a test conducted when the cleanroom is in normal production.
Sterility: the absence of living organisms.
Sterilization: a method of achieving a sterile state. The difference between a cleanroom and an ordinary air-conditioned room. The cleanrooms and ordinary air-conditioned rooms are spaces where artificial methods are used to create and maintain an air environment that reaches a certain temperature, humidity, airflow velocity and air purification. The difference between the two is as follows:
Clean room ordinary air-conditioned room
Indoor air suspended particles must be controlled. Temperature, humidity, air flow speed and air volume must reach a certain ventilation frequency (unidirectional flow clean room 400-600 times/h, non-unidirectional clean room 15-60 times/h).
Generally, the temperature is reduced by 8-10 times/h. Ventilation is constant temperature room 10-15 times/h. In addition to temperature and humidity monitoring, cleanliness must be tested regularly. Temperature and humidity must be tested regularly. Air supply must pass through three-stage filtration, and the terminal must use hepa air filters. Use primary, medium and heat and moisture exchange equipment. Clean room must have a certain positive pressure ≥10Pa for the surrounding space. There is a positive pressure, but there is no calibration requirement. Personnel entering must change special shoes and sterile clothes and pass through air shower. Separate the flow of people and logistics.
Suspended particles: generally refers to solid and liquid particles suspended in the air, and its particle size range is about 0.1 to 5μm. Cleanliness: used to characterize the size and number of particles contained in air per unit volume of space, which is the standard for distinguishing the cleanliness of the space.
Airlock: A buffer room set up at the entrance and exit of a clean room to block polluted airflow and pressure difference control from the outside or adjacent rooms.
Air shower: A type of airlock that uses fans, filters, and control systems to blow air around people entering the room. It is one of the effective ways to reduce external pollution.
Clean work clothes: Clean clothes with low dust generation used to minimize the particles generated by workers.
Hepa air filter: An air filter with a capture efficiency of more than 99.9% for particles with a diameter greater than or equal to 0.3μm and an air flow resistance of less than 250Pa at rated air volume.
Ultra-hepa air filter: An air filter with a capture efficiency of more than 99.999% for particles with a diameter of 0.1 to 0.2μm and an air flow resistance of less than 280Pa at rated air volume.
Clean workshop: It is composed of central air conditioning and air purification system, and is also the heart of the purification system, working together to ensure the normality of various parameters. Temperature and humidity control: Clean workshop is the environmental requirement of GMP for pharmaceutical enterprises, and the cleanroom air conditioning (HVAC) system is the fundamental guarantee for achieving the purification area. Cleanroom central air conditioning system can be divided into two categories: DC air conditioning system: the outdoor air that has been treated and can meet the space requirements is sent into the room, and then all the air is discharged. It is also called a full exhaust system, which is used for workshops with special process requirements. The dust-producing area on the fourth floor of existing workshop belongs to this type, such as granulation drying room, tablet filling area, coating area, crushing and weighing area. Because the workshop produces a lot of dust, a DC air conditioning system is used. Recirculation air conditioning system: that is, the clean room air supply is a mixture of part of the treated outdoor fresh air and part of the return air from the clean room space. The outdoor fresh air volume is usually calculated as 30% of the total air volume in the clean room, and it should also meet the need to compensate for the exhaust air from the room. Recirculation is divided into primary return air and secondary return air. The difference between primary return air and secondary return air: In the air conditioning system of the clean room, primary return air refers to the indoor return air first mixed with fresh air, then treated by the surface cooler (or water spray chamber) to reach the machine dew point state, and then heated by the primary heater to reach the air supply state (for constant temperature and humidity system). The secondary return air method is that the primary return air is mixed with the fresh air and treated by the surface cooler (or water spray chamber) to reach the machine dew point state, and then mixed with the indoor return air once, and the indoor air supply state can be achieved by controlling the mixing ratio (mainly dehumidification system).
