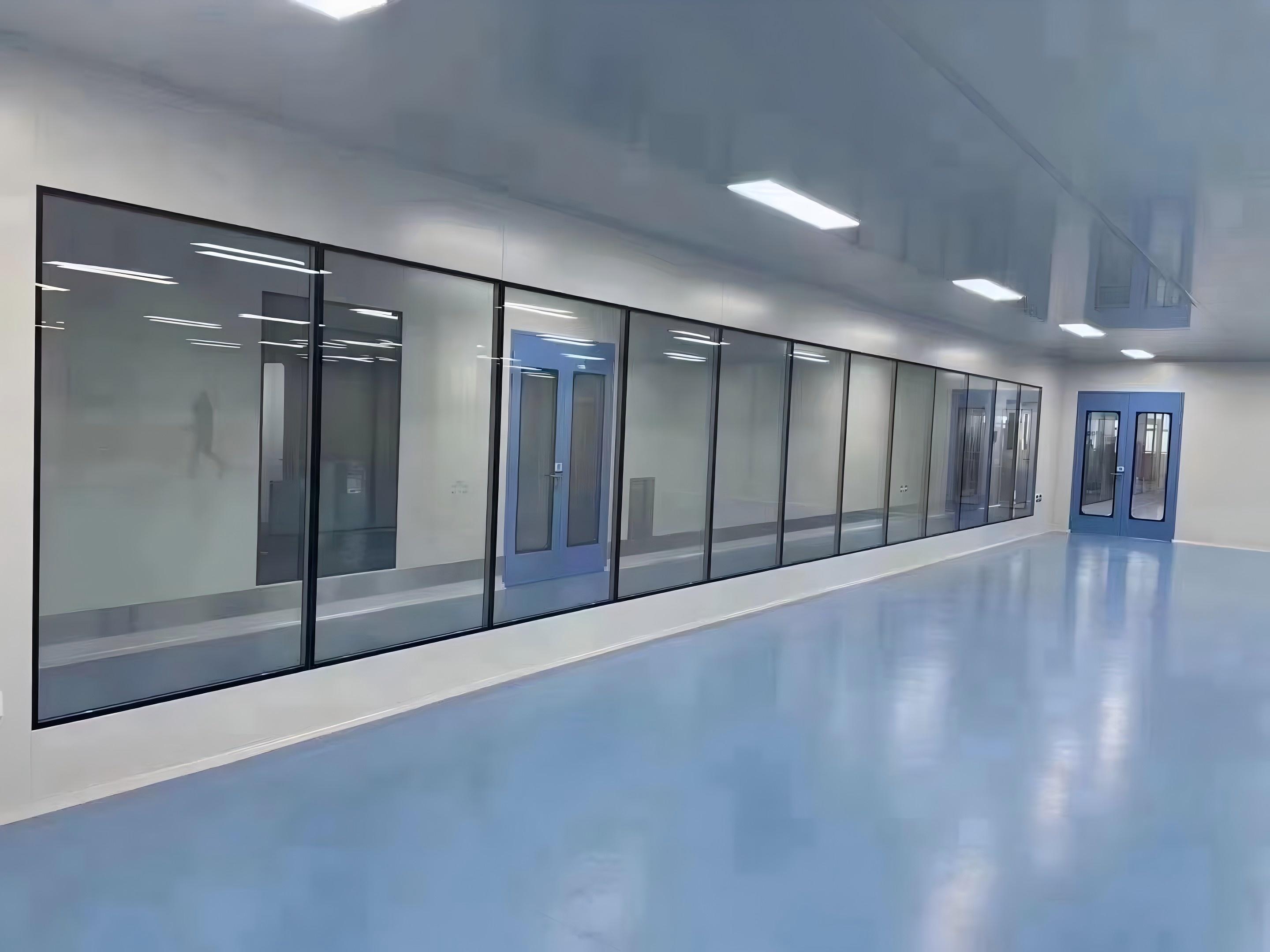
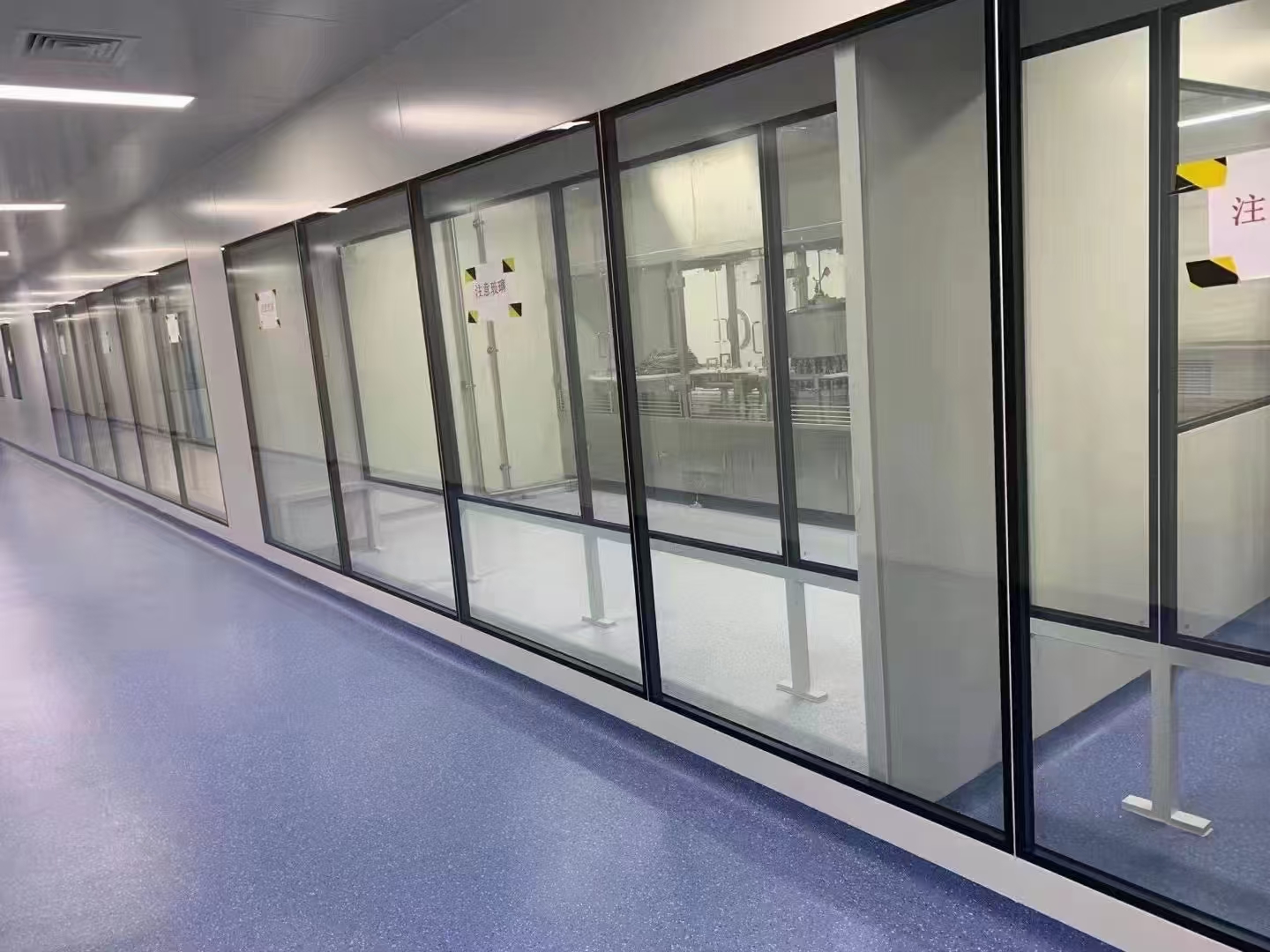
1. Dust particles removal in dust free clean room
The main function of clean room is to control the cleanliness, temperature and humidity of the atmosphere that products (such as silicon chips, etc.) are exposed to, so that the products can be produced and manufactured in a good environment space. We call this space as clean room. According to international practice, the cleanliness level is mainly determined by the number of particles per cubic meter of air with a diameter greater than the classification standard. In other words, the so-called dust-free is not 100% dust-free, but controlled in a very small unit. Of course, the particles that meet the dust standard in this standard are already very small compared to the common dust we see, but for optical structures, even a little dust will have a very large negative impact, so dust-free is an inevitable requirement in the production of optical structure products.
