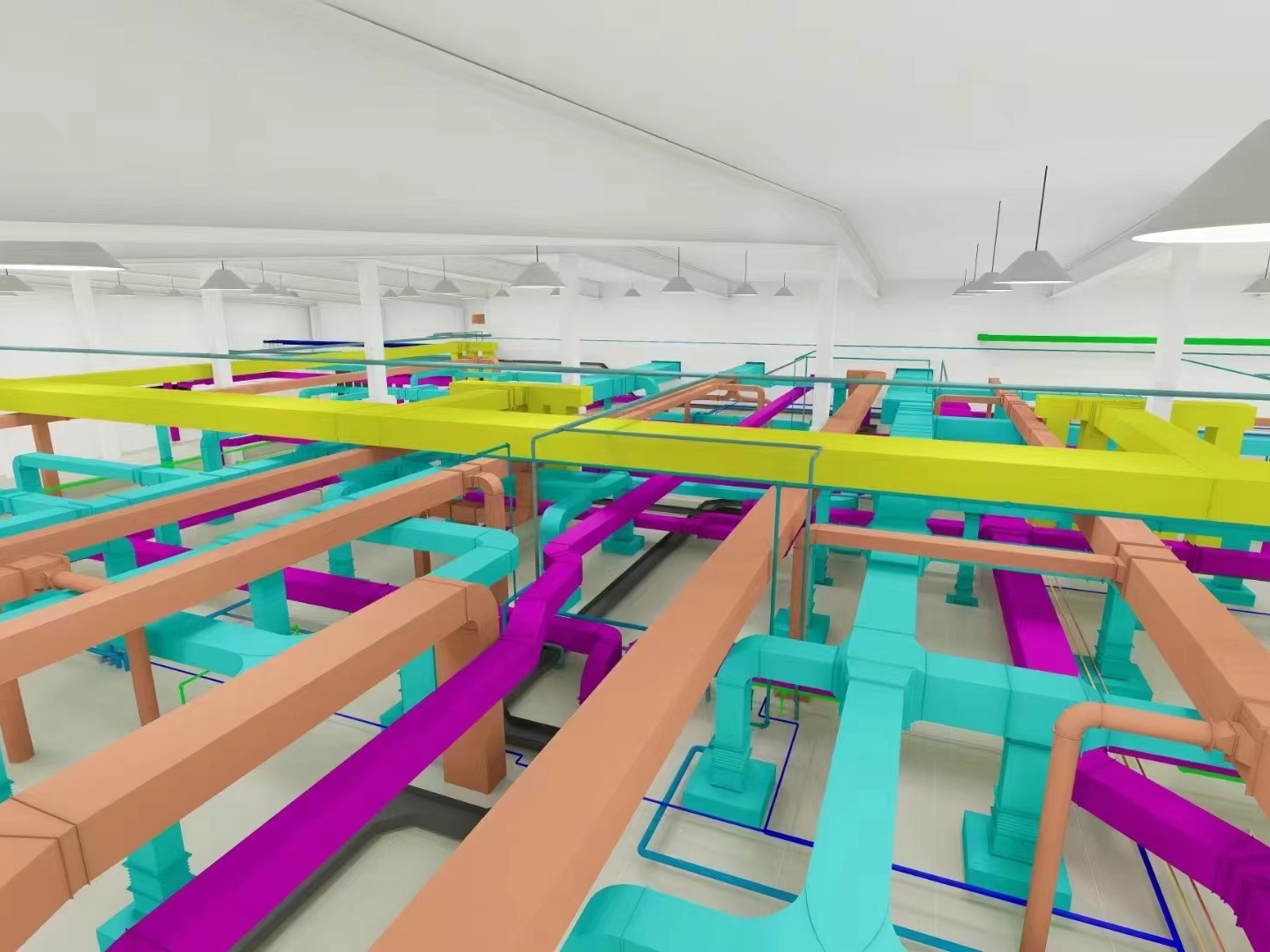
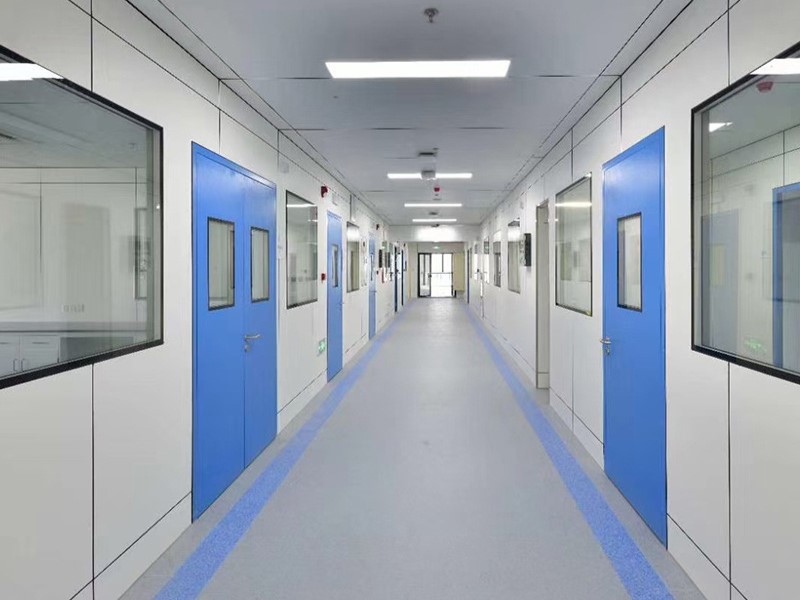
When designing cleanroom air conditioning solutions, the main goal is to ensure that the required temperature, humidity, air velocity, pressure and cleanliness parameters are maintained in clean room. The following is a detailed cleanroom air conditioning solutions.
1. Basic composition
Heating or cooling, humidification or dehumidification and purification equipment: This is the core part of the air conditioning system, which is used to perform necessary air treatment to meet the requirements of the cleanroom.
Air conveying equipment and its pipelines: send the treated air into each cleanroom and ensure the circulation of the air.
Heat source, cold source and its pipeline system: provide the necessary cooling and heat for the system.
2. System classification and selection
Centralized clean air conditioning system: suitable for occasions with continuous process production, large clean room area and concentrated location. The system centrally treats the air in machine room and then sends it to each cleanroom. It has the following characteristics: the equipment is concentrated in machine room, which is convenient for noise and vibration treatment. One system controls multiple cleanrooms, requiring each cleanroom to have a high simultaneous use coefficient. According to needs, you can choose a direct current, closed or hybrid system.
Decentralized clean air conditioning system: suitable for occasions with a single production process and decentralized cleanrooms. Each clean room is equipped with a separate purification device or purification air conditioning device.
Semi-centralized clean air conditioning system: combines the characteristics of centralized and decentralized, with both centralized purification air conditioning rooms and air handling equipment dispersed in each cleanroom.