Positive pressure: Usually, clean rooms need to maintain positive pressure to prevent external pollution from flowing in, and it is conducive to the discharge of internal dust. The positive pressure value generally follows the following two designs: 1) The pressure difference between clean rooms of different levels and between clean areas and non-clean areas should not be less than 5Pa; 2) The pressure difference between indoor and outdoor clean workshops should not be less than 10Pa, generally 10~20Pa. (1Pa=1N/m2) According to the "Cleanroom Design Specification", the material selection of the maintenance structure of the cleanroom should meet the requirements of thermal insulation, heat insulation, fire prevention, moisture resistance, and less dust. In addition, temperature and humidity requirements, pressure difference control, air flow and air supply volume, entry and exit of people, and air purification treatment are organized and cooperated to form a cleanroom system.
- Temperature and humidity requirements
The temperature and relative humidity of the cleanroom should be consistent with the production requirements of the product, and the production environment of the product and the comfort of the operator should be guaranteed. When there are no special requirements for product production, the temperature range of the cleanroom can be controlled at 18-26℃ and the relative humidity can be controlled at 45-65%. Considering the strict control of microbial contamination in the core area of aseptic operation, there are special requirements for the clothing of operators in this area. Therefore, the temperature and relative humidity of the clean area can be determined according to the special requirements of the process and product.
- Pressure difference control
To avoid the cleanliness of the clean room from being polluted by the adjacent room, the airflow along the gaps of the building (door gaps, wall penetrations, ducts, etc.) in the specified direction can reduce the circulation of harmful particles. The method to control the direction of the airflow is to control the pressure of the adjacent space. GMP requires a measurable pressure difference (DP) to be maintained between the clean room and the adjacent space with lower cleanliness. The DP value between different air levels in China's GMP is stipulated to be no less than 10Pa, and the positive or negative pressure difference should be maintained according to the process requirements.
- Airflow pattern and air supply volume reasonable airflow organization is one of the important guarantees to prevent pollution and cross-contamination in clean area. Reasonable airflow organization is to make the clean room air sent in quickly and evenly distributed or diffused to the entire clean area, minimize eddy currents and dead corners, dilute the dust and bacteria emitted by indoor pollution, and quickly and effectively discharge them, reduce the probability of dust and bacteria contaminating the product, and maintain the required cleanliness in the room. Since clean technology controls the concentration of suspended particles in the atmosphere, and the air volume delivered to the clean room is much larger than that required by general air-conditioned rooms, its airflow organization form is significantly different from them. The airflow flow pattern is mainly divided into three categories:
- Unidirectional flow: airflow with parallel streamlines in a single direction and consistent wind speed on the cross section; (There are two types: vertical unidirectional flow and horizontal unidirectional flow.)
- Non-unidirectional flow: refers to airflow that does not meet the definition of unidirectional flow.
3. Mixed flow: airflow composed of unidirectional flow and non-unidirectional flow. Generally, unidirectional flow flows smoothly from the indoor air supply side to its corresponding return air side, and the cleanliness can reach class 100. The cleanliness of non-unidirectional clean rooms is between class 1,000 and class 100,000, and the cleanliness of mixed flow clean rooms can reach class 100 in some areas. In a horizontal flow system, the airflow flows from one wall to another. In a vertical flow system, the airflow flows from the ceiling to the ground. The ventilation condition of a clean room can usually be expressed in a more intuitive way by the "air change frequency": "air change" is the air volume entering the space per hour divided by the volume of the space. Due to the different clean air supply volumes sent into the clean room, the cleanliness of the room is also different. According to theoretical calculations and practical experience, the general experience of ventilation times is as follows, as a preliminary estimate of the clean room air supply volume: 1) For class 100,000, the ventilation times are generally more than 15 times/hour; 2) For class 10,000, the ventilation times are generally more than 25 times/hour; 3) For class 1000, the ventilation times are generally more than 50 times/hour; 4) For class 100, the air supply volume is calculated based on the air supply cross-sectional wind speed of 0.2-0.45m/s. Reasonable air volume design is an important part of ensuring the cleanliness of the clean area. Although increasing the number of room ventilation is beneficial to ensuring cleanliness, excessive air volume will cause energy waste. Air cleanliness level maximum allowable number of dust particles (static) maximum allowable number of microorganisms (static) ventilation frequency (per hour)
4. Entry and exit of people and objects
For clean room interlocks, they are generally set at the entrance and exit of the clean room to block the external polluted airflow and control the pressure difference. The buffer room is set up. These interlocking device rooms control the entry and exit space through several doors, and also provide places for wearing/taking off clean clothes, disinfection, purification and other operations. Common electronic interlocks and air locks.