Controlling the number of dust particles with a particle size greater than or equal to 0.5 microns per cubic meter to less than 3520/cubic meter will reach class A of the international dust-free standard. The dust-free standard used in chip-level production and processing has higher requirements for dust than class A, and such a high standard is mainly used in the production of some higher-level chips. The number of dust particles is strictly controlled at 35,200 per cubic meter, which is commonly known as class B in clean room industry.
2. Three kinds of clean room states
Empty clean room: a clean room facility that has been built and can be put into use. It has all relevant services and functions. However, there is no equipment operated by operators in the facility.
Static clean room: a clean room facility with complete functions, proper settings and installation, which can be used according to the settings or is in use, but there are no operators in the facility.
Dynamic clean room: a clean room in normal use, with complete service functions, equipment and personnel; if necessary, normal work can be carried out.
3. Control items
(1). Can remove dust particles floating in the air.
(2). Can prevent the generation of dust particles.
(3). Control of temperature and humidity.
(4). Pressure regulation.
(5). Elimination of harmful gases.
(6). Air tightness of structures and compartments.
(7). Prevention of static electricity.
(8). Prevention of electromagnetic interference.
(9). Consideration of safety factors.
(10). Consideration of energy saving.
4. Classification
Turbulent flow type
Air enters the clean room from the air conditioning box through the air duct and the air filter (HEPA) in clean room, and is returned from the partition wall panels or elevated floors on both sides of the clean room. The airflow does not move in a linear manner but presents an irregular turbulent or eddy state. This type is suitable for class 1,000-100,000 clean room.
Definition: A clean room where the airflow flows at an uneven speed and is not parallel, accompanied by backflow or eddy current.
Principle: Turbulent clean rooms rely on the air supply airflow to continuously dilute the indoor air and gradually dilute the polluted air to achieve cleanliness (turbulent clean rooms are generally designed at cleanliness levels above 1,000 to 300,000).
Features: Turbulent clean rooms rely on multiple ventilation to achieve cleanliness and cleanliness levels. The number of ventilation changes determines the purification level in the definition (the more ventilation changes, the higher the cleanliness level)
(1) Self-purification time: refers to the time when the clean room starts to supply air to the clean room according to the designed ventilation number and the dust concentration in the room reaches the designed cleanliness level class 1,000 is expected to be no more than 20 minutes (15 minutes can be used for calculation) class 10,000 is expected to be no more than 30 minutes (25 minutes can be used for calculation) class 100,000 is expected to be no more than 40 minutes (30 minutes can be used for calculation)
(2) Ventilation frequency (designed according to the above self-cleaning time requirements) class 1,000: 43.5-55.3 times/hour (standard: 50 times/hour) class 10,000: 23.8-28.6 times/hour (standard: 25 times/hour) class 100,000: 14.4-19.2 times/hour (standard: 15 times/hour)
Advantages: simple structure, low system construction cost, easy to expand clean room, in some special purpose places, dust-free clean bench can be used to improve the clean room grade.
Disadvantages: dust particles caused by turbulence float in indoor space and are difficult to be discharged, which can easily contaminate process products. In addition, if the system is stopped and then activated, it often takes a long time to achieve the required cleanliness.
Laminar flow
Laminar flow air moves in a uniform straight line. Air enters the room through a filter with a 100% coverage rate and is returned through the elevated floor or the partition boards on both sides. This type is suitable for use in clean room environments with higher cleanroom grades, generally class 1~100. There are two types:
(1) Horizontal laminar flow: Horizontal air is blown out from the filter in a single direction and returned by the return air system on the opposite wall. Dust is discharged outdoors with air direction. Generally, pollution is more serious on the downstream side.
Advantages: Simple structure, can become stable in a short time after operation.
Disadvantages: Construction cost is higher than turbulent flow, and indoor space is not easy to expand.
(2) Vertical laminar flow: The room ceiling is completely covered with ULPA filters, and air is blown from top to bottom, which can achieve a higher cleanliness. Dust generated during the process or by the staff can be quickly discharged outdoors without affecting other work areas.
Advantages: Easy to manage, stable state can be achieved within a short time after the operation starts, and not easily affected by the operating state or operators.
Disadvantages: High construction cost, difficult to flexibly use space, ceiling hangers occupy a lot of space, and troublesome to repair and replace filters.
Composite type
The composite type is to combine or use turbulent flow type and laminar flow type together, which can provide local ultra-clean air.
