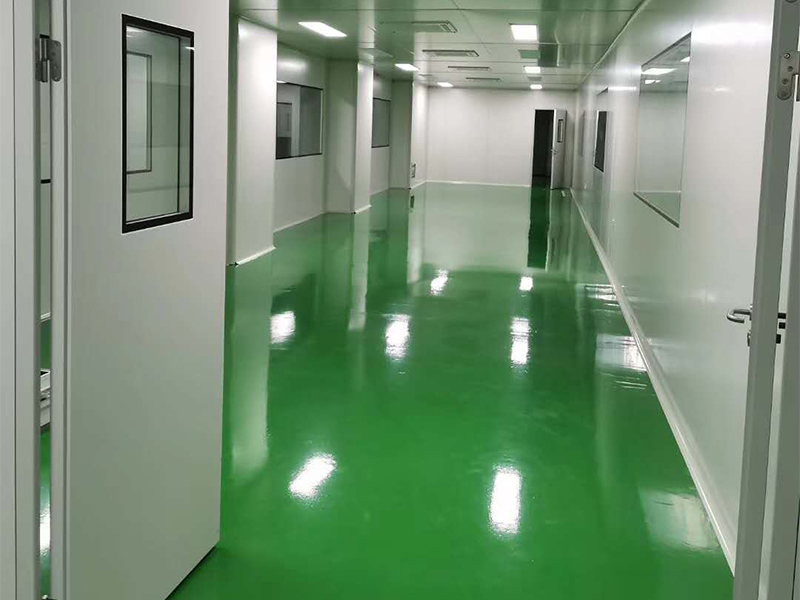
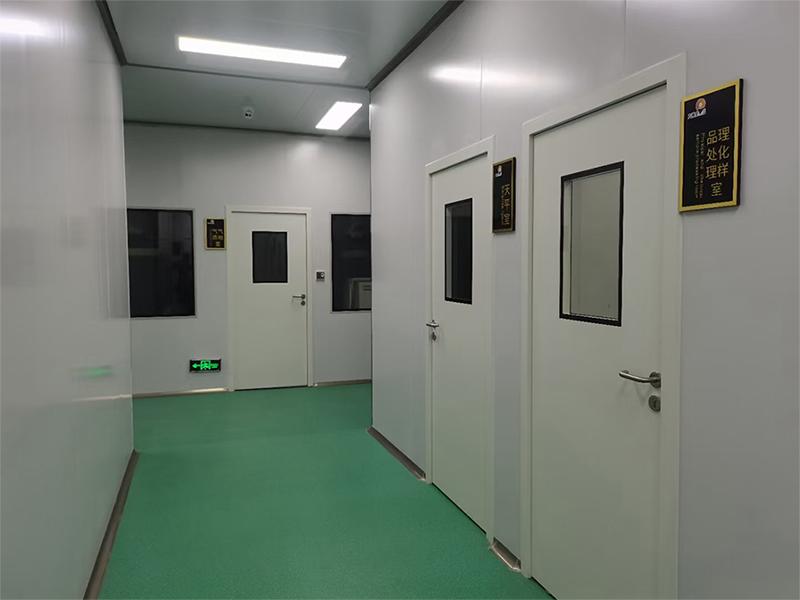
- Clean room related concepts
A clean area is a limited space with controlled concentration of suspended particles in the air. Its construction and use should reduce the introduction, generation and retention of particles in the space. Other relevant parameters in the space such as temperature, humidity and pressure are required to be controlled. Air cleanliness refers to the degree of dust particles in the air in a clean environment. The higher the dust concentration, the lower the cleanliness, and the lower the dust concentration, the higher the cleanliness. The specific level of air cleanliness is distinguished by the air cleanliness level, and this level is expressed by the counted dust concentration of the air during the operating time. Suspended particles refer to solid and liquid particles with a size range of 0.15μm in the air used for air cleanliness classification.
- Classification of clean rooms
(1). According to the cleanliness level, it is divided into level 1, level 2, level 3, level 4, level 5, level 6, level 7, level 8 and level 9. Level 9 is the lowest level.
(2). According to the airflow organization classification, clean rooms can be divided into three categories: unidirectional flow, laminar flow and clean room. Airflow with parallel streamlines in a single direction and uniform wind speed on the cross section. Among them, the unidirectional flow perpendicular to the horizontal plane is vertical unidirectional flow, and the unidirectional flow parallel to the horizontal plane is horizontal unidirectional flow. Turbulent non-unidirectional flow clean room Any clean room with airflow that does not meet the definition of unidirectional flow. Mixed flow clean room: A clean room with airflow that combines unidirectional flow and non-unidirectional flow.