Pass box: The entry and exit of materials in clean room include pass box, etc. These components play a buffering role in the transfer of materials between the clean area and the non-clean area. Their two doors cannot be opened at the same time, which ensures that the outside air cannot enter and exit the workshop when the items are delivered. In addition, the pass box equipped with ultraviolet lamp device can not only maintain the positive pressure in the room stable, prevent pollution, meet GMP requirements, but also play a role in sterilization and disinfection.
Air shower: The air shower room is the passage for goods to enter and exit the clean room and also plays the role of airlock room closed clean room. In order to reduce the large amount of dust particles brought by the goods in and out, the clean air flow filtered by the hepa filter is sprayed from all directions by the rotatable nozzle to the goods, effectively and quickly remove the dust particles. If there is an air shower, it must be blown and showered according to regulations before entering the dust-free clean workshop. At the same time, strictly follow the specifications and use requirements of the air shower.
- Air purification treatment and its characteristics
Air purification technology is a comprehensive technology to create a clean air environment and ensure and improve product quality. It is mainly to filter out the particles in the air to obtain clean air, and then flow in the same direction at a uniform speed parallel or vertically, and wash away the air with particles around it, so as to achieve the purpose of air purification. The air conditioning system of the clean room must be a purified air conditioning system with three-stage filtration treatments: primary filter, medium filter and hepa filter. Ensure that the air sent into the room is clean air and can dilute the polluted air in the room. The primary filter is mainly suitable for primary filtration of air conditioning and ventilation systems and return air filtration in clean rooms. The filter is composed of artificial fibers and galvanized iron. It can effectively intercept dust particles without forming too much resistance to airflow. The randomly interwoven fibers form countless barriers to particles, and the wide space between the fibers allows airflow to pass smoothly to protect the next level of filters in the system and the system itself. There are two situations for the flow of sterile indoor air: one is laminar (that is, all suspended particles in the room are kept in the laminar layer); the other is non-laminar (that is, the flow of indoor air is turbulent). In most clean rooms, the flow of indoor air is non-laminar (turbulent), which can not only quickly mix the suspended particles entrained in the air, but also make the stationary particles in the room fly again, and some air can also stagnate.
6. Fire prevention and evacuation of clean workshops
1) The fire resistance level of clean workshops shall not be lower than level 2;
2) The fire hazard of production workshops in clean workshops shall be classified and implemented in accordance with the current national standard "Code for Fire Prevention of Building Design".
3) The ceiling and wall panels of the clean room shall be non-combustible, and organic composite materials shall not be used. The fire resistance limit of the ceiling shall not be less than 0.4h, and the fire resistance limit of the ceiling of the evacuation corridor shall not be less than 1.0h.
4) In a comprehensive factory building within a fire zone, non-combustible body partition measures shall be set between the clean production and general production areas. The fire resistance limit of the partition wall and its corresponding ceiling shall not be less than 1h. Fireproof or fire-resistant materials shall be used to tightly fill the pipes passing through the wall or ceiling;
5) Safety exits shall be dispersed, and there should be no tortuous routes from the production site to the safety exit, and obvious evacuation signs shall be set.
6) The safety evacuation door connecting the clean area with the non-clean area and the clean area outdoors shall be opened in the evacuation direction. The safe evacuation door should not be a suspended door, special door, side sliding door or electric automatic door. The exterior wall of the clean workshop and the clean area on the same floor should be equipped with doors and windows for firefighters to enter the clean area of the workshop, and a special fire exit should be set at the appropriate part of the exterior wall.