(1) Clean Tunnel: Use HEPA or ULPA filters to cover 100% of the process area or work area to increase the cleanliness level to above Class 10, which can save installation and operation costs.
This type requires the operator's work area to be isolated from the product and machine maintenance to avoid affecting the work and quality during machine maintenance.
Clean tunnels have two other advantages: A. Easy to expand flexibly; B. Equipment maintenance can be easily performed in the maintenance area.
(2) Clean Tube: Surround and purify the automatic production line through which the product flow passes, and increase the cleanliness level to above class 100. Because the product, operator and dust-generating environment are isolated from each other, a small amount of air supply can achieve good cleanliness, which can save energy and is most suitable for automated production lines that do not require manual labor. It is applicable to the pharmaceutical, food and semiconductor industries.
(3) Clean Spot: The cleanliness level of the product process area in the turbulent clean room with a clean room level of 10,000~100,000 is increased to 10~1000 or above for production purposes; clean workbenches, clean sheds, prefabricated clean rooms, and clean wardrobes belong to this category.
Clean bench: class 1~100.
Clean booth: A small space surrounded by anti-static transparent plastic cloth in turbulent clean room space, using independent HEPA or ULPA and air conditioning units to become a higher-level clean space, with a level of 10~1000, a height of about 2.5 meters, and a coverage area of about 10m2 or less. It has four pillars and is equipped with movable wheels for flexible use.
5. Airflow Flow
Importance of Airflow
The cleanliness of a clean room is often affected by airflow. In other words, the movement and diffusion of dust generated by people, machine compartments, building structures, etc. are controlled by airflow.
The clean room uses HEPA and ULPA to filter air, and its dust collection rate is as high as 99.97~99.99995%, so the air filtered by this filter can be said to be very clean. However, in addition to people, there are also dust sources such as machines in the clean room. Once these generated dusts spread, it is impossible to maintain a clean space, so airflow must be used to quickly discharge the generated dust outdoors.
Influencing Factors
There are many factors that affect the airflow of a clean room, such as process equipment, personnel, clean room assembly materials, lighting fixtures, etc. At the same time, the diversion point of the airflow above the production equipment should also be taken into consideration.
The airflow diversion point on the surface of a general operating table or production equipment should be set at 2/3 of the distance between the clean room space and the partition board. In this way, when the operator is working, the airflow can flow from the inside of the process area to the operating area and take away the dust; if the diversion point is configured in front of the process area, it will become an improper airflow diversion. At this time, most of the airflow will flow to the back of the process area, and the dust caused by the operator's operation will be carried to the back of the equipment, and the workbench will be contaminated, and the yield will inevitably decrease.
Obstacles such as work tables in clean rooms will have eddy currents at the junction, and the cleanliness near them will be relatively poor. Drilling a return air hole on the work table will minimize the eddy current phenomenon; whether the selection of assembly materials is appropriate and whether the equipment layout is perfect are also important factors for whether the airflow becomes an eddy current phenomenon.
6. Composition of clean room
The composition of clean room is composed of the following systems (none of which is indispensable in the system molecules), otherwise it will not be possible to form a complete and high-quality clean room:
(1) Ceiling system: including ceiling rod, I-beam or U-beam, ceiling grid or ceiling frame.
(2) Air conditioning system: including air cabin, filter system, windmill, etc.
(3) Partitional wall: including windows and doors.
(4) Floor: including elevated floor or anti-static floor.
(5) Lighting fixtures: LED purification flat lamp.
The main structure of the clean room is generally made of steel bars or bone cement, but no matter what kind of structure it is, it must meet the following conditions:
A. No cracks will occur due to temperature changes and vibrations;
B. It is not easy to produce dust particles, and it is difficult for particles to attach;
C. Low hygroscopicity;
D. In order to maintain the humidity conditions in clean room, the thermal insulation must be high;
7. Classification by use
Industrial clean room
The control of inanimate particles is the object. It mainly controls the pollution of air dust particles to the working object, and the interior generally maintains a positive pressure state. It is suitable for precision machinery industry, electronics industry (semiconductors, integrated circuits, etc.), aerospace industry, high-purity chemical industry, atomic energy industry, optical and magnetic product industry (CD, film, tape production) LCD (liquid crystal glass), computer hard disk, computer head production and other industries.