3. Air conditioning and purification
Air conditioning: According to the requirements of the cleanroom, the air is treated by heating, cooling, humidification or dehumidification equipment to ensure the stability of temperature and humidity.
Air purification: Through three-level filtration of coarse, medium and high efficiency, dust and other pollutants in air are removed to ensure cleanliness. Primary filter: It is recommended to replace it regularly every 3 months. Medium filter: It is recommended to replace it regularly every 3 months. Hepa filter: It is recommended to replace it regularly every two years.
4. Airflow organization design
Upward delivery and downward return: A common airflow organization form, suitable for most cleanrooms. Side-upward delivery and side-down return: Suitable for cleanrooms with specific requirements. Ensure sufficient purified air supply to meet the requirements of the cleanroom.
5. Maintenance and troubleshooting
Regular maintenance: including cleaning and replacing filters, checking and controlling the differential pressure gauge on the electrical box, etc.
Troubleshooting: For problems such as differential pressure control and substandard air volume, timely adjustments and troubleshooting should be made.
6. Summary
The design of the air conditioning solutions for cleanroom project needs to comprehensively consider the specific requirements of the cleanroom, production process, environmental conditions and other factors. Through reasonable system selection, air conditioning and purification, airflow organization design, and regular maintenance and troubleshooting, it can ensure that the required temperature, humidity, air velocity, pressure, cleanliness and other parameters are maintained in cleanroom to meet the needs of production and scientific research.
Post time: Jul-24-2024