(3). Clean rooms can be divided into industrial clean rooms and biological clean rooms according to the classification of suspended particles in the air that need to be controlled. The main control parameters of industrial clean rooms are temperature, humidity, air velocity, airflow organization, and cleanliness. The difference between biological clean rooms and industrial clean rooms is that the control parameters increase the concentration of bacteria in the control room.
(4). The detection status of clean rooms can be divided into three categories.
①Empty clean room with complete facilities. All pipelines are connected and running, but there are no production equipment, materials and production personnel.
②Static clean room with complete facilities. The production equipment has been installed in the clean room and tested in the manner agreed upon by the owner and supplier, but there are no production personnel on site.
③Dynamic facilities are in a state of operation in a prescribed manner and there are prescribed personnel on site to work in a prescribed manner.
- The difference between clean room air conditioning and general air conditioning
Clean room air conditioning is a type of air conditioning project. It not only has certain requirements for the temperature, humidity and wind speed of indoor air, but also has higher requirements for the number of dust particles and bacterial concentration in the air. Therefore, it not only has special requirements for the design and construction of ventilation projects, but also has special requirements and corresponding technical measures for the design and construction of building layout, material selection, construction process, building practices, water, heating and electricity, and the process itself. Its cost is also increased accordingly. Main parameters
General air conditioning focuses on the supply of temperature, humidity, and fresh air volume, while clean room air conditioning focuses on controlling the dust content, wind speed, and ventilation frequency of indoor air. In rooms with temperature and humidity requirements, they are also the main control parameters. The bacterial content is also one of the main control parameters for biological clean rooms. Filtration means General air conditioning has only primary filtration, and the higher requirement is medium filtration. Clean room air conditioning requires three-level filtration, that is, primary, medium, and hepa three-level filtration or coarse, medium, and sub-hepa three-level filtration. In addition to the three-stage filtration of the air supply system of the biological clean room, in order to eliminate the special odor of animals and avoid pollution to the environment, the exhaust system is also equipped with secondary hepa filtration or toxic adsorption filtration according to different situations.
Indoor pressure requirements
General air conditioning has no special requirements for indoor pressure, while clean air conditioning has different requirements for positive pressure values of different clean areas in order to avoid the infiltration of external polluted air or the mutual influence of different substances in different production workshops. There are also requirements for negative pressure control in negative pressure clean rooms.
Materials and equipment
Cleanroom air conditioning system has special requirements for the selection of materials and equipment, processing technology, processing and installation environment, and storage environment of equipment components in order to avoid external pollution. This is also not available in general air conditioning systems. Airtight requirements Although general air conditioning systems have requirements for the air tightness and air permeability of the system. However, the requirements of clean air conditioning systems are much higher than those of general air conditioning systems. Its detection methods and standards for each process have strict measures and detection requirements.
Other requirements
General air-conditioned rooms have requirements for building layout, thermal engineering, etc., but they do not pay much attention to material selection and airtightness requirements. In addition to the general requirements for the appearance of buildings, the evaluation of building quality by clean air conditioning focuses on dust prevention, dusting prevention, and leakage prevention. The construction process arrangement and overlap requirements are very strict to avoid rework and cracks that may cause leakage. It also has strict requirements for the coordination and requirements of other types of work, mainly focusing on preventing leakage, preventing external polluted air from infiltrating the clean room, and preventing dust accumulation from polluting the clean room.
4. Clean room completion acceptance
After the completion and commissioning of the clean room, performance measurement and acceptance are required; when the system is overhauled or updated, a comprehensive measurement must also be carried out, and the general situation of the clean room must be fully understood before the measurement. The main contents include the plane, section and system diagrams of the purification air conditioning system and process layout, requirements for air environment conditions, cleanliness level, temperature, humidity, wind speed, etc., air treatment plan, return air, exhaust volume and airflow organization, purification plan for people and objects, use of the clean room, pollution in factory area and its surroundings, etc.
(1). The appearance inspection of the completion acceptance of the clean room shall meet the following requirements.
①The installation of various pipelines, automatic fire extinguishing devices and purification air conditioning equipment air conditioners, fans, purification air conditioning units, hepa air filters and air shower rooms shall be correct, firm and tight, and their deviations shall comply with relevant regulations.
②The connection between hepa and medium air filters and the support frame and the connection between the air duct and the equipment shall be reliably sealed.