Biological clean room
Mainly controls the pollution of living particles (bacteria) and inanimate particles (dust) to the working object. It can be divided into;
A. General biological clean room: mainly controls the pollution of microbial (bacterial) objects. At the same time, its internal materials must be able to withstand the erosion of various sterilizing agents, and the interior generally guarantees positive pressure. Essentially, the internal materials must be able to withstand various sterilization treatments of industrial clean room. Examples: pharmaceutical industry, hospitals (operating rooms, sterile wards), food, cosmetics, beverage product production, animal laboratories, physical and chemical testing laboratories, blood stations, etc.
B. Biological safety clean room: mainly controls the pollution of living particles of the working object to the outside world and people. The internal pressure must be maintained negative with the atmosphere. Examples: bacteriology, biology, clean laboratories, physical engineering (recombinant genes, vaccine preparation)
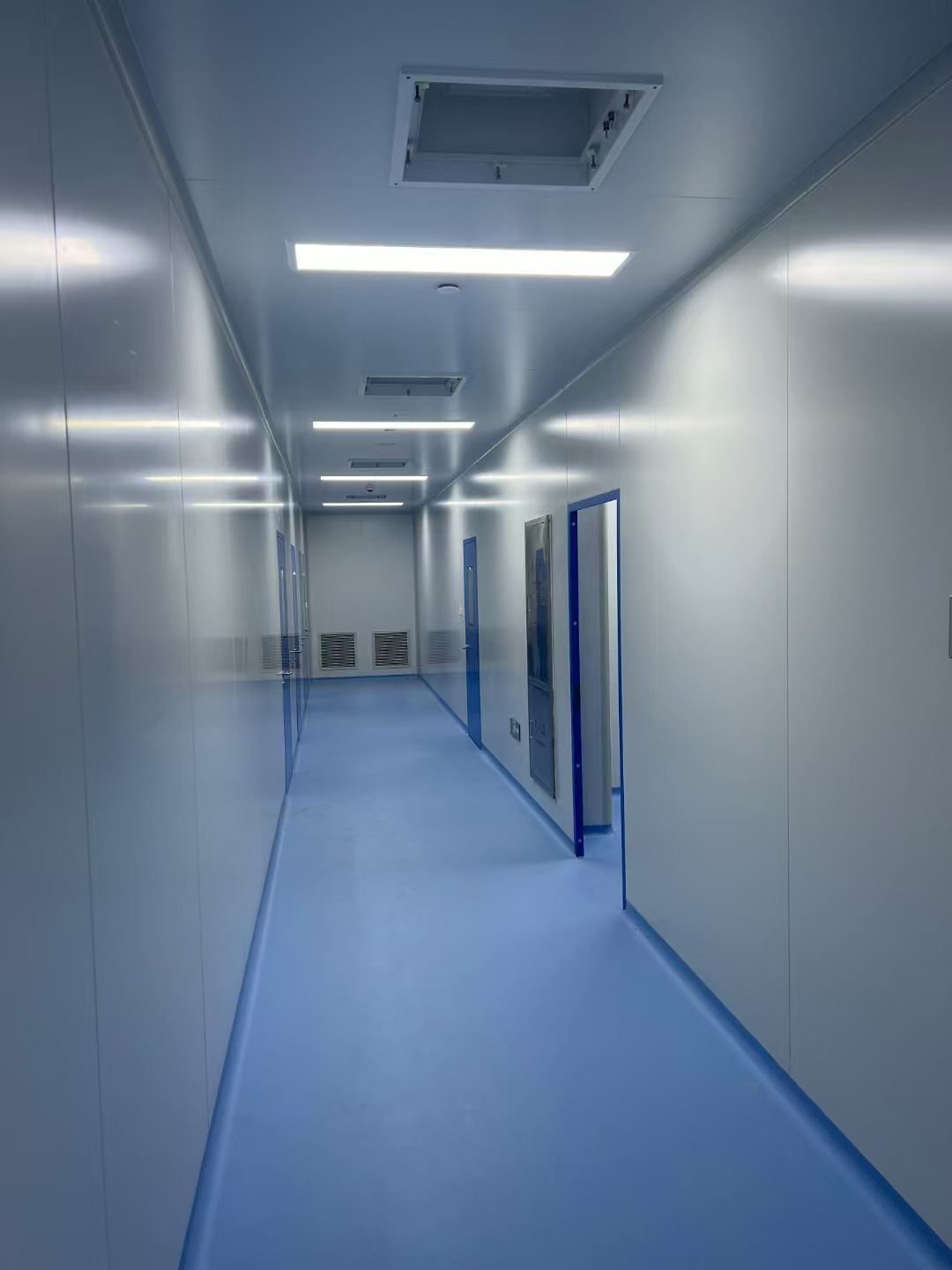
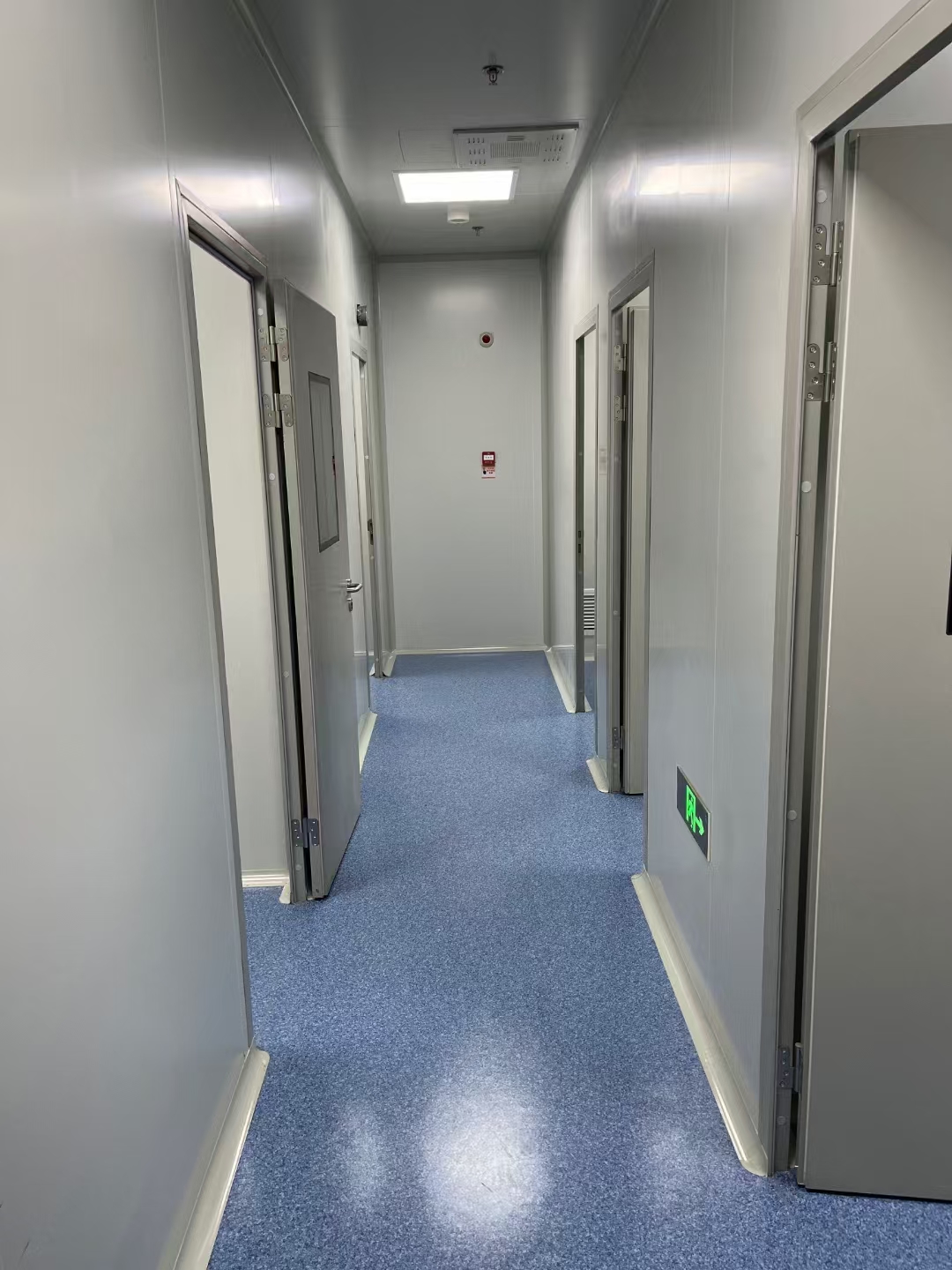
Post time: Feb-07-2025