GMP workshop definition: GMP is the abbreviation of Good Manufacture Practice. Its main content is to put forward mandatory requirements for the rationality of the enterprise's production process, the applicability of production equipment, and the accuracy and standardization of production operations. GMP certification refers to the process in which the government and relevant departments organize inspections of all aspects of the enterprise, such as personnel, training, plant facilities, production environment, sanitary conditions, material management, production management, quality management, and sales management, to assess whether they meet the regulatory requirements. GMP requires that product manufacturers should have good production equipment, reasonable production processes, perfect quality management and strict testing systems to ensure that the quality of the final product meets the requirements of regulations. The production of some products must be carried out in GMP certified workshops. Implementing GMP, improving product quality, and enhancing service concepts are the foundation and source of development of small and medium-sized enterprises under market economy conditions. Clean room pollution and its control: Definition of pollution: Pollution refers to all unnecessary substances. Whether it is material or energy, as long as it is not a component of the product, it is not necessary to exist and affect the performance of the product. There are four basic sources of pollution: 1. Facilities (ceiling, floor, wall); 2. Tools, equipment; 3. Personnel; 4. Products. Note: Micro-pollution can be measured in microns, that is: 1000μm=1mm. Usually we can only see dust particles with a particle size greater than 50μm, and dust particles less than 50μm can only be seen with a microscope. Clean room microbial contamination mainly comes from two aspects: human body contamination and workshop tool system contamination. Under normal physiological conditions, the human body will always shed cell scales, most of which carry bacteria. Since the air resuspends a large number of dust particles, it provides carriers and living conditions for bacteria, so the atmosphere is the main source of bacteria. People are the biggest source of pollution. When people talk and move, they release a large number of dust particles, which adhere to the surface of the product and contaminate the product. Although the personnel working in clean room wear clean clothes, clean clothes cannot completely prevent the spread of particles. Many of the larger particles will soon settle on the surface of the object due to gravity, and other smaller particles will fall on the surface of the object with the movement of the air flow. Only when the small particles reach a certain concentration and aggregate together can they be seen by the naked eye. In order to reduce the pollution of clean rooms by staff, staff must strictly follow the regulations when entering and exiting. The first step before entering the clean room is to take off your coat in the first shift room, put on the standard slippers, and then enter the second shift room to change shoes. Before entering the second shift, wash and dry your hands in the buffer room. Dry your hands on the front and back of your hands until your hands are not damp. After entering the second shift room, change the first shift slippers, put on sterile work clothes, and put on the second shift purification shoes. There are three key points when wearing clean work clothes: A. Dress neatly and do not expose your hair; B. The mask should cover the nose; C. Clean the dust from the clean work clothes before entering the clean workshop. In production management, in addition to some objective factors, there are still many staff members who do not enter the clean area as required and the materials are not strictly handled. Therefore, product manufacturers must strictly require production operators and cultivate the cleanliness awareness of production personnel. Human pollution - bacteria:
1. Pollution generated by people: (1) Skin: Humans usually shed their skin completely every four days, and humans shed about 1,000 pieces of skin per minute (average size is 30*60*3 microns) (2) Hair: Human hair (diameter is about 50~100 microns) is constantly falling off. (3) Saliva: contains sodium, enzymes, salt, potassium, chloride and food particles. (4) Everyday clothing: particles, fibers, silica, cellulose, various chemicals and bacteria. (5) Humans will generate 10,000 particles larger than 0.3 microns per minute when they are still or sitting.
2. Analysis of foreign test data shows that: (1) In a clean room, when workers wear sterile clothing: the amount of bacteria emitted when they are still is generally 10~300/min. The amount of bacteria emitted when the human body is generally active is 150~1000/min. The amount of bacteria emitted when a person walks fast is 900~2500/min.person. (2) A cough is generally 70~700/min.person. (3) A sneeze is generally 4000~62000/min.person. (4) The amount of bacteria emitted when wearing ordinary clothes is 3300~62000/min.person. (5) The amount of bacteria emitted without a mask: the amount of bacteria emitted with a mask is 1:7~1:14.