③Various adjustment devices shall be tight, flexible to adjust and easy to operate.
④There shall be no dust on the purification air conditioning box, static pressure box, air duct system and supply and return air outlets.
⑤The inner wall, ceiling surface and floor of the clean room shall be smooth, flat, uniform in color, dust-free and static electricity-free.
⑥The sealing treatment of the supply and return air outlets and various terminal devices, various pipelines, lighting and power line piping and process equipment when passing through the clean room shall be strict and reliable.
⑦All kinds of distribution boards, cabinets in clean room and electrical pipelines and pipe openings entering the clean room shall be reliably sealed.
⑧All kinds of painting and insulation work should comply with relevant regulations.
(2). Commissioning work for completion acceptance of clean room manufacturing
①The single-machine trial operation of all equipment with trial operation requirements should comply with the relevant provisions of the equipment technical documents. The common requirements of mechanical equipment should also comply with relevant national regulations and relevant industry standards for the construction and installation of mechanical equipment. Usually, the equipment that needs to be tested in a clean room includes air conditioning units, air supply and pressure fan boxes, exhaust equipment, purification workbenches, electrostatic self-purifiers, clean drying boxes, clean storage cabinets and other local purification equipment, as well as air shower rooms, residual pressure valves, vacuum dust cleaning equipment, etc.
②After the single-machine trial operation is qualified, the air volume and air pressure regulating devices of the air supply system, return air system, and exhaust system need to be set and adjusted so that the air volume distribution of each system meets the design requirements. The purpose of this stage of testing is mainly to serve the adjustment and balance of the air conditioning purification system, which often needs to be repeated many times. This test is mainly responsible for the contractor, and the maintenance management personnel of the builder should follow up to familiarize themselves with the system. On this basis, the system joint trial operation time including cold and heat sources is generally not less than 8 hours. It is required that the linkage and coordination of various equipment components in the system, including the purification air conditioning system, automatic adjustment device, etc., should operate correctly without abnormal phenomena.
5. Process flow of clean room detection
All instruments and equipment used in the measurement must be identified, calibrated or calibrated according to regulations. Before the measurement, the system, clean room, machine room, etc. must be thoroughly cleaned; after cleaning and system adjustment, it must be continuously operated for a period of time and then leak detection and other items are measured.
(1) The procedure for clean room measurement is as follows:
1. Fan air blowing;
2. Indoor cleaning;
3. Adjust air volume;
4. Install medium efficiency filter;
5. Install high efficiency filter;
6. System operation;
7. High efficiency filter leak detection;
8. Adjust air volume;
9. Adjust indoor static pressure difference;
10. Adjust temperature and humidity;
11. Determination of average velocity and velocity unevenness of the cross section of the single-phase flow clean room;
12. Indoor cleanliness measurement;
13. Determination of indoor floating bacteria and settling bacteria;
14. Work and adjustment related to production equipment.
(2) The inspection basis includes specifications, drawings, design documents and technical data of equipment, which are divided into the following two categories.
1. Design documents, documents proving design changes and relevant agreements, and completion drawings.
2. Technical data of equipment.
3. "Cleanroom Design Specifications", "Ventilation and Air Conditioning Engineering Construction Quality Acceptance Specifications" for construction and installation
6. Inspection indicators
Air volume or air velocity, indoor static pressure difference, air cleanliness level, ventilation times, indoor floating bacteria and settling bacteria, temperature and relative humidity, average speed, speed unevenness, noise, airflow pattern, self-cleaning time, pollution leakage, illumination (lighting), formaldehyde, and bacterial concentration.
(1). Clean operating room of hospital: wind speed, ventilation times, static pressure difference, cleanliness level, temperature and humidity, noise, illumination, and bacterial concentration.
(2). Cleanrooms in pharmaceutical industry: air cleanliness level, static pressure difference, wind speed or air volume, airflow pattern, temperature, relative humidity, illumination, noise, self-cleaning time, installed filter leakage, floating bacteria, and settling bacteria.
(3). Cleanrooms in electronics industry: air cleanliness level, static pressure difference, wind speed or air volume, airflow pattern, temperature, relative humidity, illumination, noise, and self-cleaning time.
(4). Cleanrooms in food industry: directional airflow, static pressure difference, cleanliness, air floating bacteria, air settling bacteria, noise, illumination, temperature, relative humidity, self-cleaning time, formaldehyde, air velocity in the cross section of the Class I work area, air velocity at the opening of the development, and fresh air volume.
Post time: Mar-11-2025