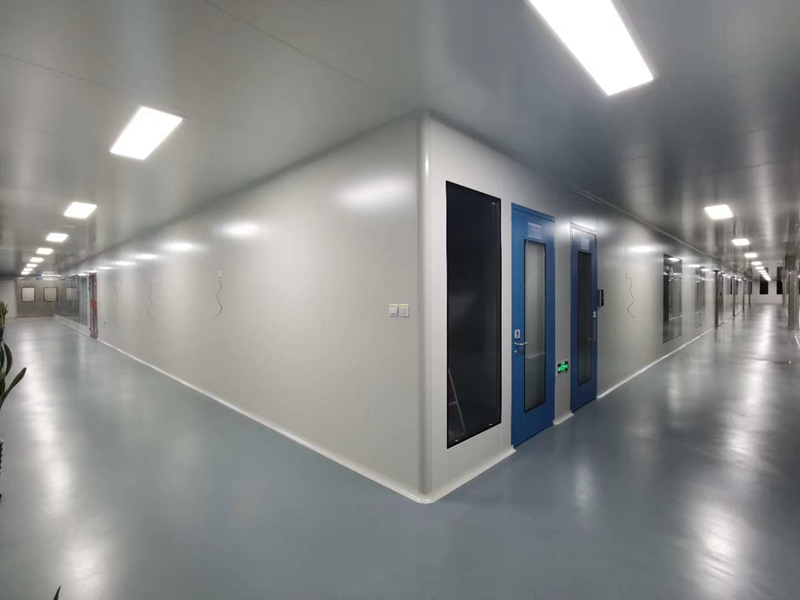

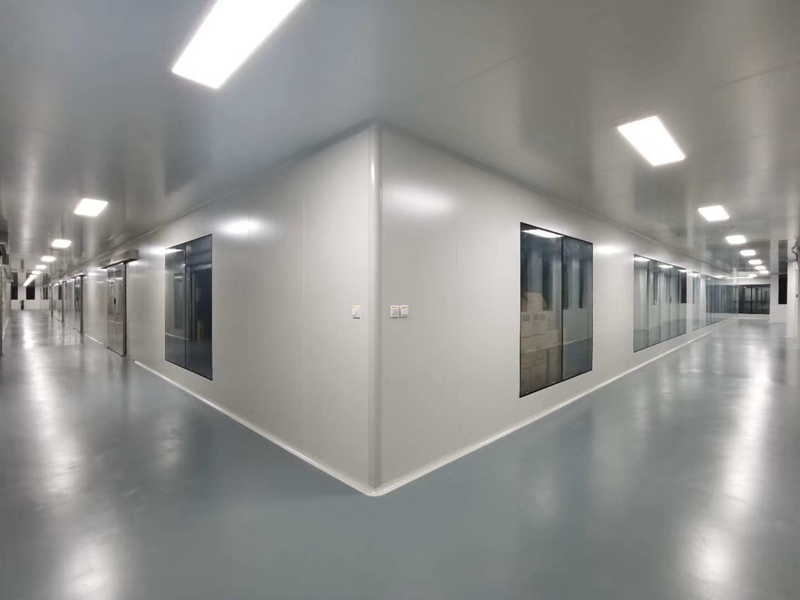
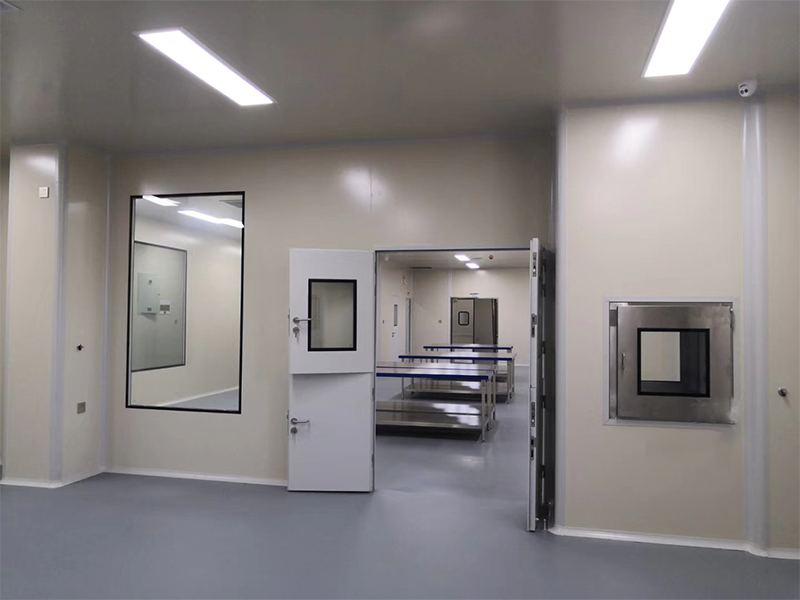
Post time: Mar-05-2025